Acrylic has been one of the foremost materials used across many industries, from signage and displays to furniture and architecture. It offers exceptional clarity, durability, and lightweight, specifically in sheet form.
That’s why acrylic sheets are more like a high-performing alternative to glass materials. Its applicability continues to expand due to its functionality, aesthetics, and customization. And this article takes a closer look at acrylic sheets.
It explores what makes acrylic sheets stand out, how custom acrylic solutions can help, and why you should choose Jumei. We can help anyone needing acrylic sheets, from designers to fabricators and business owners.
What is an Acrylic Sheet?
Acrylics are synthetic polymers (plastics) of methyl methacrylate. Manufacturers also sell the product as Plexiglass, Polymethyl Methacrylate (PMMA), Perspex, Acrylite, and Lucite. These transparent plastics are thermoplastics that act as a dependable alternative to glass.
The polymerization of acrylic acid derivatives eventually produces acrylic. Manufacturers can mold the resultant plastic into sheets, tubes, rods, or complex shapes. An acrylic sheet is a solid sheet formed by –
- Casting – It involves pouring liquid acrylic into molds (cast acrylic) or
- Extruding – It forces the melted acrylic through rollers (extruded acrylic).
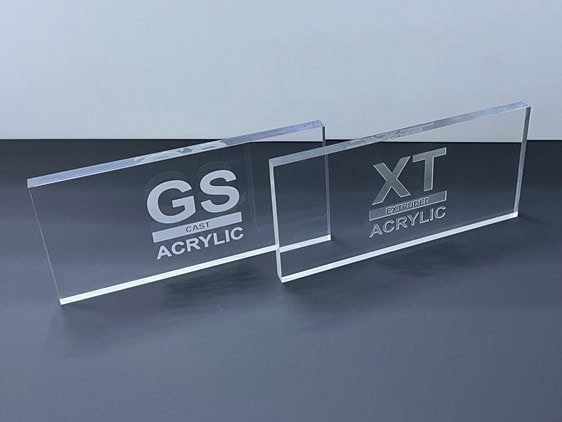
Plexiglass sheets come in distinctive sizes, thicknesses, colors, and finishes. Standard thicknesses range from 1mm to 25mm+ based on rods/sheets’ requirements. In addition, there are different finishes, such as clear, frosted, mirrored, tinted, fluorescent, etc.
Exclusive Features and Properties of Acrylic Sheets
- Optical Clarity: It transmits up to 92% of visible light. The clarity is better than glass materials.
- UV Resistance: Plexiglass sheets are considerably UV-resistant, making them ideal for outdoor applications.
- Weather and Chemical Resistance: It can withstand sunlight, rain, and standard chemicals.
- Impact Resistance: Standard plexiglass sheets exhibit 10x more resistance to impact than comparable materials.
- Lightweight: Mounting and transporting mass quantities is easy with half the weight of glass.
- Scratch Repairable: Polishing or treating with a flame can restore the standard optical clarity.
- Color/Finish Variety: It’s available in colored, frosted, tinted, mirrored, matte, and glossy finishes.
- Thermoformable: It’s possible to heat and reshape acrylic sheets without losing their strength.
- Non-Toxic (Food Safe): Certain acrylic plastics are FDA-approved for food or medical contact.
- Printable and Paintable: Acrylic sheets are compatible with UV/screen printing and paints.
Acrylic Sheets vs Other Forms of Acrylic
Feature | Acrylic Sheet | Acrylic Rods (Tubes) | Acrylic Film | Acrylic Resin |
Availability | Many different thicknesses, finishes, and colors | Fewer sizes or shapes of rods are available | Available in thin thickness with few decorative options | Being raw material, it’s not directly usable |
Fabrication Flexibility | Easy to cut, shape, glue, and print | Moderate flexibility (needs CNC or heat forming) | Significantly limited shaping | Molding and curing requirements |
Commercial Popularity | Highest industrial and commercial demands | Niche applications (mechanical or decorative parts) | Limited (mostly for packaging or lamination) | Employed in manufacturing only |
Ease of Use | Usable with basic mechanical tools | Mostly require specialized tools | Difficult to handle due to fragility | Heavy industrial tools are required |
Applications | Signage, displays, panels, dividers, windows | Decorative rods, light guides, handrails | Labels, overlays, flexible signs | Casting products, coatings, molding |
Cost Efficiency | Cost-efficient for large applications | Costlier due to specialized shapes | Cheaper for less reliable quality | Economical for bulk production |
Why Are Acrylic Sheets So Popular?
