Acrylics have remarkable optical clarity, durability, and adaptability as a highly favored glass substitute. Its widespread uses are available in distinctive forms and specifications for different manufacturing methods.
This article explores acrylic plastic manufacturing by breaking down the standard processes. Aside from knowing how acrylic is manufactured in fundamental detail, you’ll get to select the proper method.
What is Acrylic in Manufacturing?
Acrylic or plexiglass is a synthetic polymer originating from different acrylic acid derivatives. The most common derivative is the polymethyl methacrylate (PMMA). Also, there are other monomers like methacrylic acid.
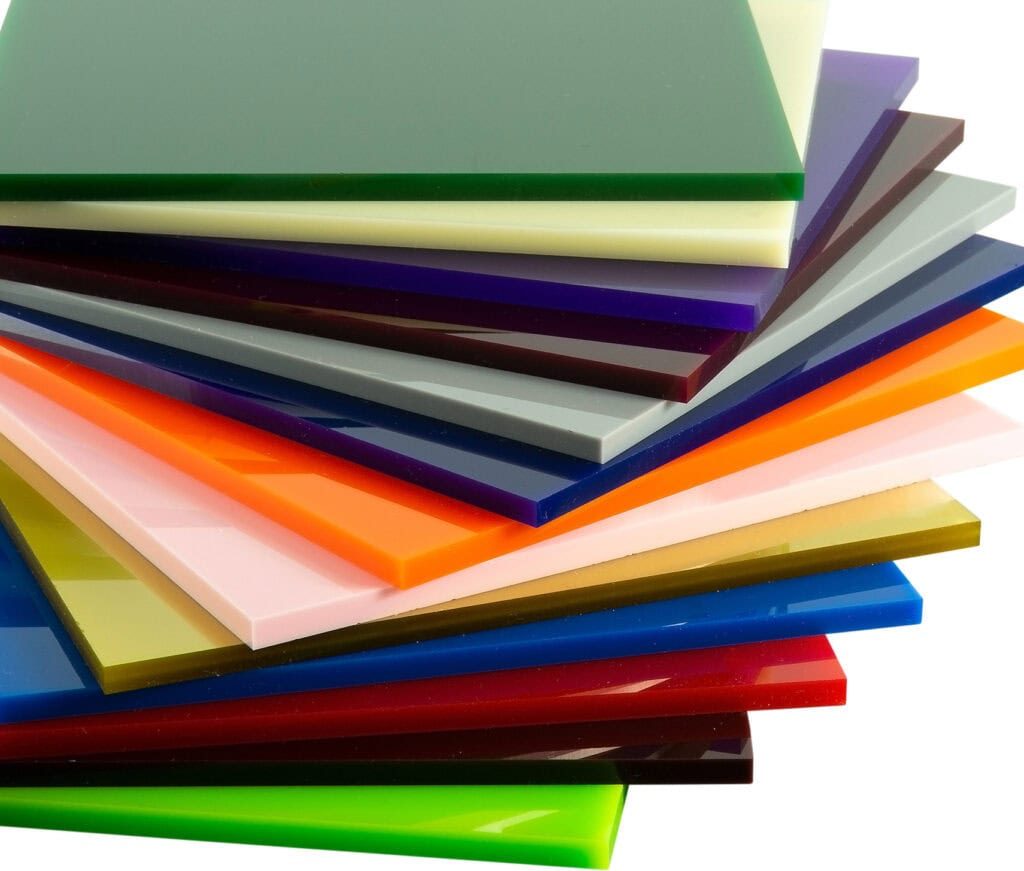
Physical Properties of Acrylics
- Transparent with high optical clarity (92% light transmission).
- Significantly lightweight (nearly half as heavy as glass materials).
- Excellent resistance to impact with noticeably tougher than glass.
- Scratch-resistant, but a scratched surface can be polished easily.
- Softens when heated to allow effortless shaping and molding.
Chemical Properties of Acrylics
- Chemically stable with good resistance to UV and weathering.
- Non-toxic and incredibly inert when fully polymerized.
- Soluble in standard organic solvents such as acetone.
- Combustible at high temperatures, producing CO2 and water.
Raw Materials for Acrylic Manufacturing
The precise production process of acrylic plastics features a blend of chemistry and engineering. It always starts with specific raw materials. They serve as the founding blocks for a usable plexiglass.
