Acrylic has widespread applications in modern industries. Its versatility, durability, and clarity have been a preferred choice for demanding projects. However, the thickness of Plexiglas is one crucial factor in determining the overall performance.
This article looks into the importance of selecting the appropriate acrylic value. You’ll get to know its influence on design, capacity, and resilience. Even proper guidance on custom solutions is there to meet your diverse project requirements.
Meaning of Thickness in Plexiglas
It refers to the measurement of how thick a product is. It indicates the distance between two flat surfaces, perpendicular to the plane of the sheet. The measurement is mostly expressed in millimeters (mm) or inches (in).
For instance, a 3mm sheet indicates a thickness of 3 millimeters. The value can range from ultra-thin sheets (1mm) to much thicker (50mm+). Manufacturers maintain standard thicknesses for specified applications.
- Thin Sheets (1mm to 5mm): Lightweight and flexible. Uses in signs, displays, and small crafting projects.
- Medium Values (6mm to 20mm): Strong and flexible. Suitable for aquariums, furniture, acrylic shower wall panels, and architecture.
- Thick Sheets (≥ 25mm): Durable and rigid. Uses in structures, barriers, or heavy-duty industrial designs.
Accurate measurement is obligatory for access to the best result. It’s primarily measured through tools (calipers or micrometers). Such tools create consistency, especially in industries where precision is vital.
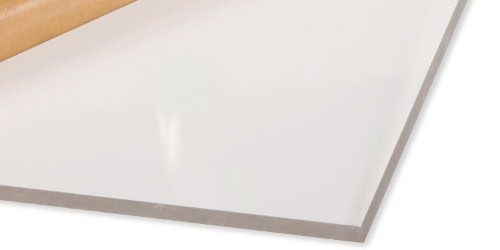
Why is the Dimensional Metric So Important?
- Mechanical Strength: Thicker sheets have greater resistance to forces (bending, impact, and vibration). Such materials are ideal for applications like acrylic shower wall panels, barriers, structural components, or furniture.
- Optical Properties: The metric influences transparent plexiglass clarity, color, and light transmission. Thin sheets are lightweight enough to create maximum light penetration (not for acrylic shower panels). But thicker sheets may exhibit subtle color shifts.
- Thermal Properties: Acrylic has moderate thermal resistance. Thicker sheets can handle temperature changes effectively. This makes the plastics suitable for outdoor applications involving fluctuating temperatures.
- Weight: It also contributes directly to its weight. Thicker sheets are heavier, making it a key consideration for acrylic shower wall panels. Applications, where weight affects functionality (automotive or aerospace), have to take precise measures.
- Acoustic Insulation: Thicker plexiglass provides better soundproofing compared to thinner sheets. This particular property seems beneficial in applications like sound barriers, enclosures, and/or acrylic shower panels.
Factors Related to the Selection
Selecting the appropriate value for the dimensional metric is a critical decision. It’ll eventually influence the sheet’s performance, functionality, and appearance. And the concerning factors would be –
- Intended Use/Application: The specific use heavily dictates its required value. The values can vary based on applications, determining how well the material can serve.
- Load-Carrying Requirements: The physical ability of the acrylic sheet is always a key consideration. It involves optimal weight limits, sufficient pressure handling, and steady structural stability.
- Environmental Exposure: Likewise, where and how the acrylic will be employed has a role in the selection process. You must keep indoor/outdoor uses, UV resistance, and temperature changes in mind.
- Installation Method: The method of mounting or supporting an item has been an overlooked factor. However, thicker sheets require significant installation and support considerations.
- Safety Concerns: It’s one of the driving factors for high-risk environment applications. That’s how manufacturers create plexiglass with sufficient resistance to shattering and brittleness.
- Aesthetic Considerations: Visual appeal also guides the decision, mostly for design-focused applications. Optical clarity, visual balance, and long-term strength are quite important.
