Plexiglass has many applications as a durable, versatile, and reliable alternative to traditional glass. It has transformed many industries with excellent strength and superb adaptability. The plastic also possesses resilience, impact resistance, and transparency. That’s why the acrylic material can deliver remarkable advantages across diverse applications.
This article evaluates acrylic glass material in terms of strength and durability for common as well as demanding applications. You’ll get to know the unique properties, uses in real-world settings, and comparisons with glass and polycarbonate. Understanding acrylic characteristics and applications can help you with the practicality of plastics.
What is Acrylic Glass (Plexiglass)?
Plexiglass is an alternative/synonymous brand name for methyl methacrylate polymer (PMMA). It also goes by acrylic and Plexiglas. It’s a synthetic resin from the polymerization of methyl methacrylate (MMA) monomer.
Chemically, polymethyl methacrylate (PMMA) is an acrylic polymer. The thermoplastic comes with impressive strength, clarity, and adaptability. Manufacturers can mold and reshape the versatile material to meet unique specs.
Some Key Characteristics
- Clarity: Acrylic glass features exceptional optical clarity (nearly 92% light transmission). That’s what makes transparent plastic directly comparable to standard glass.
- Lightweight: Despite the durability, the versatile plastic material is significantly lighter than glass. The durable material seems more convenient to handle, transport, and install. It particularly suits large-scale commercial applications.
- Impact Resistance: One of the plexiglass’ most outstanding features is its resistance to impact. The value is around 17x stronger than glass. Thus, it enables safety and durability.
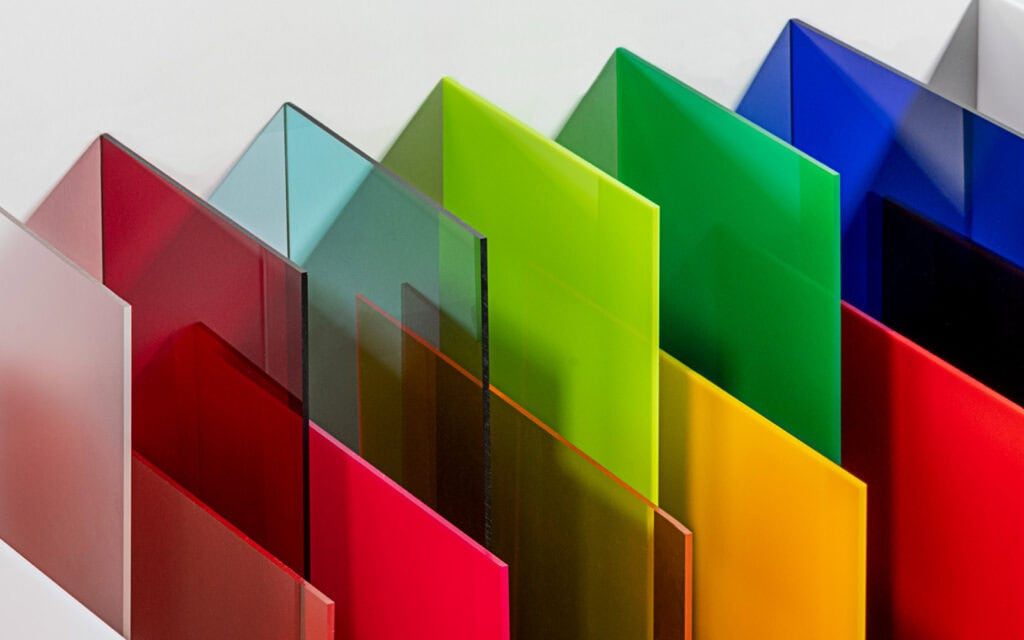
Differences Between Plexiglass and Its Alternatives
Acrylic sheets are more or less alternatives to other materials like traditional glass and polycarbonate (PC). It’s mandatory to know the fundamental differences between the three.
- Plexiglass vs Glass: Plexiglass features more shatter resistance. The lightweight material is easy to mold into intricate shapes. Glass offers higher scratch resistance compared to acrylic products. That’s why acrylic plastics may need protective coatings for certain applications.
- Plexiglass vs Polycarbonate: Polycarbonate is one of the other materials from thermoplastics. It shares many characteristics with acrylic glass (high resistance to impact). Polycarbonate is tougher than acrylic products with greater resistance to force at a higher cost and low clarity.
- Polycarbonate vs Glass: Lightweight polycarbonate is approximately 250x stronger than glass. The least scratch resistance may require coatings for durability. Glass is heavier with high scratch resistance and superior optical clarity for safety glass or decorative element(s).