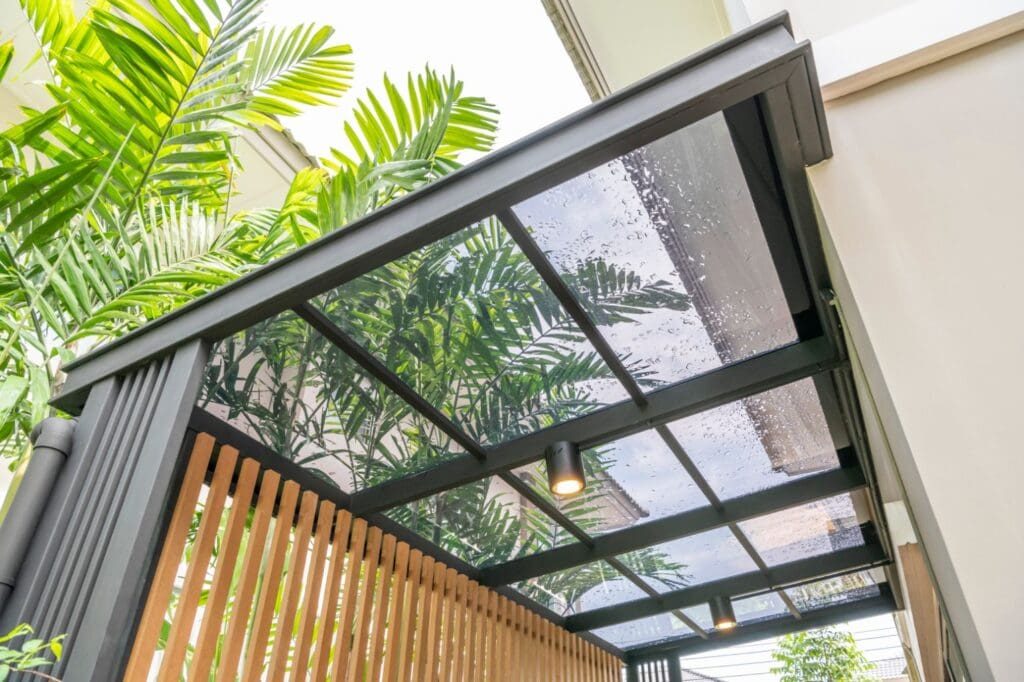
From business owners to DIY enthusiasts, there are viable reasons to prefer acrylic sheets –
- Versatility: Acrylic sheets are easy to cut, shape, and drill. It can undergo laser cutting (engraving), heat bending, and polishing for custom one-off projects.
- Broad Application Scope: Acrylic sheets cover more application scenarios than rods, tubes, or pellets. You’ll find them in signage, furniture, medical devices, and aquariums.
- Structural Stability: Unlike films or molded ones, plexiglass sheets provide good rigidity and load-bearing capability. Its uniform surface can accommodate mounting, printing, and fabrication.
- Availability: Acrylic sheets are globally available in standard and custom sizes. Mass production makes overall sourcing, shipping, and replacing simpler.
Meanwhile, acrylic sheets are in favour of commercial and industrial purposes because they –
- Support bulk customization (UV printing, CNC routing, or laser cutting).
- Compatible with automation for precision cutting and thermoforming.
- Act as substrates in advertising, fabrication, construction, and electronics.
- Reduce expenses due to easy transportation and superfast installation.
- It can be layered, laminated, and/or combined with lighting (for signage).
What Are Custom Acrylic Solutions?
Custom acrylic solutions indicate exclusive design, fabrication, and finishing of acrylic sheets. Customers specify projects, tasks, or requirements from which the specifications get determined. Such plastics go beyond standards through unique shapes, sizes, textures, finishes, colors, and/or functionalities.
Advantages of Custom Acrylic Solutions
- Tailor-made to fit design specs perfectly.
- Cost-efficient in the long run (less waste, few modifications).
- Integrates rather well with other materials.
- Meets brand aesthetics and functional requirements.
- Reduces lead time for installation or assembly.
- Improves end-product quality and customer satisfaction.