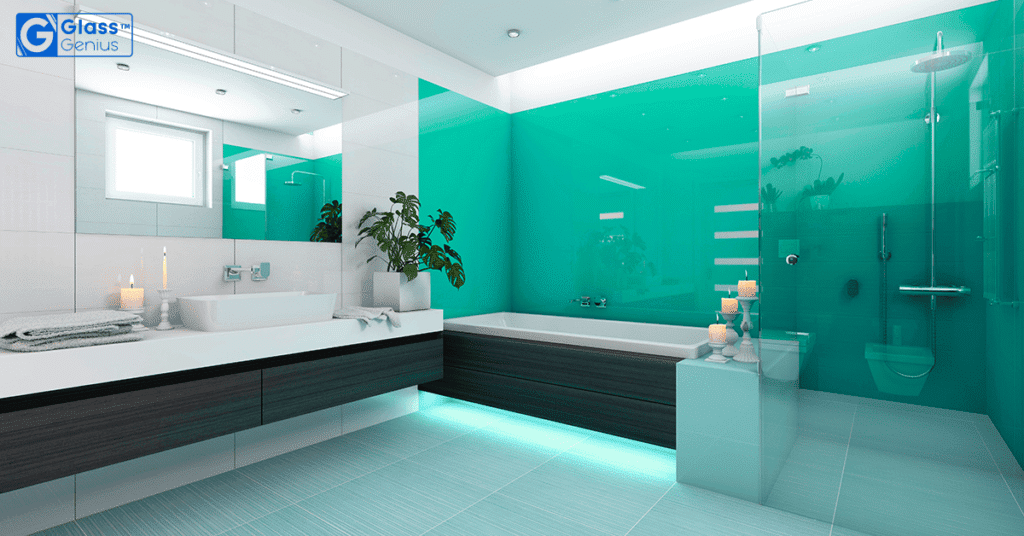
How Does the Value Influence the Durable Material (Plexiglass)?
Each application requires careful assessment to initiate the optimal balance between the metric and other factors. Use, weight, optical clarity, fabrication, and cost are the foremost factors to remember.
- For signage, thin sheets (1mm – 3mm) are suitable for indoor uses. Thicker sheets (5mm – 10mm) are better for outdoor signs to endure wind and weather.
- Acrylic barriers (sneeze guards or protective shields) require a medium (4mm – 6mm) to balance transparency with impact resistance.
- For acrylic shower wall panels, windows, or skylights – thicker sheets (6mm – 12mm) can ensure insulation, optical clarity, and resistance to external forces.
- Medium sheets (8mm – 15mm) for furniture like tables and/or shelves provide adequate load-carrying capacity. They can maintain the required aesthetic appeal.
- Furniture or display cases may need thicker sheets (10mm – 20mm or more) to hold the loads without bending.
- Acrylic shower wall panels, aquariums, or water tanks must withstand the water pressure. That’s why the value must correspond to the tank size and water volume (20mm+ sheets for large tanks).
- Outdoor applications demand thicker sheets due to exposure to wind, rain, and potential impacts. Outdoor sheets are UV-stabilized to prevent yellowing or brittleness over prolonged sun exposure.
- Thicker sheets with UV protection are preferred for settings like greenhouses or advertising signs.
- Extreme temperature fluctuations require thicker sheets against warping or cracking. Applications in cold climates often employ thicker sheets for added insulation.Also, glazing in metal or wooden frames may not require unnecessarily thick sheets.
- Acrylic sheets in hanging displays or partitions need more (6mm or more) to prevent sagging. For adhesive-mounted applications, thinner sheets with sufficient strength seem more dependable.
- In contrast, a screwed/bolted installation benefits from medium-to-thick sheets for mechanical fastening (acrylic shower wall panels).
- Areas prone to accidental impacts (acrylic shower wall panels, retail barriers, or industrial shields) need thicker sheets.
- A 6mm to 12mm material doesn’t break, unlike other forms. Acrylic’s natural shatter resistance is superior to glass, but applications like bulletproof barriers may need ultra-thick sheets (20mm – 40mm) for security.
- Thinner sheets are preferred for sleek and minimalist furniture/displays. Thicker sheets can still convey high end serviceability. Thicker values can introduce slight optical distortion or color tint.