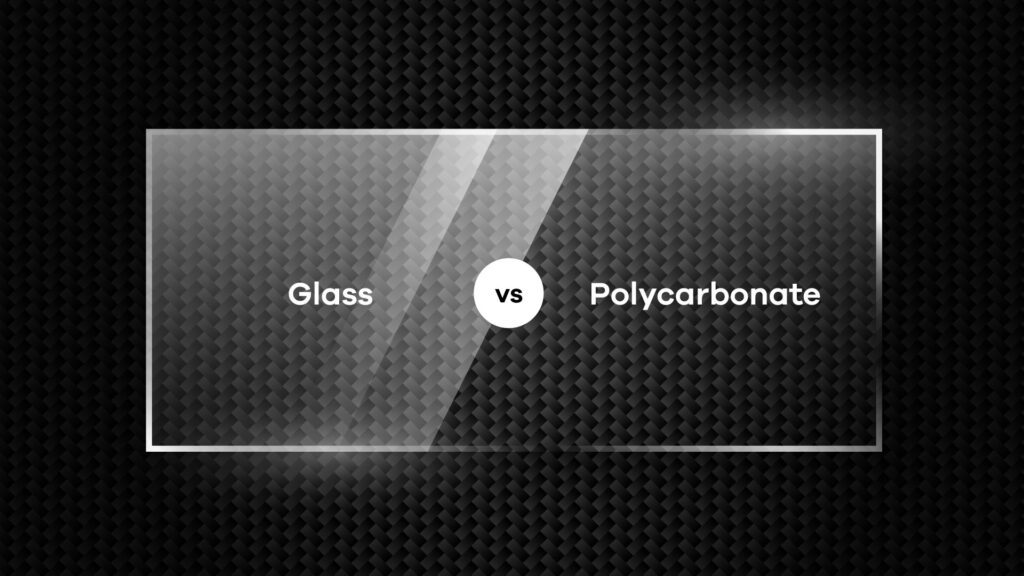
Plexiglass vs Traditional Glass vs Polycarbonate
However, the above discussion is unlikely to depict the basic differences between the three. You can easily grab the core ideas from the detailed comparison table mentioned below.
Property | Acrylic | Glass | Polycarbonate |
Chemical Composition | Methyl Methacrylate (MMA) Polymer or PMMA | Silicon Dioxide with various additives | Polycarbonate resin originating from BPA |
Optical Clarity | High (about 92% light transmission) | Extremely clear, higher than acrylic (92% – 96%) | Sufficient clarity (about 88% light transmission) |
Weight | Lightweight (50% lighter than glass) | Heaviest among the three | Very lightweight (similar to Plexiglass) |
Impact Resistance | Approximately 10x stronger than glass | Brittle, less shatter resistant on impact | Extremely impact-resistant (250x stronger than glass) |
Flexibility | Flexible and can be molded or shaped | Rigid and brittle, not flexible | Highly flexible, ideal for bending applications |
Scratch Resistance | Susceptible to scratching (can be polished) | Excellent scratch resistance | Prone to scratching (requires protective coatings) |
UV Resistance | Naturally resistant to UV radiation | Limited UV resistance (may require treatment) | UV resistant with additional coatings |
Chemical Resistance | Resists household chemicals; less resistant to industrial solvents | Almost inert or inactive; highly resistant to chemicals | Resistant to many chemicals but vulnerable to certain solvents |
Durability | Long lifespan (10 – 30 years) | Can last decades with maintenance | Exceptional durability often outlasts Plexiglass |
Cost | Moderate cost | Varies (typically expensive for high-quality glass) | Costlier than acrylic plastic but worth it for specific applications |
Applications | Protective barriers, windows, displays, signage | Architectural uses, airplane windows, decorative applications | Safety glass, shields, industrial parts, curved designs |
*Plexiglass is a trade name for methyl methacrylate polymer (acrylic materials). All plexiglass is acrylic but all acrylic sheets aren’t the same product (not commonly sold as plexiglass)*
Types of Strength in Plexiglass
As mentioned, acrylic glass exhibits incredible strength that makes it ideal for various applications. The strength is divided into four key types – tensile strength, impact resistance, flexural strength, and compressive strength. Each one contributes to the durability of acrylic sheets.
01. Tensile Strength
It measures the amount of pulling force a standard acrylic sheet can endure before breaking. Plexiglass showcases a tensile strength of approximately 65 MPa – 70 MPa (megapascals). The value denotes an exceptionally strong plastic material. Acrylic glass also has good flexibility, making it a shatter resistant alternative under heavy stress. It qualifies acrylic glass for applications requiring resistance to stretching or pulling forces (display cases and barriers).
02. Impact Resistance
It represents the plexiglass’ ability to withstand sudden shocks or forces without breaking. The clear acrylic is around 10x stronger than regular glass for additional safety and durability. It also makes the clear plastic sheet an excellent choice for heavy impact (sports arenas or protective shields) uses. Clear acrylic also remains a dependable material for uses requiring lightweight and transparent alternatives with the additional benefit of reduced fragility.
