Acrylic and plexiglass are interchangeably used across industries. Similarities in appearance and shared properties due to the same chemical structure are likely to cause the misconception. As you should know, the two are different identities.
The article demystifies the mis-concept interchange between ‘plexiglass’ and ‘acrylic.’ We’ll shed light on their features, properties, and application differences. You’ll know which material is the most suitable for your project.
What Is Acrylic?
Acrylic primarily refers to a group of synthetic polymers derived from acrylate monomers. The most common form of acrylic is polymethyl methacrylate (PMMA). It’s a transparent thermoplastic often used as an alternative to typical glass plates.
PMMA was first developed in the early 20th century with a balance of durability, weather resistance, and lightweight properties. Acrylic sheets, rods, and other fabricated forms are ubiquitous in automobile, furniture, and display industries.
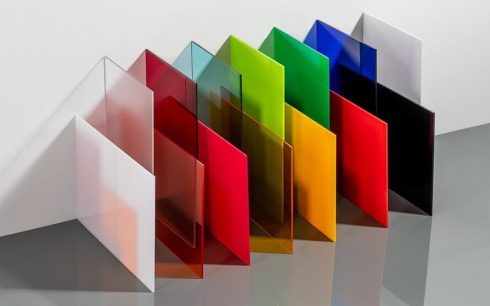
Properties of Acrylic
- Clarity and Light Transmission: Acrylic can achieve near-perfect optical clarity. It’s ideal for transparent uses like windows or shields.
- Eco-Friendly Advantages: Recyclable acrylic contributes to responsible environmental actions upon proper management.
- Strength: Despite being lightweight, acrylic is shatter-resistant. The significantly stronger plastic ensures durability in most uses.
- Weather Resistance: Acrylic can resist UV radiation and moisture. It maintains aesthetics and integrity in outdoor applications.
- Supreme Versatility: Incredibly flexible acrylic facilitates simplified transportation, installation, molding, fabrication, and thermoforming.
- Customizable Appeal: Sheets are available in many colors and finishes. You can get frosted, mirror, tinted, and clear acrylic.
- Easy Maintenance: Acrylic surfaces are easy to clean. The plastic can resist common chemicals to retain optimal longevity.
- Excellent Compatibility: Seamlessly combined acrylic with other materials (metal or wood) creates sophisticated designs.
Common Acrylic Applications
- Signage and Advertising: Illuminated signs and displays rely extensively on acrylic for clarity, durability, and customizability.
- Medical Devices: Its non-reactive nature and sterilization make acrylic suitable for incubators, surgical trays, and dental prosthetics.
- Eyewear: A lightweight and impact-resistant acrylic sheet is a great lens option. It provides optical clarity along with long-lasting uses.
- Household Products: From furniture and lighting to aquariums, acrylic can enhance products with stylish appearance and practical benefits.
- Automotive and Aeronautics: Acrylic windows, light covers, and interior components are preferred due to the high strength-to-weight ratio.
- Construction: Roofing, partitions, and decorative panels in modern architecture increasingly choose acrylic for aesthetics and functionality.
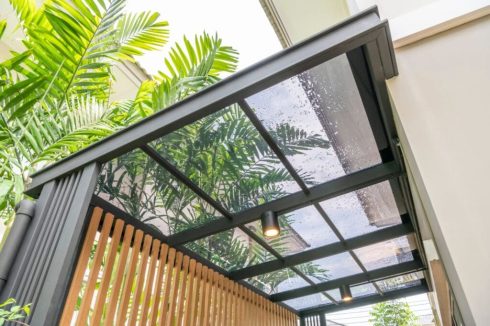
Acrylic PMMA is a plastic material with a perfect blend of practicality, adaptability, and creativity. Its unique properties drive innovation across countless industries for modern design and functionality.
What Is Plexiglass?
Plexiglass is a trademark or brand name for a specific acrylic type of polymethyl methacrylate (PMMA). Thermoplastic PMMA, deriving from methyl methacrylate (MMA) monomers, is known for its outstanding physical properties.
History of Plexiglass: German chemist Otto Röhm first polymerized methyl methacrylate in 1928. The Röhm Haas ag patented plexiglass for commercialization in 1933. The origins of the word ‘plexiglass’ refer to the initial brand name ‘Plexiglas.’