- Applications where customers are interested in items like tabletops may need thicker sheets.
Designers and engineers choose the thinnest possible sheet without compromising the functionality details. It’s especially true when weight reduction and/or expenses become the priorities.
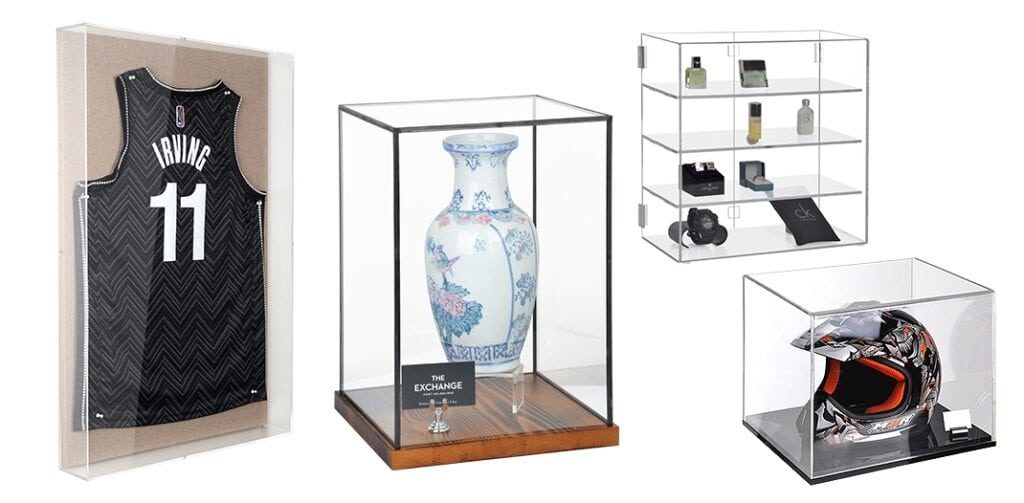
Cast vs Extruded: Impact on the Value
Two of the most common acrylic types are – cast acrylic and extruded acrylic. The type significantly influences tolerances, consistency, and suitability.
- Surface Variation: Cast sheets may exhibit slight variations in smooth surfaces and finish due to the molding process. The extrusion process enables superior consistency with a smooth surface throughout the sheet.
- Thickness Tolerance: It refers to the allowable variation in the sheet across the surface. Cast acrylic sheets feature considerable variations across the sheet. And tolerances are usually larger than those of extruded sheets (about ±10%).
- Extruded acrylic from a highly controlled production leads to tighter tolerances (±5%) at greater uniformity.
- Optical Quality: Cast acrylics create superior optical clarity compared to extruded sheets for visually aesthetic uses. Despite being uniform, extruded sheets may not have the same optical clarity due to some minor internal stresses.
- Precision Concerns: The manual nature of casting presents difficulty in achieving exact values. Cast sheets may exhibit slight inconsistencies, especially in uniformity-based applications.
- The consistent mechanical process keeps the variations to a minimum. Extruded acrylic sheets seem more beneficial for high-precision applications due to low variation and tight tolerances.
- Property Uniformity: The surfaces are clear but the inherent variations can introduce issues in terms of exact dimensions. However, extruded sheets maintain consistency in the physical properties and repeatability for mass production.
Acrylic Applications Requiring Exactness
Demanding applications often require exact dimensional measurements. And extruded acrylics have the upper hand due to precise manufacturing with tighter tolerances. Expert recommendations for exact applications imply –
- Industrial Parts: Components requiring uniformity for assembly fit (machine guards).
- Mass Production: Repeatability for applications with identical parts (signage and/or frames).
- Fabrication: Processes like laser cutting and CNC routing benefit from consistent values.
Cast acrylic may lack precision in values to some extent. However, it excels in applications requiring exceptional optical clarity and surface finish (aquariums, decorative panels, or designs). Such projects barely need tight tolerances.