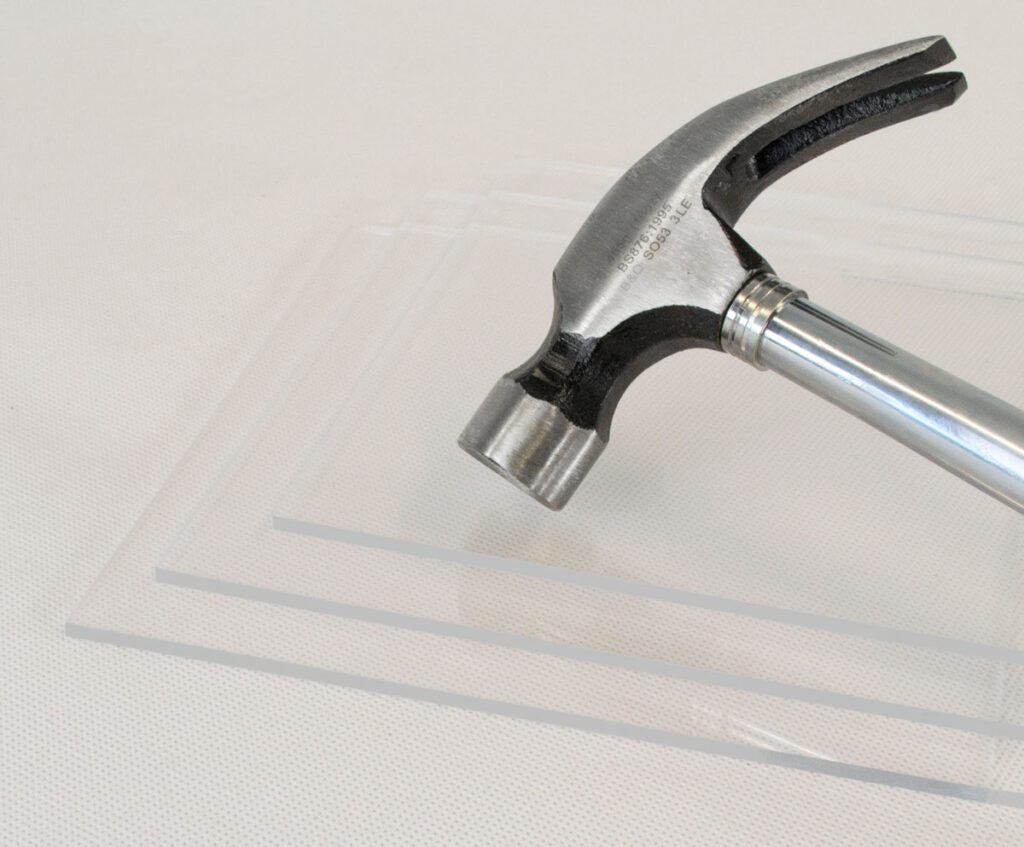
03. Flexural Strength
It refers to plexiglass’s ability to bend without breaking, a property for curved or loaded applications. Plexiglass products hold a flexural strength of 110 MPa (approximately). Thus, it maintains structural integrity under bending forces. The strength becomes especially significant in applications like signage, curved windows, and decorative panels. Plexiglass offers a combination of flexibility and durability, making it more adaptable to creative engineering demands.
04. Compressive Strength
It measures the material resistance to crushing and/or flattening force. Plexiglass exhibits excellent compressive strength to withstand loads and pressure without deformation or cracks. It’s a crucial property for applications where the material must endure weight and pressure. You can choose plexiglass as furniture components and structural reinforcements. Compared to regular glass, plexiglass has higher compressive strength as glass is more brittle.
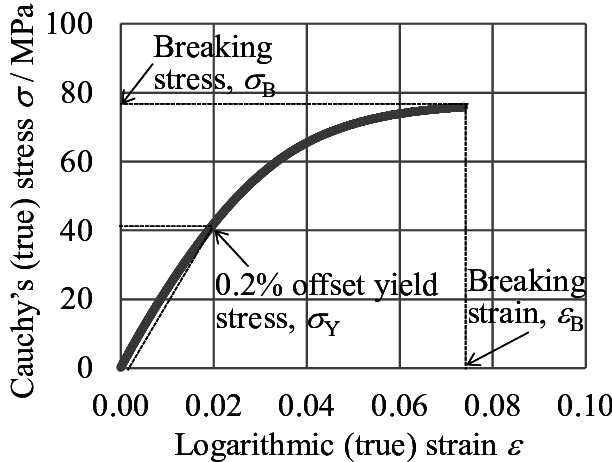
Durability Factors of Acrylic Sheets
Aside from strength, the acrylic plastic doesn’t fall short of durability. It features impressive longevity, making the plastic a preferred material for indoor and outdoor applications.
a. UV Resistance
The high resistance to UV radiation by default has been one of the plexiglass’ standout features. Standard glass may yellow or degrade over time. But the acrylic sheet is engineered to withstand prolonged exposure without significant degradation. It also retains the original clarity with aesthetic appeal even after years of outdoor use. Special coatings can further enhance the UV resistance, making acrylic products ideal for greenhouse panels, outdoor signage, and barriers.
b. Weather Resistance
Plexiglass excels in outdoor environments due to its ability to endure rain, wind, and temperature. Even immense temperature fluctuations can barely mess with the plastic (with a protective coating). It remains stable under varying climatic conditions to retain its strength and functionality. Whether you’re using acrylic products in freezing temperatures or under scorching heat, acrylic maintains structural integrity. That’s why it’s a reliable option for construction, automotive, and furniture.