- Initiators: An organic peroxide like benzoyl/lauryl peroxide is the foremost example. The compounds initiate the polymerization process by breaking down into free radicals. Those radicals react with methyl methacrylate (MMA) molecules to form the polymer chain.
- Methyl Methacrylate (MMA): MMA is the primary monomer to produce PMMA. It’s a colorless liquid with a sharp odor. Acetone reaction with hydrogen cyanide (sodium cyanide) produces methyl methacrylate.
- The compound forms long polymer chains during polymerization. The long PMMA chain acts as the base material for acrylic plastic.
- Stabilizers: They prevent thermal degradation and yellowing of the PMMA during processing. Standard stabilizers for plexiglass manufacturing include antioxidants like hindered phenols.
- Processing Aids: Polyethylene glycol and stearic acid are the topmost examples of manufacturing aids. They improve the flow properties of the polymer during processing. Also, such compounds reduce potential surface defects in the manufactured plexiglass.
- Pigments and Fillers: Pigments add color to the clear acrylic material. Meanwhile, materials like glass fibers, calcium carbonate, or talc enhance mechanical properties such as strength and durability.
- Additives: UV stabilizers protect the highly transparent material from sunlight, extending its lifespan in industrial applications. Flame retardants improve fire resistance. Antistatic agents reduce static electricity buildup on the surface.
- Solvents: Acetone or other organic solvents are the prime examples of typical solvents. They take part in the preparation and purification of MMA. High-quality polymerization is obligatory to obtain the best possible outcome.
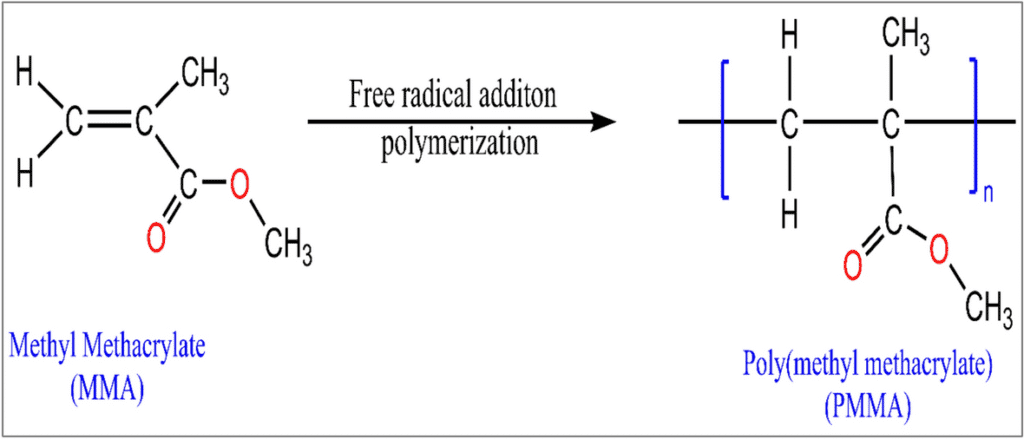
Careful combination and processing of the raw materials lead to usable PMMA. Meticulous selection, integration, and control of materials and additives let the final polymer meet the desired specifications.
A. Cast Acrylic Manufacturing (Casting Process)
It’s a methodical, detailed, and popular approach for high-quality acrylic sheets. The resulting plastic materials feature exceptional clarity and strength. It involves the following steps –
- Step #01 – Raw Materials: The process starts with methyl methacrylate (MMA) monomer. Stabilizers get mixed with MMA in proper proportions. The same goes for UV inhibitors and pigments (for colored sheets).
- Step #02 – Mold Preparation: The molds, usually made from two sheets of high-grade glass, hold a polished surface. It allows the final acrylic plastic to have a smooth surface.
- Rubber or plastic spacers between the sheets determine the thickness. Tight edge seals prevent contamination and leakage of the synthetic resin.
- Step #03 – Filling the Mold: The prepared liquid resin (mix of MMA and additives) gets poured or injected into the mold cavity. Gentle vibration or vacuum placement eliminates the air bubbles for optical clarity.
- Step #04 – Polymerization Process: The filled mold gets placed in a temperature-controlled water bath or oven. A gradual increase in temp initiates polymerization.
- It converts the liquid MMA into polymethyl methacrylate (PMMA). Exothermic polymerization requires careful control of temperatures to prevent warping or defects.