Some Downsides to Consider
- Higher initial cost than buying standard sheets.
- Longer lead time for complex or bulk designs.
- Requires accurate specifications to avoid errors.
- Not all customizations are always compatible.

Core Elements of Custom Solutions
A. Sizes and Shapes
It means cutting acrylic sheets to custom dimensions or shapes. You’ll get an exact fit for architectural designs with less installation time and minimal material waste. There are laser cutting (for precision), CNC routing (for thickness), and waterjet cutting (for thick acrylic plastics).
B. Thickness Variations
Customers can order sheets of specific thicknesses (from ultra-thin 1mm up to super thick 50mm+). Structural optimization comes with improved safety and aesthetic proportioning. They get adequately tailored to the specified usage conditions. And the applications are –
- Thin sheets (1–3 mm) for overlay, lenses, or printing substrates.
- Thick sheets (10–50 mm) for aquariums, load-bearing structures.
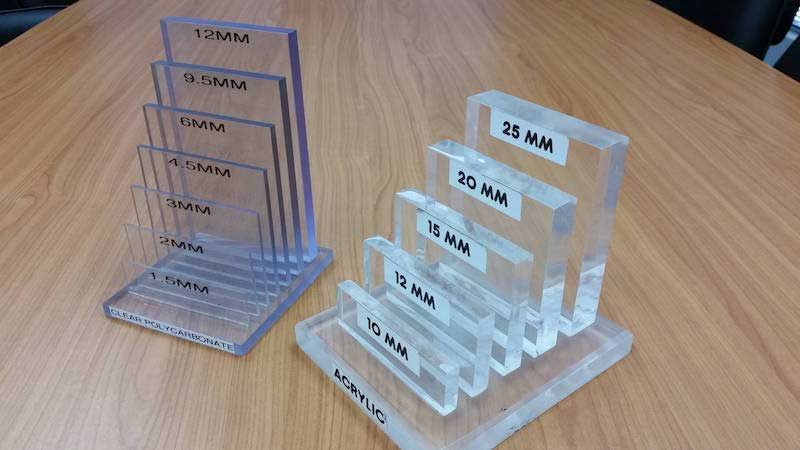
C. Colors and Finishes
Customers can choose from a range of color options. They can even request blends of different surface textures. It enables brand consistency, unique visual appeal, and diffusion control. Available finishes would be –
- Clear
- Matte/frosted
- Glossy
- Metallic
- Fluorescent
- Mirror
- Textured
D. Printing and Engraving
Acrylic sheets may feature UV-printed, screen-printed, or laser-engraving with graphics, texts, or logos. It initiates high-quality branding without requiring stick-on labels.
E. Forming and Bending
As mentioned, manufacturers heat and thermoform acrylic sheets into curved, domed, or angular shapes. You’ll get unique 3D structures in a seamless one-piece fabrication. Those plastics feature superior strength and molded curvature. The most preferable methods are –
- Line bending
- Oven forming
- Vacuum forming
F. Fabrication Service
It combines different operations to deliver finished acrylic parts, not just raw sheets. Turnkey solutions often save time in assembly while reducing multi-vendor coordination. The Commercial fabrication process may include –
- Cutting and shaping
- Gluing or solvent bonding
- Drilling and threading
- Assembly with other materials
G. Functional Add-Ons
It refers to the customization of acrylic sheets for specific functionalities, including coating and layering. Enhanced performance enables increased durability and user safety. They also come with regulatory compliance (fire rating). Common add-ons are –
- Anti-glare or anti-fingerprint coating
- UV-blocking or IR-reflective layers
- Impact modification (for extra strength)
- Anti-static coating (for electronics)
Factors to Decide on Acrylic Sheet
Choosing the perfect acrylic sheet is obligatory for optimal results, aesthetics, durability, and ROI. It doesn’t matter whether you’re working on a commercial product, architectural structure, retail display, or DIY craft. You must understand the key factors that influence the ultimate choice.
01. Application Purpose
Your project’s intended use directly affects the type of acrylic plastics you should choose. Ask yourself –
- Is it for indoor or outdoor use?
- Will it face impact, heat, or moisture?
- Is clarity or strength more important?
- Will it be decorative or structural?
Due to high transparency and impact resistance, you’ll need cast acrylic sheets for aquariums. On the other hand, extruded sheets are sufficiently cost-effective for protective barriers in retail.