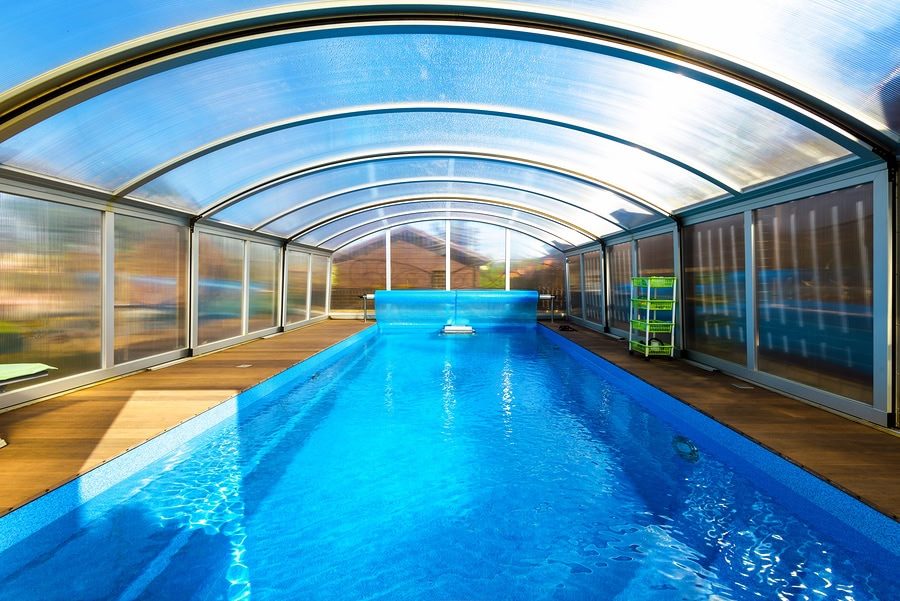
c. Scratch Resistance
Plexiglass is more prone to surface scratching than glass. It surely seems like a drawback but you can polish the plastics to restore the original, smooth, and clear finish. Manufacturers often employ protective coatings to enhance the standard scratch resistance in demanding applications. It’s quite important for tabletops, displays, and protective shields. Despite being less resistant to scratches, the ability to get repaired rather easily adds to the material’s versatility.
d. Chemical Resistance
The versatile plastic material shows satisfactory resistance to most household chemicals. It includes regular cleaning agents and related solvents for daily use. However, its chemical resilience is more like a standard or minimal. It’s because the compound can degrade or react under exposure to harsh or reactive industrial solvents eventually. This limitation becomes a crucial consideration in environments involving specialized chemicals like laboratories or industrial plants.
e. Lifespan
The longevity of Plexiglass primarily depends on its intended usage and overall exposure conditions. An acrylic item can last about 10 to 30 years under favorable conditions by maintaining its strength and transparency. However, you can expect the lifespan to get on a higher end upon indoor applications with minimal wear and tear. Meanwhile, outdoor uses put the material under stress, reducing its durability. But protective treatments can prolong its effectiveness.
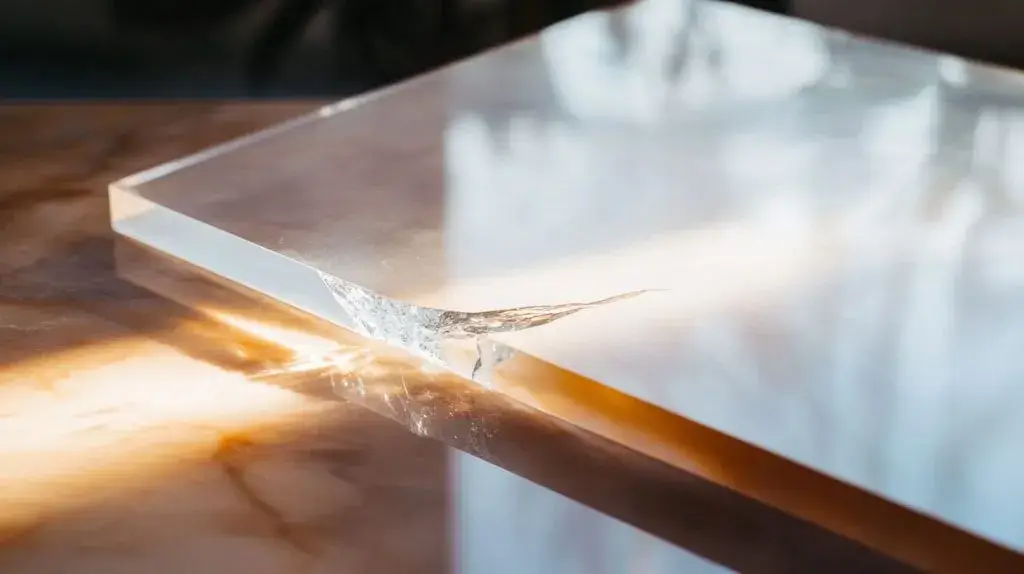
Common Applications to Indicate Plexiglass Strength
Plexiglass continues to serve as an indispensable material in numerous industries and settings. Let’s check out some common applications where each one illustrates durability and strength.