Over time, ‘plexiglass’ has evolved into a generic term used interchangeably with acrylic sheets. It also contributes to a degree of confusion about their differences. Remember – all plexiglass is acrylic, but not all acrylic is plexiglass.
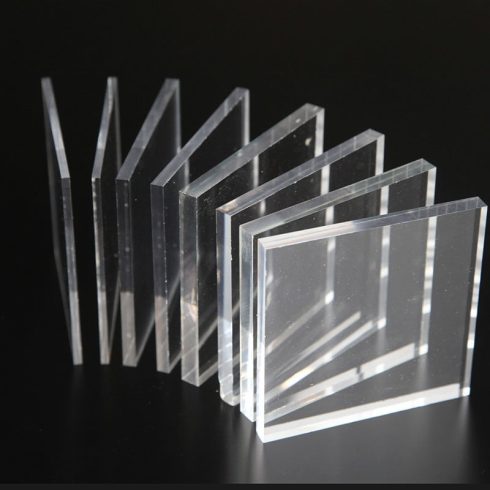
Characteristics of Plexiglass
- Clarity: Plexiglass offers exceptional optical clarity with a maximum of 92% light transmission rate. It makes the material as clear as glass.
- Lightweight: It’s significantly lighter than glass. Plexiglass facilitates easy handling, transportation, and installation without losing strength.
- Shatter-Resistance: Plexiglass sheet is highly resistant to impact and shattering. It’s a safe choice for uses that require enhanced durability.
- Customizable Forms: Plexiglass is primarily available in sheets. It can be easily shaped, molded, and cut into custom forms to meet functional needs.
- Weather and UV Resistance: Plexiglass retains clarity and structural integrity when exposed to outdoor conditions (sunlight and weather).
- Environmentally Friendly: It’s possible to recycle plexiglass. Such acts contribute to sustainable material usage when disposed of responsibly.
- Simple Maintenance: Modern plexiglass requires minimal effort to clean. It resists scratches and damage when handled correctly/carefully.
- Cost-Effective Alternative: Plexiglass seems more affordable than glass regarding material costs and installation for most custom projects.
Common Plexiglass Applications
- Construction and Architecture: Skylights, partitions, and sound barriers increasingly choose plexiglass due to its strength, clarity, and lightweight nature.
- Signage and Displays: Plexiglass is quite popular for illuminated signs, store displays, and exhibition booths, with different customization options.
- Automotive and Transportation: Windshields’ side and rear windows benefit from lightweight and shatter-resistant properties for safety and performance.
- Retail and Commercial Displays: It’s ideal for durable and visually appealing retail shelves, display cases, and protective shields at checkout counters.
- Home and Decorative Uses: Clear plexiglass is now featured in furniture, picture frames, and aquariums, where its light weight and modern appearance are valued.
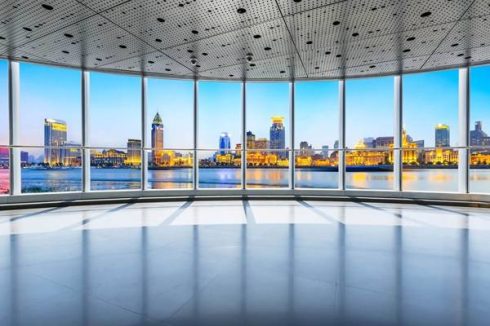
Plexiglass is a material that harnesses the combo of functionality, durability, aesthetics, and flexibility. Its enduring relevance across industries proves adaptability and practicality as a highly reliable material.
Key Difference Between Plexiglass and Acrylic
A. Brand Name vs. Umbrella Term
As mentioned, plexiglass is a brand name that refers to polymethyl methacrylate (PMMA). Over time, ‘plexiglass’ has been mistakenly considered as the same material as acrylic. And it creates confusion among consumers and even manufacturers.
In contrast, acrylic refers to a broader category of synthetic polymers. It’s more like an umbrella term that includes plexiglass alongside other variants, materials, or plastics. Acrylic is available in many forms, finishes, and qualities for distinctive applications.
B. Material Composition
Plexiglass, or ‘Plexiglas,’ is the trademarked brand name for a specific acrylic type. As a branded form of acrylic, plexiglass meets higher standards of quality and consistency. It’s favored for applications requiring reliability and precision.