- Step #05 – Annealing: The manufactured acrylic plastic gets annealed (slowly cooled) to relieve all the internal stresses. This prohibits cracking or warping. The required periods vary depending on the sheet thickness, ranging from hours to days.
- Step #06 – Mold Removal: The molds are disassembled to remove the acrylic sheet upon full curing. Any residue from the mold is cleaned off. Also, close and careful surface inspection takes place to detect flaws.
- Step #07 – Finishing: The edges of the acrylic sheet get trimmed to the specified dimensions. It may undergo polishing to enhance the optical clarity. Additional processing like laser cutting, engraving, or drilling may take place.
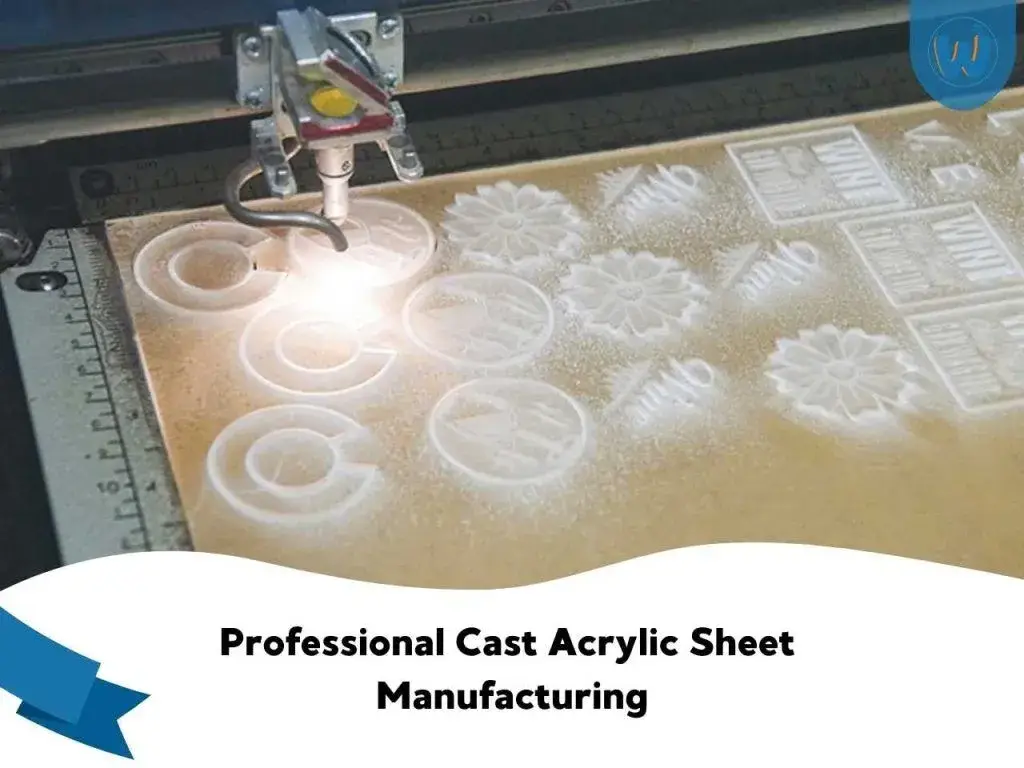
Advantages of Cast Acrylic
- Optical Clarity: These plastic materials possess exceptional transparency (up to 92%). It’s an ideal material for various applications involving visual appeal.
- UV Resistance: It exhibits excellent resistance to UV light and weathering. Durability prevails for the most common applications without degradation.
- Customizable Thickness: The manufacturing process allows different thinner thicknesses. That’s why cast plexiglass is quite versatile for various applications.
- High Impact Resistance: Acrylic plastic isn’t as tough as polycarbonate. Still, these acrylic plastics exert more impact resistance to offer safety and reliability.
- Ease of Fabrication: Manufacturers can easily cut, drill, machine, and thermoform engineering plastics. It allows intricate designs and shapes for decorative purposes.
- Chemical Resistance: The material features excellent chemical stability (and weathering). It retains the designated lifespan under notably adverse conditions.
Disadvantages of Cast Acrylic
- Brittleness: These engineering plastics are brittle despite being shatter resistant.
- Higher Cost: The production process is labor-intensive, making it more expensive.
- Flammability: Combustible plexiglass may catch fire at elevated temperatures.