- Protective Barriers and Sneeze Guards: Plexiglass has become a well-favored choice as barriers and sneeze guards. Such products incorporate safety and visibility. The barriers provide a strong and impact-resistant shield to protect individuals. You can barely get in touch with physical interactions, airborne particles, or contaminants with poor visibility.
- Aquarium Panels: Thick acrylic in a sheet form is also common in aquarium panels. It’s the same for small-scale home setups and massive commercial aquariums. The high resistance to impact allows the plastics to support immense water pressure without cracking or breaking. Thus, it provides a secure enclosure for aquatic life and the surroundings with excellent clarity.
- Windows and Skylights: Plexiglass has widespread applications in aircraft windows and skylights. It’s quite the preferred choice for environments requiring enhanced impact resistance and optical clarity. Lightweight acrylic makes it easy to install. Whereas the ability to withstand impacts (hailstones or debris) ensures durability in harsh/adverse weather conditions.
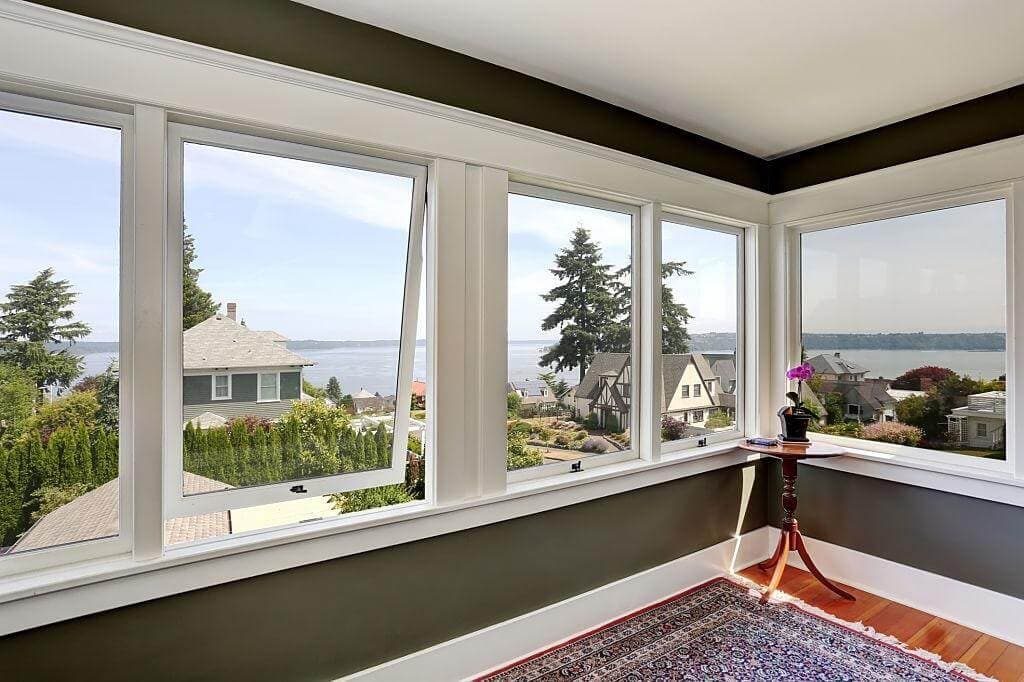
- Machine Guards in Industrial Settings: Some other manufacturers employ plexiglass for machine guards in industrial settings. It ensures the safety of workers while maintaining the visibility of operational equipment. The resistance to impact enables protection against flying debris or accidental impacts. Thus, it offers a reliable shield in potentially hazardous industrial settings.
- Signage and Displays: The longevity and lightweight nature make clear acrylic a sought after material for signs and displays. You can choose the plastic material for illuminated advertising signs, retail displays, and decorative panels. It features a great combo of durability with aesthetics. Its ability to maintain clarity without discoloration retains vibrancy and professionalism.
- Furniture and Interior Design: Plexiglass has increasing applications in furniture and interiors. The plastic introduces a modern and sleek alternative to traditional compounds. Designers employ acrylic products for items like tabletops, shelves, and decorative items. Strength and transparency create a unique visual appeal whereas its flexibility accommodates a custom design.