Acrylic, on the other hand, is a generalized term for PMMA-based synthetic polymers. PMMA, the material used in plexiglass, is the most common type of acrylic. However, the term also encompasses other variations in diverse forms (sheets, rods, tubes).
C. Cost (Initial and Overall)
Plexiglass mostly marks higher price points than standard acrylic. The additional charge comes from its brand recognition and constant manufacturing quality. The trademark material holds stricter standards in production for reliable performance.
The pricing for acrylic significantly varies based on the specified variant. Standard acrylic sheets are usually more affordable to suit budget-conscious projects. The actual cost varies significantly based on thickness, finish, and customization.
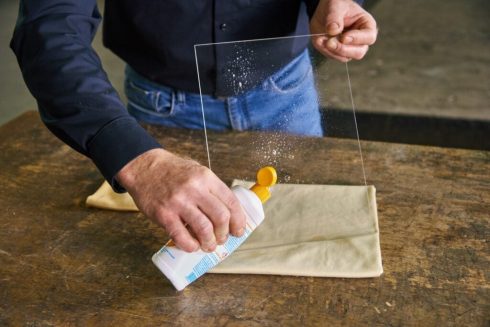
D. Material Durability
The trademark form of polymethyl methacrylate (PMMA) features superior durability. It’s more like a premium material for high-performance applications. Resistance to shatter and impact makes plexiglass a reliable choice regarding strength and safety.
Acrylic exhibits varying degrees of durability depending on the manufacturer, type, and application. PMMA is the most durable variant, but others (extruded or cell cast acrylic without treatment) may not deliver sufficient strength and weatherability.
E. Scratch Resistance
Plexiglass exhibits enhanced scratch resistance compared to most other acrylic products. The proprietary manufacturing process enables plexiglass engineering with minimal surface damage during usage. It’s suitable for applications involving frequent contact or luxury aesthetics.
Meanwhile, standard acrylic is notorious for picking minor scratches easily. Such vulnerability stems from manufacturing acrylic and plexiglass with varying quality standards. Extruded acrylic, for example, is more prone to scratches than acrylic from cell casting.
F. UV Resistance
Plexiglass is widely recognized for its superior UV resistance and ability to maintain structural integrity. The branded acrylic material often features UV-resistant additives or protective coatings. It prevents future discoloration, yellowing, and material degradation.
Acrylic shows varying UV resistance depending on the manufacturer and material composition. Standard sheets may lack the inherent UV protection found in plexiglass. They’re more prone to discoloration, yellowing, and material degradation under prolonged sun exposure.
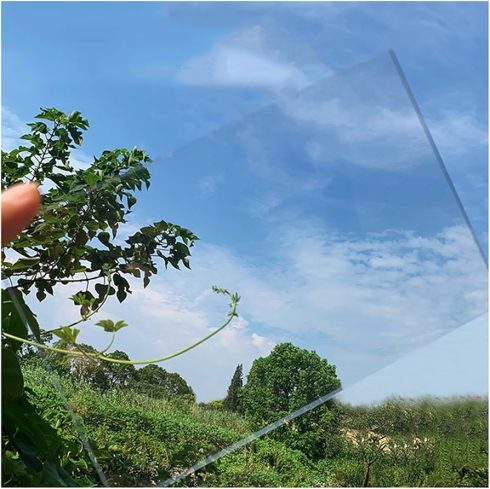
G. Available Surface Finish
Plexiglass is typically available in a limited range of surface finishes. Still, the finishes are carefully engineered to meet high-quality standards. You can cater to specific applications rather effectively. Standard finishes for plexiglass include –
- Glossy/Polished Finish: The polished finish is ideal for maximum transparency in display cases, protective shields, and advertising signage.
- Frosted Finish: An elegant light diffusion light with optimal durability suits privacy panels, decorative partitions, or architectural applications.
- Textured/Non-Glare Finish: Minimal glare and reflections make it to retail displays, museum cases, or environments with bright lighting.
In contrast, acrylic comes with an impressively wide array of surface finishes. It gives manufacturers more flexibility to match specific designs and functional needs. The available acrylic finishes include –
- High-Gloss Finish: The reflective surface is perfect for picture frames, furniture, and modern lighting.
- Frosted/Matte Finish: Its soft, translucent appeal scatters light evenly. Signage or interior décor can get some added elegance.