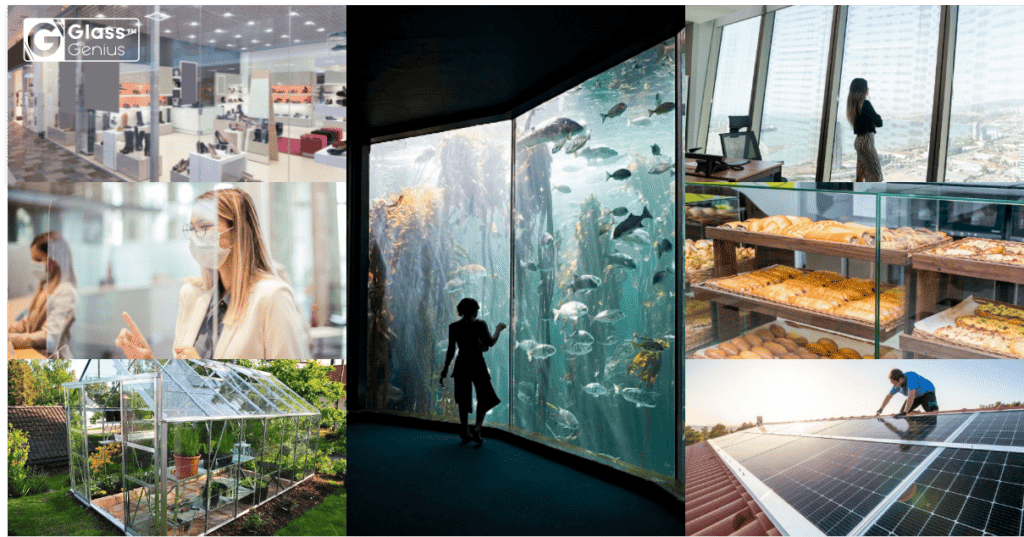
02. Thickness Requirements
The thickness of the acrylic sheet influences crucial properties like strength, durability, weight, flexibility or rigidity, and cost. Typical thicknesses for acrylic sheets include –
- 1–3 mm: Labels, overlays, craft projects
- 4–6 mm: Signboards, glazing, furniture panels
- 10–25 mm: Aquariums, safety barriers, structural panels
- 25+ mm: Load-bearing applications, security glazing
For instance, a 5 mm sheet is ideal for indoor signboards. A 20 mm thick cast sheet is more suitable for a large fish tank wall.
03. Optical Clarity and Finish
The clarity and surface finish affect visual appeal along with functionality. You’ll get to choose from different options like –
- Clear (glass-like): Best for windows, displays, and aquariums.
- Frosted or Matte: Reduces glare, ideal for lighting or privacy.
- Colored or Tinted: For decorative panels and branding.
- Mirrored: For interior decor and child-safe mirror alternatives.
For example, employ a colored and light-diffusing acrylic sheet for LED-lit signage. Consider frosted acrylic plastics to maintain light while offering privacy for office partitions.
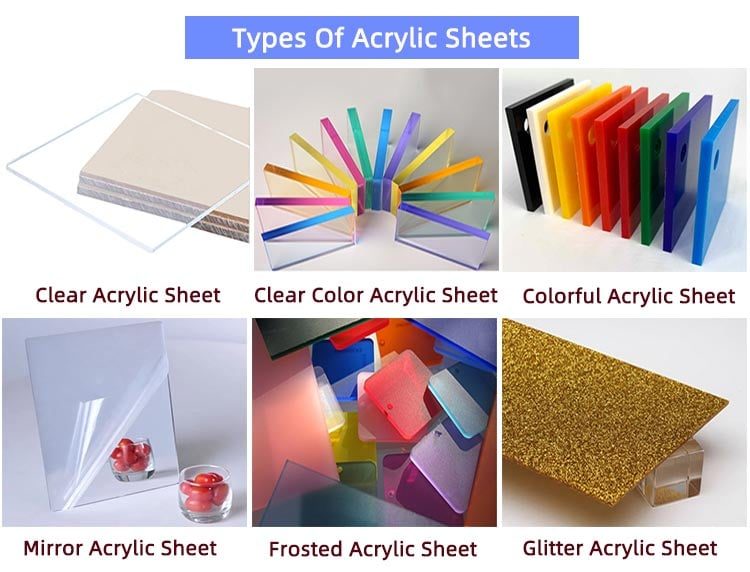
04. Fabrication Needs
Based on the project requirements, you may have to cut, engrave, shape, bond, or print on the sheet. Top fabrication factors include –
- Laser cutting works best with cast acrylic (cleaner edges).