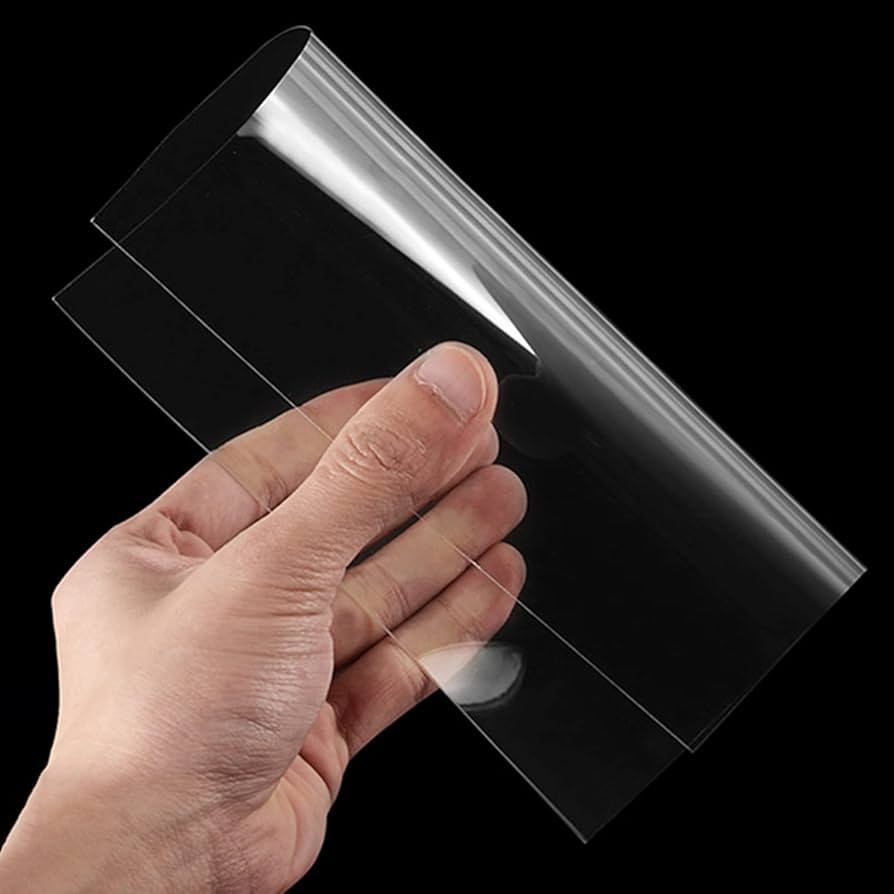
Mistakes to Avoid with Acrylic Sheets
Choosing the acrylic metric are critical task for everyone involved. However, several common mistakes can lead to functional or aesthetic issues, increased costs, or safety concerns.
- Ignoring Application-Specific Requirements: One of the most frequent errors is selecting a value without knowing the specific demands. Choosing a sheet that is too thin for heavy loads or impact resistance isn’t high end.
- The acrylic may eventually fail, crack, or deform. Understand the intended use and environmental factors for selection.
- Overestimating The Specifications: Selecting unnecessarily thick sheets can increase costs, weight, and complexity with no functional benefits. Overly thick sheets are harder to install and handle.
- They may limit the design flexibility. Perform a cost-benefit analysis and choose the thinnest sheet that satisfies your overall functional requirements.
- Overlooking Weight Considerations: Forgetting the weight of thicker acrylic sheets can result in logistics-related challenges. Excessive weight complicates mounting or hanging methods.
- They may even require additional support structures. Account for the weight and its implications for installation, especially in suspended or mounted applications.
- Disregarding Environmental Exposure: Many underestimate how environmental factors (UV radiation, temperature fluctuations, and humidity) can impact plexiglass.
- Thinner sheets may warp or become brittle when exposed to harsh outdoor conditions. Choose thicker acrylic for outdoor applications like greenhouses or signage for durability.
- Neglecting Safety Standards: Ignoring the considerations can lead to inadequate protection in terms of impact resistance or shatter-proofing. Selecting too thin sheets for barriers/shields may compromise intactness.
- Meanwhile, choosing glass-like materials without proper inspection risks shattering. Evaluate industry requirements and use thicker sheets.