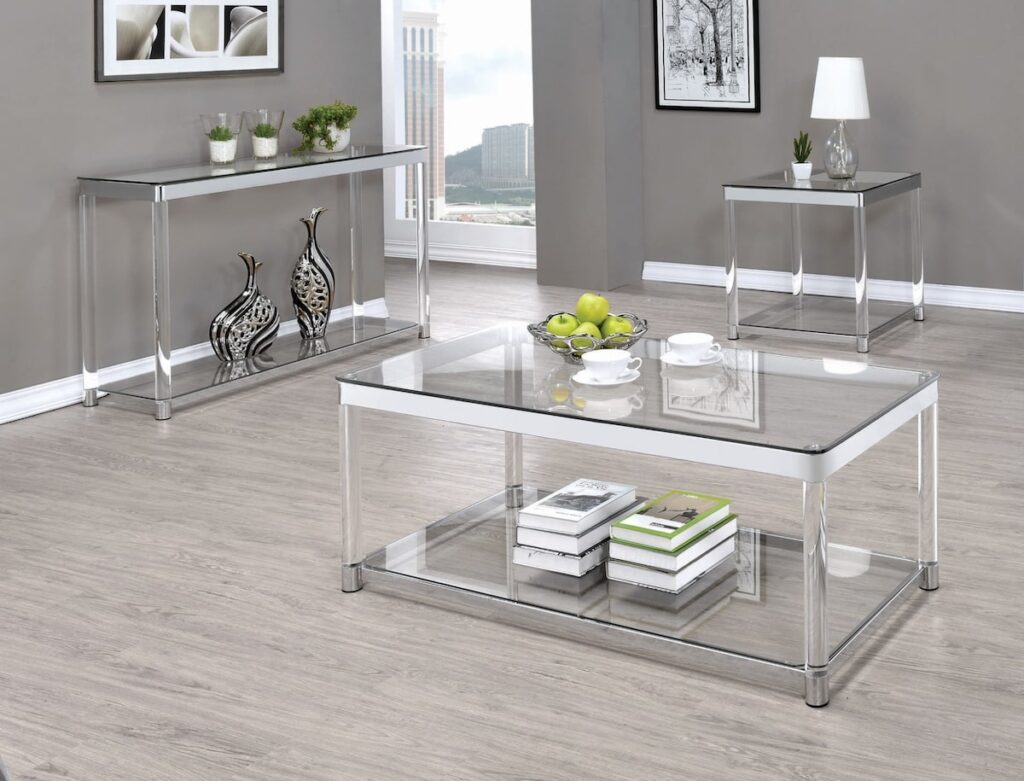
Factors to Affect Acrylic Plexiglass Sheet Strength
There are multiple critical, influencing, or driving factors for acrylic sheet strength and performance. You must understand those aspects to make the most of plexiglass during your intended applications.
i. Sheet Thickness
It’s one of the most crucial determinants of acrylic strength. Thicker sheets mostly possess greater strength. It allows the plastic to bear heavy loads and withstand high-impact forces. A thin plexiglass sheet seems adequate for light applications like picture frames or barriers.
In contrast, thicker sheets are crucial for demanding applications (aquarium panels and/or structural elements). Thicker materials can distribute force more evenly while reducing the risk of cracks or breaks. It makes acrylic an ideal material for load-carrying and high-impact applications.
ii. Mounting/Support Design
It may sound absurd but plexiglass installation and support can significantly impact its durability. Improper mounting leads to warping, cracks, and even vibrational damage. Uneven support for the plastic initiates uneven stress, causing the material to bend or deform over time.
Over-tightened screws or fittings can create stress points, often leading to fractures. In the meantime, insufficient or loose supports in high-vibration environments can weaken the plastics. That’s why plexiglass sheets should be properly mounted using flexible gaskets and spacers.