- Thermoforming is easier with an extruded acrylic sheet.
- Glue bonding with surface prep is used to coat an acrylic sheet.
- Printing works well on flat, precise, or matte surfaces.
A laser-cut acrylic award should be made from a cast acrylic sheet for polished edges. Meantime, a curved product display stand in a shop should incorporate extruded acrylic for easier bending.
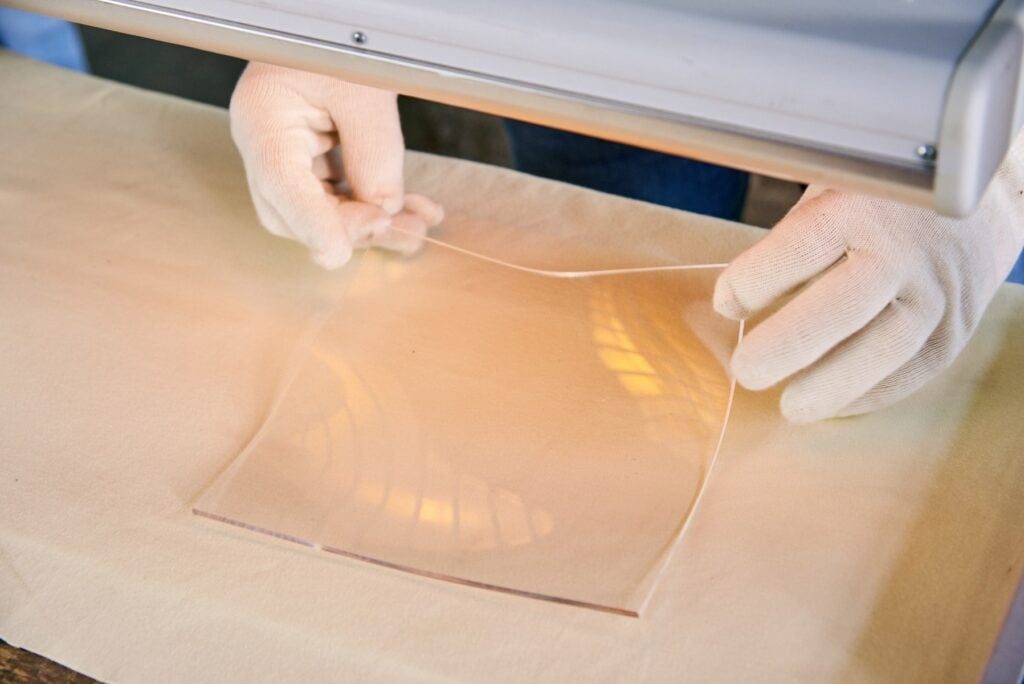
05. Environmental Conditions
Exposure to sunlight, heat, humidity, or chemicals can impact the sheet’s performance over time. You must proceed based on the following considerations –
- UV-resistant acrylic plastics for prolonged UV exposure.
- Heat-resistant or impact-modified acrylic for high-temperature zones.
- Weatherproof, tinted, or cast acrylic for outdoor uses.
- A sheet with superior chemical resistance for corrosive environments.
For example, employ a UV-stabilized colored acrylic sheet to resist yellowing for outdoor menu boards. Consider anti-static or chemically resistant acrylic for laboratory covers.
06. Impact Resistance and Safety
Applications in public spaces, schools, or high-traffic areas demand optimized durability. Available plastics or materials include –
- Standard Acrylic: 10x stronger and more resistant than conventional glass.
- Impact-Modified Acrylic: Up to 17x stronger than an average acrylic sheet.
- Polycarbonate (Alternative): Up to 250x stronger but considerably expensive.
For instance, you’ll need an impact-modified acrylic sheet for sports facility barriers. Thicker sheets work better in public or children’s spaces to prevent breakage.