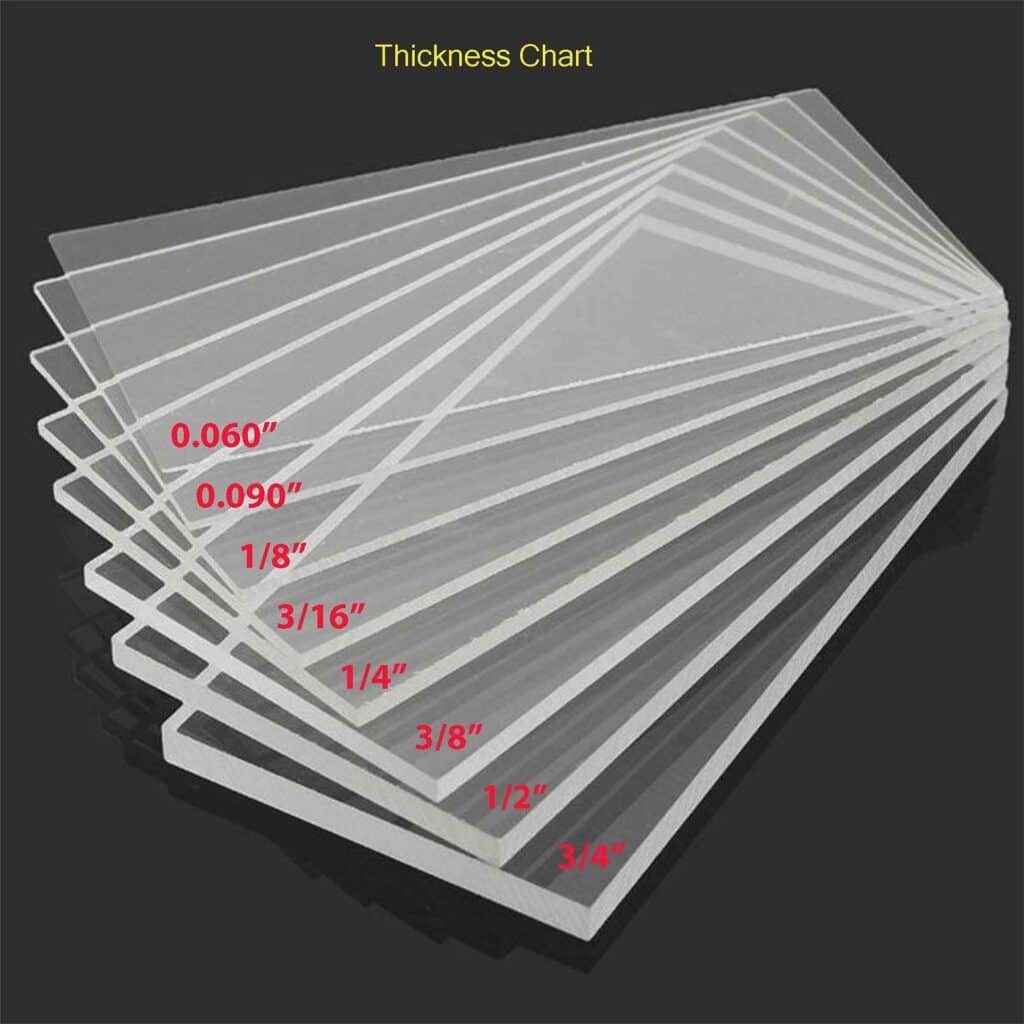
Custom Solutions for the Metric
Customized solutions for acrylic provide the flexibility to meet the exact project needs. From custom-cut sheets to collaborating with manufacturers, these solutions solve design and engineering issues. It results in creativity and precision in every aspect.
Standard sheet thicknesses range from 1mm to 50mm and sometimes, more. However, specific projects may require sizes beyond these limits or variations within the standards. Custom-cut solutions create precise adjustments to meet unique specifications.
Benefits of Custom-Cut Acrylic
- Exact Fit: Custom sizing enables the perfect fit of the dimensions for specialized applications. Additionally, it eliminates the need for trimming or adjustments.