- Textured Finish: Includes options like pebble, sandblasted, or non-slip textures. It’s ideal for shower doors, illuminated signage, or anti-glare panels.
- Opaque Colors and Patterns: Lots of opaque colors, tints, gradients, and patterns allow creative design possibilities.
- Mirrored Finish: It mimics the reflective qualities of glass for use in creative and decorative projects.
H. Flexibility and Customization
Customizing options for plexiglass are somewhat limited. However, they’re always tailored precisely to meet performance-oriented needs. The material is available in standard thicknesses, sizes, and finishes. However, exotic/unique finishes, patterns, and colors are less common.
Typical acrylic, in contrast, offers extensive flexibility and customization options. That’s why it’s one popular choice for countless industries and design projects. Acrylic materials are available in numerous finishes, a wide spectrum of colors, and even unique patterns or textures.
I. Best Uses/Applications
Plexiglass is highly suitable for reliability, safety, and performance applications. Superior optical clarity, shatter resistance, and UV stability make it an excellent choice for demanding conditions. Some of the best applications involve –
i. Aerospace and Automotive Components
Plexiglass has thriving uses in airplane windows, cockpit canopies, and vehicle windshields. High impact resistance with lightweight properties enables safety and efficiency. Plexiglass can withstand extreme pressures and weather conditions.
ii. Medical and Dental Equipment (Protective Gear)
Plexiglass-made medical devices include incubators, surgical trays, and protective shields. Its consistent quality ensures absolute safety standards like resistance to sterilization and long-term clarity. Plexiglass use in protective shields reportedly increased by 300% during COVID.
iii. Outdoor Installations (Skylights, Greenhouses)
Excellent UV resistance and weatherproofing properties make plexiglass a preferred choice for long-term outdoor applications. For instance, plexiglass greenhouse panels allow up to 92% light transmission while blocking harmful UV rays.
Acrylic is a more affordable and adaptable material for creative flexibility applications. Its wide availability in various finishes, colors, and thicknesses seems ideal for consumer-focused projects.
i. Signage and Displays
Acrylic has become the go-to choice for illuminated signs, retail displays, and exhibition booths. Easy customization of the lightweight plastic allows intricate designs and creative expressions. A variety of finishes make it accessible and visually appealing.
ii. Interior Design and Furniture
Acrylic also makes furniture, decorative panels, lighting fixtures, and partitions. Molded, coloring, and finishing present almost endless design possibilities. Any budget-conscious decorative projects can benefit modern aesthetics while maintaining privacy.
iii. Arts and Crafts
Acrylic’s almost universal adaptability makes it a top material for DIY projects, picture frames, and art installations. The affordable and workable plastic also accommodates easy cutting or shaping. Hobbyists and artists can experiment creatively without higher costs.
iv. Aquariums and Tanks
An underrated yet growing applicable field concerns acrylic fish tanks (from small to large). Plexiglass may offer higher scratch resistance, but lightweight and affordable acrylic gets the upper hand. Acrylic aquariums are 17x more impact-resistant than glass tanks.
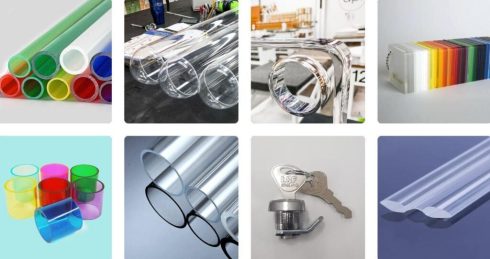
Comparison Table: Plexiglass vs Acrylic Sheets
Aspect | Plexiglass | Acrylic |
---|---|---|
Definition and Branding | A trademarked brand name for polymethyl methacrylate (PMMA) | A generic term encompassing all synthetic polymers derived from acrylate monomers, including PMMA |
Material Composition | Always composed of PMMA with strict quality standards | Indicates a broad range of polymers with varying properties and quality |
Long-Term Transparency | Quality control and assurance retains the clarity for years of application | Retention of clarity depends on treatment and assurance in acrylic production |
Material Weight | Lightweight for applications requiring high strength-to-weight ratio | Similarly lightweight but mostly chosen for easy installation and versatile applications |
Cost (Initial and Overall) | Higher upfront cost due to brand recognition and premium quality | Usually more affordable due to less upfront cost for standard specifications |
Long-Term Cost Efficiency | Highly cost-saving in the long run due to minimal maintenance needs | Untreated products require more frequent replacement to increase overall costs |