07. Budget Constraints
The cost of acrylic sheets varies based on – type (cast vs extruded), thickness, size (shape or dimension), finishes, coatings, and further customization. A reasonable cost hierarchy (approximate) would be –
- Extruded clear sheet = Most affordable
- Cast acrylic = Moderate cost
- Colored/mirrored/impact-resistant = Higher cost
- Specialty sheets (UV-blocking) = Premium
For example, clear extruded acrylic plastics seem like a good choice for a low-cost retail barrier. You should go for cast or frosted acrylic for a premium jewelry display.
08. Sheet Size Availability
Acrylic sheets come in standard sizes (4’×8′, 5’×10′). However, custom sizes can minimize waste and reduce cutting needs.
For instance, you can order a pre-sized panel for a vending machine to reduce fabrication time. Get a jumbo-size cast acrylic to avoid joints for a wall-sized lightbox.
09. Customization Requirements
Some projects demand more than just cutting. In addition, they need custom printing, lamination, bending, or coating. Standard customization requirements include –
- Logo engraving or UV printing
- Curved panels
- Edge-polishing or beveled corners
- Anti-glare, mirrored, or anti-fog coatings
For example, employ custom-cut, colored, and polished acrylic material for a backlit company logo. Go for pre-drilled and bent acrylic panels for a restaurant sneeze guard.
Custom Solutions and Fabrication at JUMEI
Jumei Acrylics specializes in custom acrylic sheet solutions. All plastics are perfectly tailored to unique project demands. We create the best material for industrial components. You’ll have –
- Custom Sizes and Shapes – Precision-cut to fit your exact material specifications.
- Variety of Colors and Textures – From clear to frosted and mirrored to fluorescent.
- Tailored Thickness Options – Wide range of sheet thicknesses to suit your application.
Purchasing and Shipping Information
At Jumei, we strive to make your purchasing experience seamless and efficient through –
- Competitive Pricing – Great value on every material, with discounted rates for large orders.
- Standard Sheet Sizes Available – Including the most popular sizes like 48″ x 96″ (4 ft x 8 ft).
- Reliable Shipping – Worldwide delivery with quick turnaround times to meet your deadlines.
Why Choose JUMEI Acrylics for Plexiglass Sheets?
We’ve been a leading supplier of premium acrylic materials for years. That’s why we’re committed to offering top-tier material through exceptional service. As one of the valuable customers, you’ll have –
- High-Quality Acrylic Sheets – Durable, versatile, and available in many finishes and formats.
- Comprehensive Product Range – Including acrylic rods, tubes, blocks, and specialty materials.
- Customer-First Approach – Support team is always ready to help with every material aspect.
It doesn’t matter whether you’re for DIY enthusiasts, commercial fabricators, or industrial customers. Jumei Acrylics is ready to become your trusted partner for all kinds of acrylic ventures.
Frequently Asked Questions (FAQs)
01. What is the difference between polycarbonate and plexiglass sheets?
Acrylic and polycarbonate are plastics used as glass alternatives. Polycarbonate is comparable to an acrylic sheet in many ways –
Feature | Acrylic | Polycarbonate |
Optical Clarity | High (about 92% transmission) | Less (88% – 90% transmission) |
Impact Resistance | 10x than glass | 250x (literally unbreakable) |
Scratch Resistance | An acrylic sheet exerts high resistance | Low (easily gets scratched) |
Weather Resistance | A standard acrylic sheet holds excellent resistance | UV Coating is required for polycarbonate |
Ease of Fabrication | Easy to cut, polish, and bond | Difficulty in clean cuts and gluing |
Cost | An acrylic sheet is mostly affordable | Polycarbonate is somewhat expensive |
02. How do I glue acrylic sheets together?
Joining acrylic sheets takes specific adhesives and a careful process. Common gluing methods are –
- Solvent Cement: The adhesives melt the edges slightly to fuse them. The method is the best for invisible yet seamless joints.
- Capillary Action Technique: Keep the rods in contact together to apply the solvent along the seam. The liquid gets drawn into the joint to create a fused surface.
- Thicker Adhesives (Epoxy): It’s used for gap-filling or more forgiving applications. But the epoxy leaves a more visible joint line.
03. What are the advantages of using acrylic sheets for glazing applications?
Acrylic sheets have become popular for glazing (windows, skylights, enclosures, and protective barriers). It offers the following key advantages –
- Lightweight: Up to 50% lighter than glass. Easy installation and reduced structural load.
- High Impact Resistance: 10x – 17x stronger than glass. Reduced risk of potential breakage.