- Enhanced Precision: Custom cuts are ideal for projects requiring intricate shapes or non-standard dimensions. Architectural designs or custom furniture are the prime examples.
- Waste Reduction: It also involves cutting sheets to the desired value. Material waste becomes minimal, leading to a more cost effective solution.
Common Custom-Cut Acrylic Applications
- Interior Design: Tailored sheets for creative brand furniture, wall partitions, or artistic installations.
- Technical Projects: Engineering projects with precision (mechanical components or enclosures) from custom solutions.
- Retail Displays: Custom shapes and sizes enable uniqueness in brand signs and point-of-sale displays.
Engineering designs, especially complex or sensitive ones, demand plexiglass with non-standard thicknesses. It makes manufacturers push the boundaries of conventional details. Customization enables optimal performance for strength, flexibility, and aesthetics.
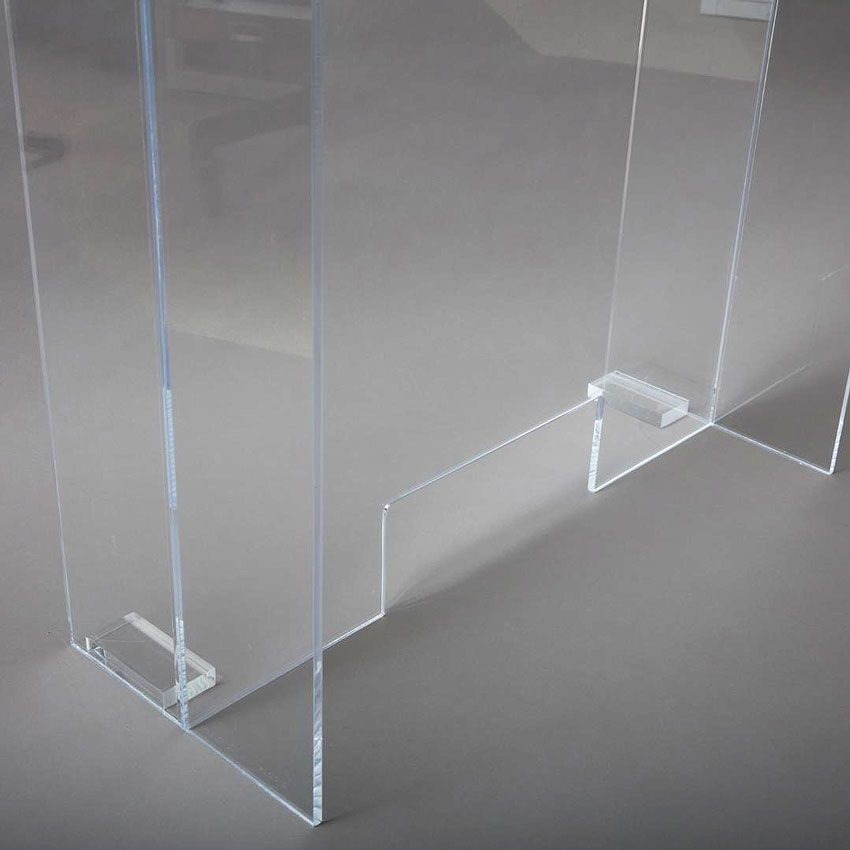
Key Considerations for Customization
- Load Requirements: Engineering projects (structures or partitions) need calculated values. It can achieve the desired strength without overburdening the design.
- Fabrication Specifications: Laser cutting, thermoforming, and engraving are the common fabrication methods. They may necessitate specific thicknesses for compatibility with tools/techniques.
- Visual Precision: There are widespread applications of Plexiglas like glazing or aquarium panels. Such customization accommodates optical clarity and/or longevity.
Examples of Customized Solutions
- Vehicle Design: Plexiglas is purchased by automotive designers with tailored values for aesthetics. The same goes for structural needs in dashboards or light covers.
- Marine Applications: Customers often contact for sheets with custom thicknesses. The purchased material must withstand underwater pressure and/or marine conditions.
- Industrial Machinery: Acrylic sheets with specific values are for secure enclosures. And it’s no different for advanced control panels in heavy-duty machinery.