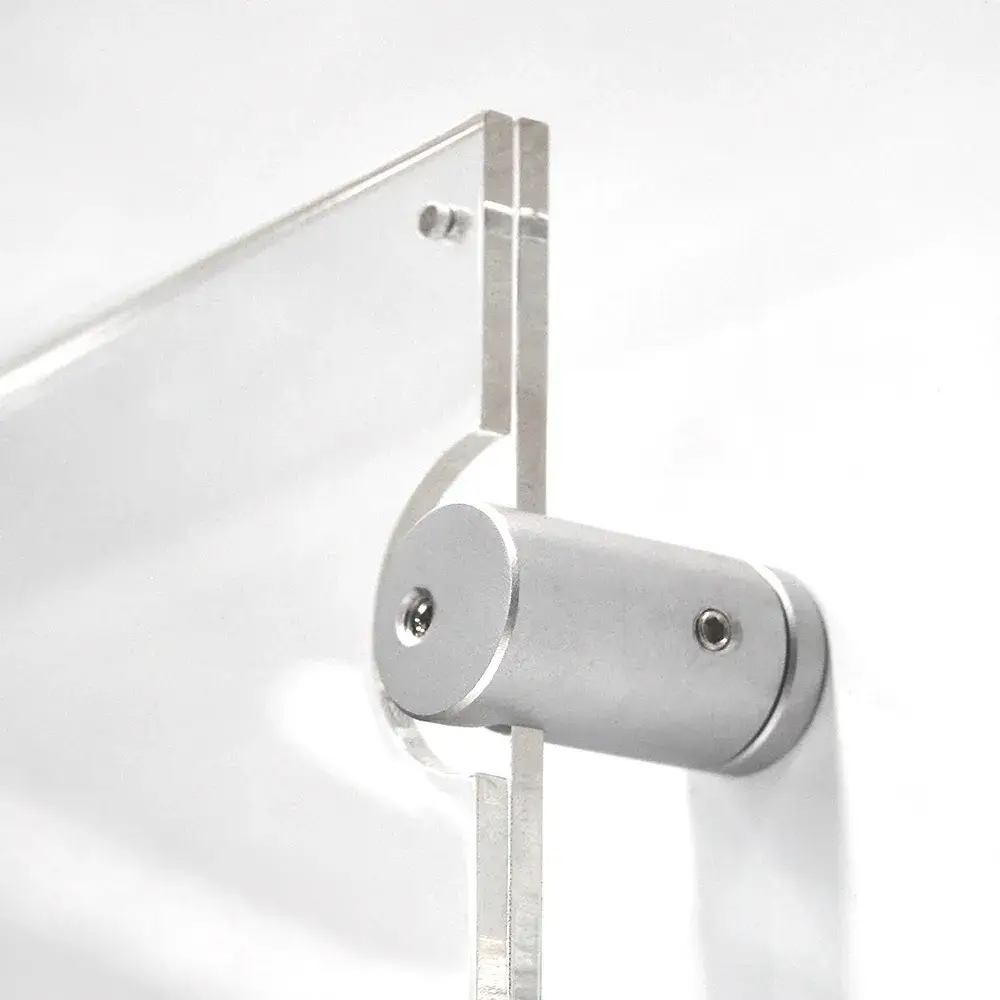
iii. Type of Acrylic (Cast vs Extruded)
The acrylic plastic type has a substantial influence on acrylic strength and performance. Cast acrylic sheets feature superior clarity and rigidity. The strong plastic seems less prone to bending or warping. It’s ideal for aquariums, display cases, or optical instruments.
Meanwhile, extruded acrylic sheets are slightly more flexible and easier to machine. But acrylic plastics are less rigid and may even lack the uniform strength of cast acrylic. However, the relatively low cost material works well for applications involving machining or shaping.
iv. Environmental Stress
Prolonged exposure to environmental factors (sun, rain, moisture, air) can gradually degrade Plexiglass strength. You should look out for high temperatures, UV light, and chemical exposures from the start. Acrylic glass, being less heat resistant, becomes soft, reducing integrity.
Additional protective measures are specified in industrial settings. Despite its natural ability, extended exposure without UV-resisting coating can lead to surface degradation or micro-cracks. Harsh solvents or prolonged exposure can cause crazing to compromise the strength.
Testing and Certification for Plexiglass
Many customers as well as some negligent manufacturers tend to overlook testing and certifications. It’s especially true for less-known and DIY projects. The acrylic sheet must meet industry standards for strength, durability, and safety.
Strength testing for Plexiglass is governed by internationally recognized standards. Obviously, the practice is led by ASTM (American Society for Testing and Materials) and ISO (International Organization for Standardization).
Such standards provide detailed and accurate guidelines. For example, ASTM D638 focuses on the material properties of plastics, including PMMA products. Meanwhile, ISO 7823 specifies testing methods for pure PMMA sheets (cast and extruded).