- Surface Susceptibility: It’s prone to surface damage over time (industrial applications).
Applications of Cast Acrylic
- Signage and Displays: illuminated signs, logo panels, and POP displays.
- Furniture: high-end pieces, tabletops, and design items.
- Architectural Uses: windows, skylights, partitions, and decorative panels.
- Art and Design: sculptures and creative installations.
- Medical: optical lenses, dental appliances, and enclosures for medical devices.
- Marine Industry: aquarium walls and boat windows.
- Automotive Industry: instrument panels, light covers, and vehicle windows.
- Aerospace: cockpit canopies and instrument covers.
B. Extruded Acrylic Manufacturing (Extrusion Process)
It’s an effective process to produce acrylic sheets, rods, and tubes with uniform thickness. It involves melting acrylic resin and shaping it continuously through extrusion. It features the following steps –
- Step #01 – Acrylic Resin: The process begins with acrylic plastic resin in small pellets or granules. The granules or pellets mainly originate from polymethyl methacrylate (PMMA). It gets mixed with stabilizers, pigments, and UV inhibitors for specific properties.
- Step #02 – Feeding the Extruder: The acrylic resin pellets get poured into a hopper. It feeds the material into the extruder machine. The flow of pellets is regulated for uniform processing without gaps in the material.
- Step #03 – Heating and Melting: The resin gets transported through a heated barrel in the extruder for gradual melting. The barrel with multiple heating zones enables careful control of temperatures. Typical temperature ranges between 150°C to 230°C to avoid degradation.
- Step #04 – Mixing and Homogenization: Rotating screws mix the molten resin within the extruder for uniform consistency and color dispersion. Any trapped air or gas in the resin gets removed at this stage to maintain clarity and strength.
- Step #05 – Extrusion Through a Die: The molten acrylic plastic gets forced through a precisely designed die. It shapes the resin into sheets, rods, or tubes. Flat dies form continuous acrylic sheets, whereas cylindrical dies create rods and tubes. Adjusting the die dimensions can produce thicker sheets of material.
- Step #06 – Cooling and Solidification: The acrylic plastics (extruded sheet) pass through chilled rollers (calender rolls) for cooling. Meanwhile, air or water solidified the extruded shapes (tubes or rods). The gap between the rollers controls the thickness of the flat sheets.
- Step #07 – Cutting and Trimming: Manufacturers cut the cooled acrylic plastic into desired lengths or shapes using laser cutting. Edges get properly trimmed and polished to meet the specific requirements.
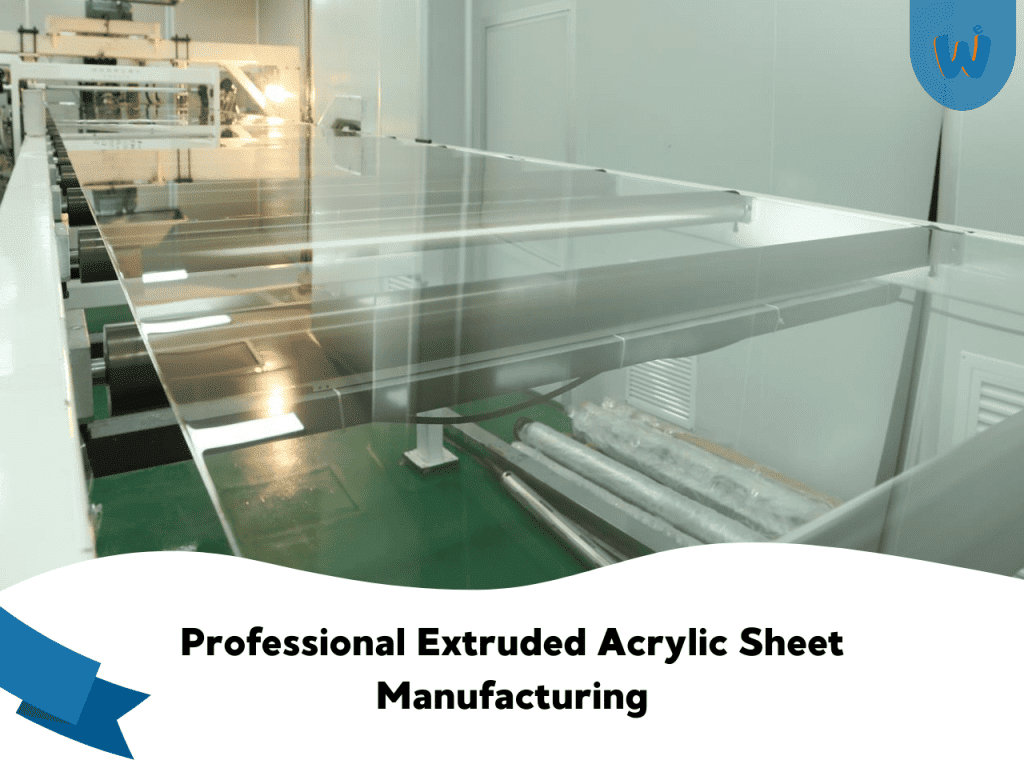
Advantages of Extruded Acrylic
- Cost Effective: The highly efficient process makes acrylic polymers (extruded) cheaper.