Frequently Asked Questions (FAQs)
01. What is the difference between acrylic and glass?
Plexiglass is highly considered a substitute or alternative to glass. Both transparent materials have widespread applications. But they differ in properties to a great extent.
- Material Composition: Acrylic derives from polymethyl methacrylate (PMMA). As a plastic, acrylic is also a synthetic material designed for versatility.
- Glass originates from silica (sand). The natural yet inorganic material undergoes melting and cooling to achieve transparency.
- Strength and Durability: Acrylic is more impact-resistant than glass. Therefore, plexiglass doesn’t shatter easily.
- Upon breaking, Plexiglas forms large-sized dull edged pieces (safe for kids). Glass is more prone to shattering under impact, creating dangerous shards with a sharp edge.
- Weight: Acrylic is about 50% (almost half) lighter than glass, allowing easy transportation, handling, and installation.
- Displays or partitions heavily rely on the material. Meanwhile, glass-like materials are considerably difficult to employ for large, outdoor, and harsh conditions.
- Optical Properties: Acrylic offers exceptional clarity, allowing up to 92% light transmission. It maintains transparency without developing a greenish tint of thicker glass.
- Despite being transparent, thicker glass tends to develop a slight greenish hue due to the higher density.
- Resistance to Elements: Plexiglass is resistant to UV light. They can withstand prolonged sun/UV exposure without yellowing. It makes plexiglass ideal for outdoor applications.
- Glass is incredibly durable and inert. But untreated glass may deteriorate faster under natural influence.
- Cost Considerations: Acrylic is generally more affordable than glass, especially for large-scale projects.
- It’s also efficient to install because of its lighter note (lightweight). Glasses may seem quite problematic and expensive for somewhat complex/intricate tasks.
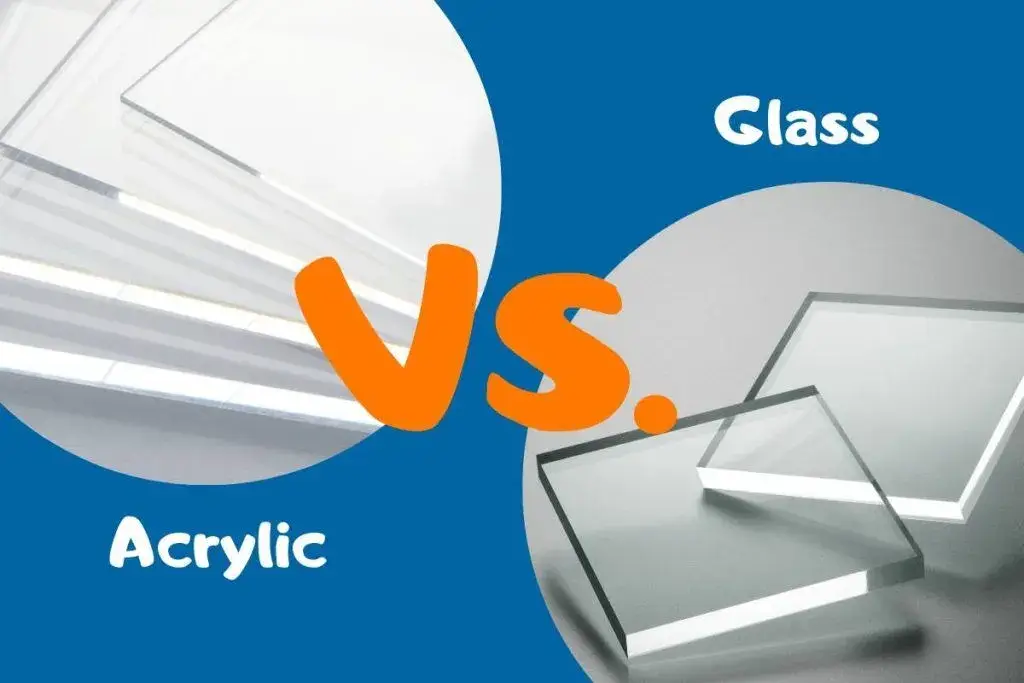
02. Can acrylic sheets be used outdoors?
Yes. Acrylic sheets are highly suitable for outdoor use. It’s because the material possesses durability and weather-resistant properties, like –
- UV Stability: The durable material is mostly UV-stabilized. It prevents yellowing or brittleness caused by prolonged sun exposure.