Material Durability | Superior impact resistance, shatter-proof, and UV-resistant | Variable durability depending on quality |
Scratch Resistance | Enhanced scratch resistance due to specialized manufacturing and coatings | More susceptible to scratches but can be treated or polished for improved performance |
UV Resistance and Weatherability | Exceptional UV resistance retains clarity and integrity under prolonged sun exposure. | UV resistance depends on treatment; untreated acrylic may degrade or yellow faster. |
Surface Finish Options | Limited to premium finishes for performance and aesthetics for demanding uses | A broad range of finishes, colors, and patterns to suit decorative applications |
Flexibility and Customization | Customization focused on performance and reliability, including thermoformability. | Highly adaptive with extensive customization in colors, patterns, textures, and shapes |
Manufacturing Standards | Strict proprietary processing for consistency, durability, and reliability | Produced by manufacturers with diverse quality standards and processes |
Weather Resistance | Excellent weatherproof properties remain durable in extreme conditions without yellowing or cracking. | Performance depends on UV or weather-resistant treatments. Untreated acrylic may degrade faster outdoors. |
Impact Resistance | Capable of withstanding high-impact force to resist immediate shattering | Capable of withstanding enough impact forces without immediate shattering |
Heat Resistance | Superior resistance to confront temperature fluctuations | Varying degrees of resistance to temperature fluctuations |
Chemical Resistance | High-end plexiglass products are less reactive to everyday agents and solvents. | Limited resistance, especially with |
Environmental Impact and Recyclability | Recyclable and sustainable when managed responsibly for long-term ecological benefits | Recyclable, but variations may affect recycling. Some acrylics are made from recycled scraps. |
Foremost Applications | Aerospace, automotive, medical, outdoor installations, and noise barriers | Signage, interior design, furniture, aquariums, arts and crafts, and decorative projects |
Which One to Choose from Acrylic and Plexiglass?
Choosing between acrylic and plexiglass depends entirely on the specific needs of your project. You must balance cost, durability, customization, and environmental conditions.
Both materials share too many similarities, like cleanups for plexiglass and acrylic maintenance. But they excel in particular features to suit different applications regarding a comparative benefit.
a. Durability and Performance
Get plexiglass when your project requires high durability. Superior manufacturing standards enable consistency in strength and resistance. Stick to acrylic for less demanding applications. Acrylic is still durable but may not handle prolonged outdoor exposure.
b. Cost Efficiency
Plexiglass justifies the need for long-term durability with its high initial cost. It needs less maintenance and minimal replacement. For budget-conscious projects, acrylic picks the win. Acrylic maintenance and sustainability seem affordable with lower upfront costs.
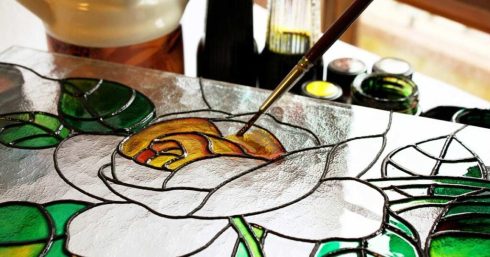
c. Customization and Flexibility
Projects involving performance-driven customization should use plexiglass. Its thermoformability allows precision and integrity. Acrylic offers greater flexibility with many finishes, colors, and patterns. It’s preferred for artistic, decorative, or visually driven projects.
d. Resistance to Rigors
For outdoor, sensitive, reactive, and stressing applications, plexiglass has the upper hand. It can resist yellowing and degradation way better than untreated acrylic. Treated acrylic can suffice the same uses while being a more affordable alternative with periodic replacements.
Conclusion
The difference between acrylic and plexiglass prevails in performance, cost, and applications against some foundational similarities. Higher manufacturing standards turn plexiglass more like a premium variant of standard acrylic PMMA. However, generic/typical acrylic provides unmatched flexibility and customization to suit almost any cost-sensitive project.
Get Your Necessary Acrylic or Plexiglass from JUMEI
Have you decided on a choice between plexiglass or acrylic? Or are you still unsure about the best option? Jumei Acrylic Manufacturing has excelled in acrylics for 15+ years with top experts, standards, and techniques. Contact us for professional consultation on your best possible choice.