- Consistency: It offers uniform thickness and dimensions across the entire plexiglass product.
- Production Speed: Extrusion is a continuous method that enables high-volume production.
- Ease of Handling: Acrylic polymers (extruded) are lightweight and easy to cut, shape, and form.
- Customization: Available in different sizes, shapes, and colors to cater to diverse requirements.
Disadvantages of Extruded Acrylic
- Lower Optical Clarity: Impurities make it slightly less clear than other engineering plastics.
- Less Weather Resistance: They may not withstand prolonged exposure to UV and harshness.
- Brittleness: It’s more prone to cracks or breaks. These acrylics have less impact resistance.
- Surface Susceptibility: They’re susceptible to scratching and scuffing, making them less durable.
- Limited Thickness Range: Extrusion methods may not allow for various thicknesses.
Applications of Extruded Acrylic
- Retail Displays: point-of-purchase (POP) displays and protective shields.
- Lighting Fixtures: diffusers and light covers for their glass-like qualities.
- Consumer Goods: picture frames, signage, and protective electronic covers.
- Construction: lightweight window glazing and decorative panels.
- Automotive Industry: light lenses, interior trim pieces, and sunroof glazing.
- Furniture Design: lightweight furniture components and partitions.
- Packaging: transparent, durable packaging materials.
- DIY Projects: custom creations like terrariums or craft enclosures.
Special Acrylic Manufacturing Methods
Additional manufacturing mainly involves injection molding, continuous bulk polymerization, and suspension polymerization.
I. Injection Molding
It’s a versatile technique for large quantities of complex acrylic plastic materials. Injection molding comes with the following steps –
- Material: Acrylic pellets (PMMA) get fed into an injection molding machine.
- Heating: The pellets are heated in a barrel. The heat melts the pellets into a viscous liquid.
- Injection: The molten acrylic gets injected into a mold cavity under elevated pressure.
- Cooling: The mold is cooled down to allow the acrylic to solidify into the specified shape.
- Ejection: The finished acrylic product gets ejected or removed carefully from the mold.
- Finishing: The parts may undergo additional processes like trimming and/or polishing.
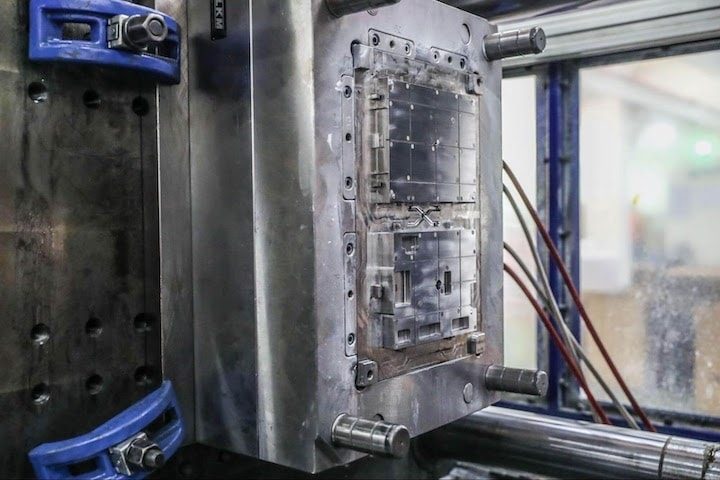
Benefits of Injection Molding
- Complex and intricate designs with precision.
- Superb efficiency in mass production.
- Minimal material wastage during the process.
- Flexibility in shapes, sizes, and textures.