- Optical Clarity: Up to 92% light transmission, significantly higher than standard glass.
- Weather Resistance: UV-stabilization prevents yellowing, degrading, or cracking under sunlight.
- Safety: Shatters into large yet dull pieces (not sharp shards), making it safer in public spaces.
- Insulation: Provides superior thermal insulation than glass in some applications.
- Design Flexibility: Easily cut, shaped, or curved for custom window panels, domes, or partitions.
04. Can I purchase translucent acrylic sheets?
Yes. You better contact Jumei Acrylics for translucent acrylic sheets. Translucent plastics are available in different colors, finishes, and thicknesses. Translucent ones allow light to pass through. However, translucent blurs or diffuses visibility, similar to frosted glass. Available options include –
- Frosted (matte surface) translucent.
- Tinted translucent (gray, bronze, or colored).
- Fluorescent edge-lit translucent acrylic.
- Light-diffusing acrylic (LED panels and backlit signs).
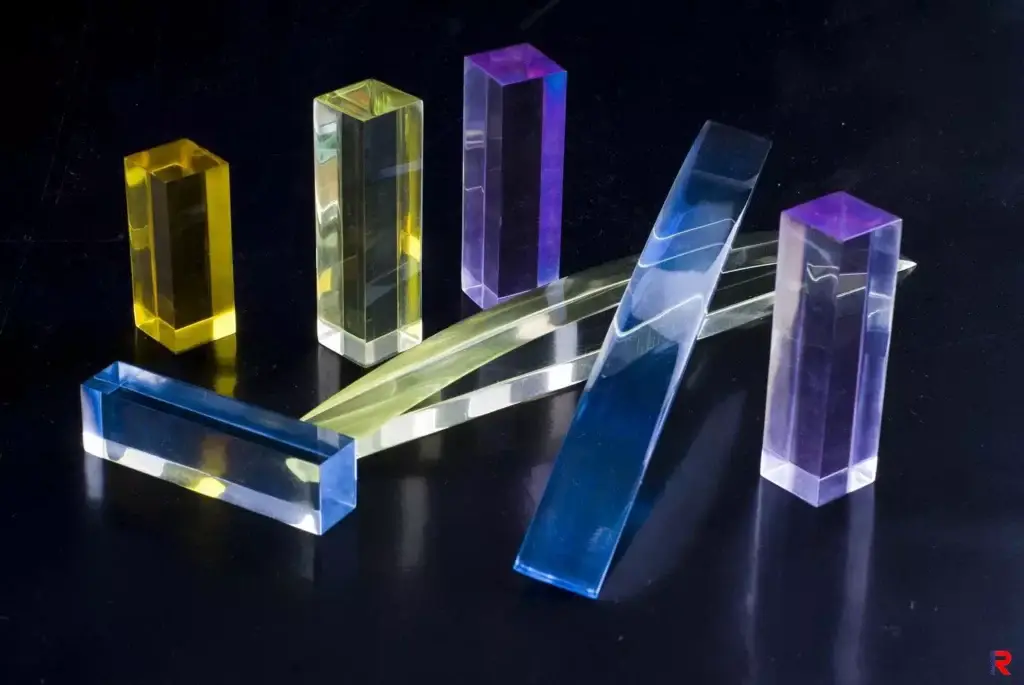
05. Do you offer custom cutting and fabrication services for acrylic sheets?
Absolutely. Customization is one of the prime specialties at Jumei Acrylics. Our fabrication services Include:
- Custom Cutting – Laser and CNC cutting for precision.
- Drilling – For pre-mounted holes, slots, or fasteners.
- Polishing – Edge finishing for a glossy, clean, and nice look.
- Thermoforming – Heat-shaped acrylic for display stands, covers, and guards.
- Printing and Engraving – Branding, signage, or decorative designs.
Conclusion
Acrylic features an ideal balance of versatility, durability, and flexibility. That’s why it’s a go-to material for creative and functional applications. A wide range of colors, textures, thicknesses, and custom fabrication options are available for acrylic sheets. Therefore, bringing your vision to life with Jumei Acrylic is easier than ever. Whether you’re set for a business, public space, or personal project, our experts are ready to prove their worth as the ultimate supplier. Contact us right away to discuss your demands, learn about custom solutions, and get expert guidance.