- Weather Resistance: Acrylic is highly resistant to rain, wind, and temperature fluctuations. It’s an ideal option for outdoor signage, roofing, or barriers.
- Applications: Common outdoor applications include greenhouses, pergolas, canopies, and exterior decorative panels.
03. How do I clean and maintain acrylic sheets?
Proper cleaning and maintenance keep acrylics clear and scratch-free. Careful cleaning requires –
- Mix lukewarm water with mild soap. Gently wipe the sheet with a non-abrasive, soft cloth. Don’t use ammonia-based cleaners (glass cleaners). Chemical agents can damage the acrylic surface. Use microfiber cloths instead of rough sponges or paper towels to avoid creating scratches.
That’s for cleaning. You’ll need to maintain the sheets through some measures. And the tips include –
- Buff out all the minor scratches using plastic polish or a scratch-removal kit. There are kits specifically designed for acrylic. Prevent accidental damage by placing plexiglass in any stable installations.
- Choose a place where they’re less prone to knocks. Periodically check for signs of wear for outdoor Plexiglas. Replace when necessary to maintain clarity and durability.
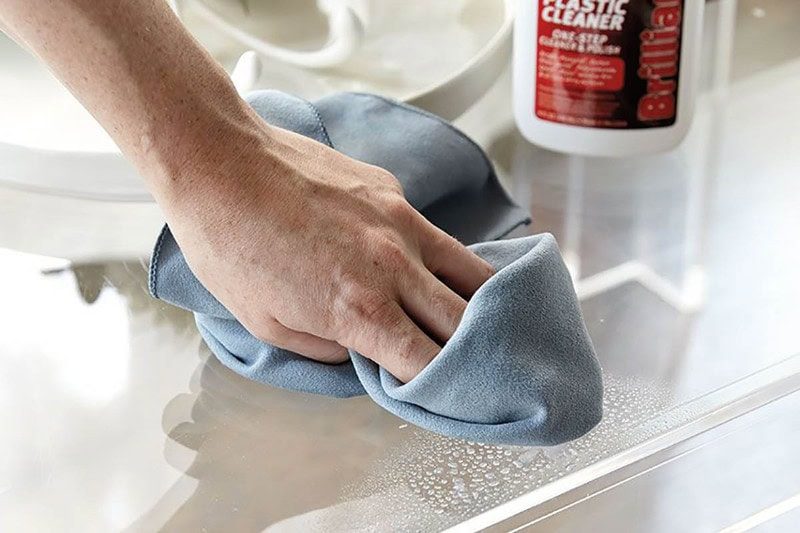
04. Are acrylic sheets recyclable?
Yes. Modern manufacturing makes the products recyclable. Recycling acrylic reduces waste and the need for new raw materials, turning it into an eco-friendly option. Although the recycling process is considerably complex compared to other materials.
Acrylic is initially recycled by melting down and repurposing the material into new sheets or products. Some specialized recycling facilities accept acrylic but standard curbside recycling programs might not process it.
Conclusion
The correct thickness can ensure functionality, durability, and aesthetics. It doesn’t matter whether the acrylics are for signage, furniture, or protective barriers. It greatly affects structural integrity, safety, access, and optical quality. That’s why evaluating your needs based on factors like loading limit, environmental exposure, and design objectives is mandatory to select the optimal value.
Get Your Perfect Sheet from JUMEI ACRYLIC
Are you looking for safe and practical solutions with a balance of creativity and aesthetics? Jumei Acrylic Manufacturing is ready to deliver a seamless outcome for your utmost satisfaction.
For standard to tailored acrylic products, our years of experience from industry-leading experts are ready to roll. Contact us without hesitation for professional suggestions and/or recommendations for your project.