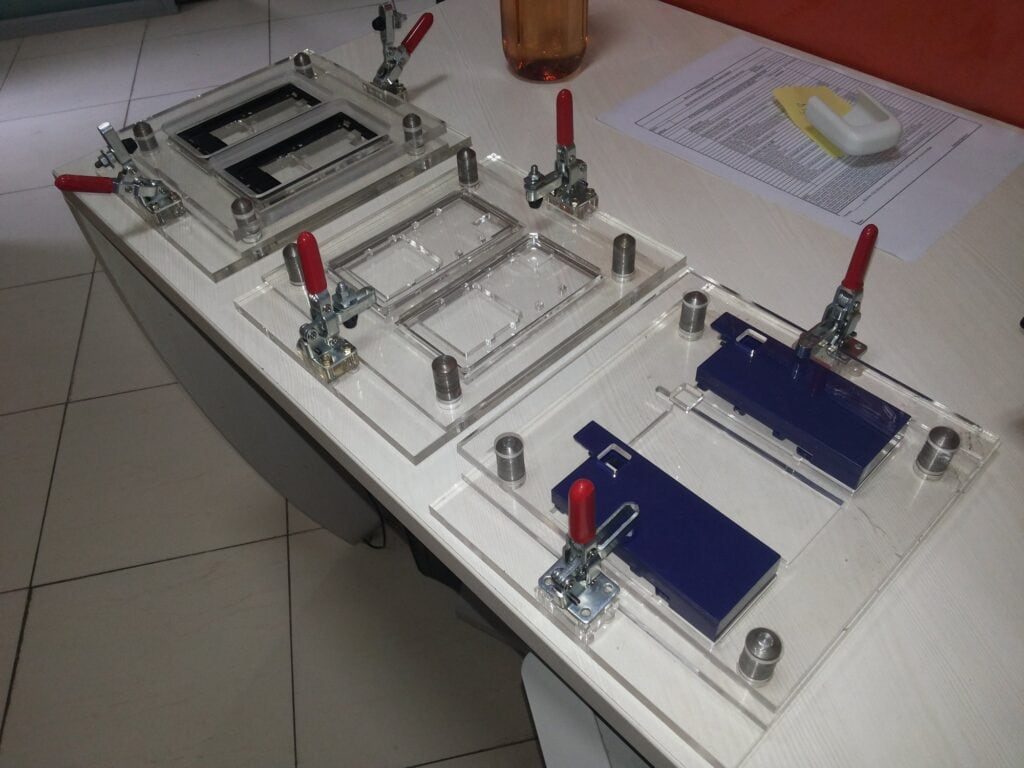
Certifications for Safe Applications
Certifications also play a crucial role in verifying Plexiglass’s compliance with common safety standards. ISO 9001 ensures quality management systems to guarantee consistent production and performance. LEED certification recognizes Plexiglass’s contribution to energy efficiency and sustenance construction. ISO 14001 focuses on environmental management to validate Plexiglass’ sustainability in construction. ISO 45001 addresses occupational health and safety to ensure Plexiglass meets the industry standards.
Maintenance of Plexiglass
- Preserving Clarity and Strength: Proper and periodic cleaning is mandatory to maintain clarity and structural integrity. A solution of warm water and mild soap is enough to remove dirt and grime.
Always clean Plexiglass with a soft cloth or microfiber towel to prevent scratches. Stay away from rough scrubbers, abrasive sponges, or ammonia products. Rinse with clean water to remove soap residue.
- Protective Coatings or Films: They offer an additional layer of defense to enhance plexiglass durability against everyday rigors (wear and environmental exposure). Specialized coatings significantly improve resistance to scratches, making acrylic more suitable for high-contact applications.
Meanwhile, UV-resistant coatings prevent yellowing and degradation over prolonged sun exposure. It also helps the acrylic plastic retain its clarity for outdoor uses. Anti-fog films reduce condensation for visibility in temperature-fluctuating or high-humidity settings (barriers and acrylic windows).
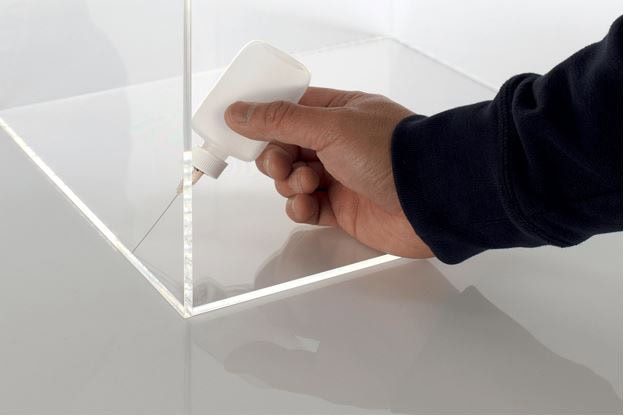
- Repairing Minor Scratches or Cracks: It’s possible to repair minor damages (scratches or small cracks) easily to restore appearance and functionality. A commercial acrylic polish or plastic cleaner can buff the surface to minimize the scratches. Deeper scratches may need fine-grit sandpaper followed by a polishing compound for a smooth finish.
For minor cracks, consider using an appropriate acrylic adhesive or solvent-based glue designed for an acrylic plexiglass sheet. Implementing the sealant can fill the gap to reinforce the damage. But apply the adhesive sparingly and allow adequate curing time to ensure a strong bond. Severely cracked or heavily scratched acrylic may need replacement.
Conclusion
Plexiglass surely stands out among the transparent materials for dependable everyday applications. Its strength, durability, and versatility seem unmatched due to the balance of physical properties. You’ll get impact resistance, optical clarity, and lightweight properties – all in one package. It makes plastic invaluable across diverse sectors, from protective shields and shower panels to lighting fixtures and modern furniture. Its durability enables long-lasting performance under adversity whereas its strength meets functional demands.
Only the high quality plexiglass can deliver reliable and consistent service in terms of safety, design, and integrity. That’s where Jumei Acrylic Manufacturing excels in the global competition with years of innovation, expertise, and satisfaction. We’re ready to help your acrylic projects with the foremost technology, professionals, and standards. Contact us to share your thoughts and receive fact-based expert recommendations.