Limitations of Injection Molding
- Not suitable for low-volume production.
- Expensive mold design and tooling.
- Limited to components of smaller widths.
Applications of Injection Molding
- Automotive parts (dashboards and headlamp covers).
- Medical devices (syringes and housings).
- Consumer goods (toys, decorative items, and appliances).
II. Suspension Polymerization
It’s a chemical process that manufactures beads or granules from acrylic acid. Those items are later processed into finished products. The involved steps are –
- Preparation: The methyl methacrylate molecule gets dispersed in water by a suspending agent.
- Polymerization: MMA molecules are polymerized with initiators to form PMMA beads.
- Cooling: The chemical reaction gets controlled and cooled down to maintain uniformity.
- Separation: The PMMA beads get filtered out of the solution and adequately washed.
- Drying: The beads are dried to prepare them for storage and/or further processing.
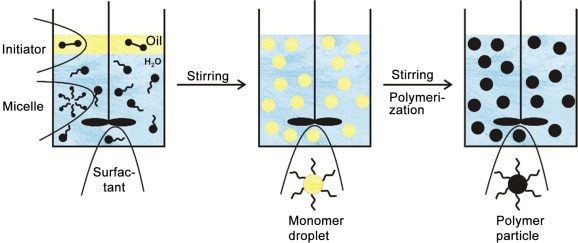
Benefits of Suspension Polymerization
- Produces acrylic beads of uniform size.
- Beads are easy to handle, store, and transport.
- Low-cost process with scalable output.
- High versatility for downstream applications.
Downsides of Suspension Polymerization
- Additional processing to turn beads into usable forms.
- Limited customization during the initial polymerization.
- Lower optical clarity than direct methods like casting.
Applications of Suspension Polymerization
- Raw material for extrusion and injection molding.
- Adhesives, sealants, and coatings.
- Creating consumer and items for various industries.
III. Continuous Bulk Polymerization
It enables large-scale acrylic sheet production with minimal solvents and additives. The transparent plastic materials-making process features the following steps –
- Preparation: Methyl methacrylate monomer gets mixed with initiators and stabilizers.
- Continuous Polymerization: The monomer is polymerized with heat and pressure in a reactor.
- Sheet Formation: The polymerized acrylic plastic gets fed through rollers to form sheets.
- Cooling: The sheets are cooled down to solidify the produced material.
- Cutting and Finishing: The sheets get cut into precise dimensions through laser cutting.
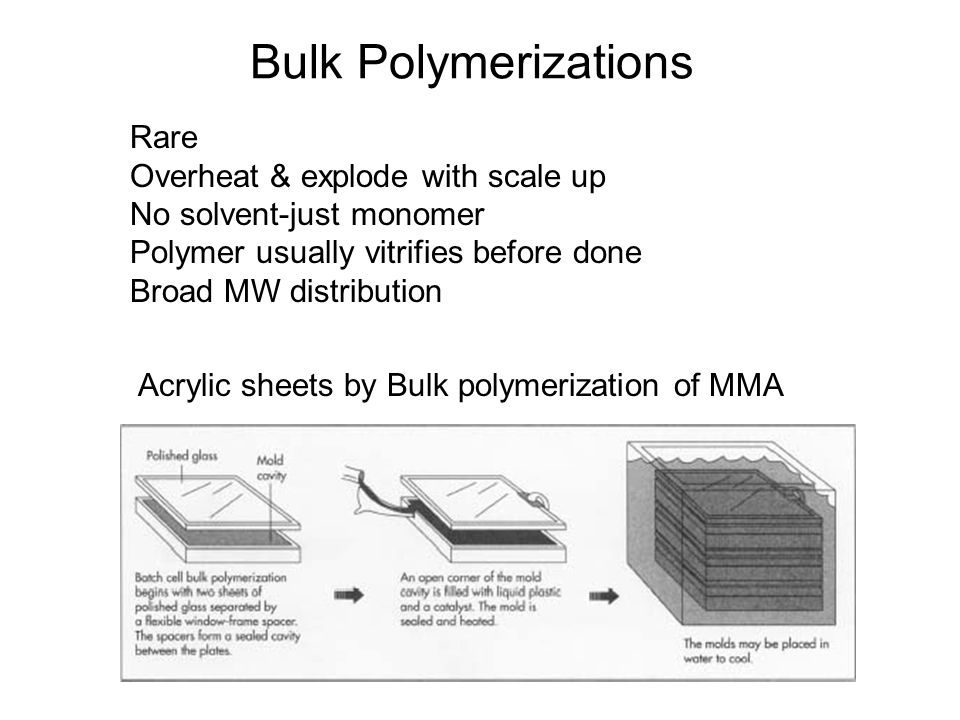
Advantages of Bulk Polymerization
- High production efficiency and consistency.
- Environmentally friendly with minimal solvent usage.
- Production of large, uniform acrylic sheets.
- Low operational cost once the setup gets established.
Downsides of Continuous Bulking
- Limited flexibility in shapes and designs.
- High initial equipment and setup costs.
- Quality is less customizable than casting.
Applications of Continuous Polymerization
- Architectural panels and windows.
- Industrial and decorative components.
- Signage and/or advertising boards.
How to Choose the Best Acrylic Manufacturing Method?
Choosing the best manufacturing method for acrylic plastic materials depends on multiple factors. You can easily select the right one for your project with the following considerations –
- Product Requirements: Start by outlining the specific characteristics and features. Aquariums, lenses, and display cases rely on engineering plastics.
- Extrusion seems more suitable for consistency (protective shields/display cases). Consider injection molding for intricate shapes (automotive parts or decorative items).
- Consider the Application: Each application with unique demands should guide your choice. The plastic material, resistant to UV light, is preferable for outdoor signs or skylights.
- Acrylic polymers (extruded) are cost-effective for high-volume industrial needs. And injection molding seems excellent for precise and detailed components.
- Production Volume: The chosen method chosen must align with production scales. Casting goes well with small production runs, prioritizing customization and quality over speed. Continuous polymerization and extrusion are more economical due to speed and efficiency.
- Material Properties: Choose a method based on the physical and mechanical properties. Engineering plastics from casting are strong and resistant to heavy loads.
- They also offer smooth finishes, whereas acrylic plastics (extruded) may need additional finishing. But acrylic plastic sheets (extruded) are more flexible, making them suitable for bending and shaping.
- Customization Needs: The ability to customize size, shape, thickness, and color also influences your decision. Cast acrylic is an ideal material for variable thicknesses and colors. The versatile material (extruded) seems better for standard sheets, rods, or tubes with consistent dimensions.
- Turnaround Time: The speed of the manufacturing process becomes critical for tight deadlines.
- Extrusion and bulk polymerization can accommodate time-sensitive production. Engineering plastics from casting takes longer due to curing and polishing, often delaying the timelines.
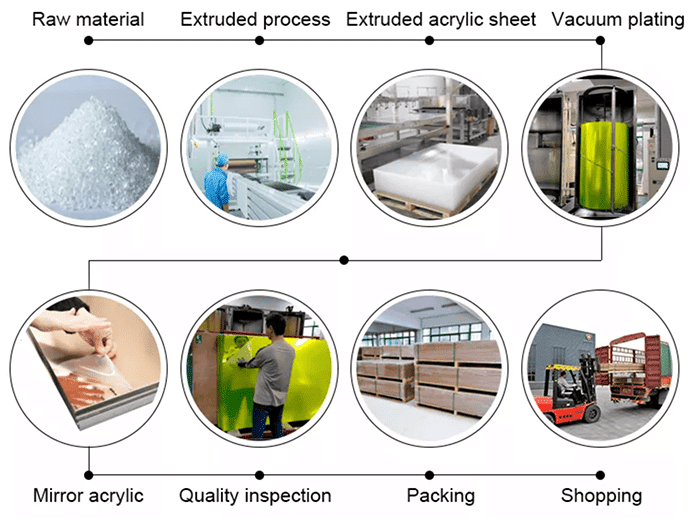
Conclusion
Different acrylic plastic manufacturing involves distinctive materials, steps, and processing. They differ in advantages, limitations, and application to a significant extent.
Selecting the right option (whether casting, extrusion, or polymerization) ensures the desired durability, versatility, and usability. Also, maintaining rigorous quality control and customization options should be available for specific needs.
Choose JUMEI as Your Professional Acrylic MAnufacturing Partner
Jumei Acrylic Manufacturing stands on top of the global competition. We have the best standards, expertise, and tools to deliver the most precise engineering plastics for your projects. Contact us now to receive professional suggestions for your next project.