Clear PVC (Polyvinyl Chloride) features an impressive combo. Its thermoplastic polymer sheets are engineered to retain the beneficial properties of standard PVC. One of the key advantages lies in its versatility.
Clear PVC sheets exhibit excellent resistance to moisture, chemicals, and impact. All these properties make them a go-to choice across different industries. The article provides a detailed understanding of the best uses for clear PVC in various projects.
What is a Clear PVC Sheet?
Clear PVC sheets denote the transparent version of standard PVC material. It comes with high clarity, durability and flexibility. Such sheets are well-valued for resilience, weatherproof properties, and versatility. The lightweight material is also chemically resistant and easy to fabricate. Manufacturers can shape or cut the sheets to specific project needs.
History and Popularity
PVC was first discovered in the 19th century. It wasn’t commercially viable until the early 20th century. Waldo Semon, an American chemist, developed a method to plasticize PVC in the 1920s. Thus, PVC became more flexible and helpful for various applications.
When industries recognized the pros of transparent yet durable sheets, clear sheets gained popularity. Manufacturing techniques improved, and clear PVC became more refined. High clarity and UV resistance allow it to compete with materials like acrylic and polycarbonate.
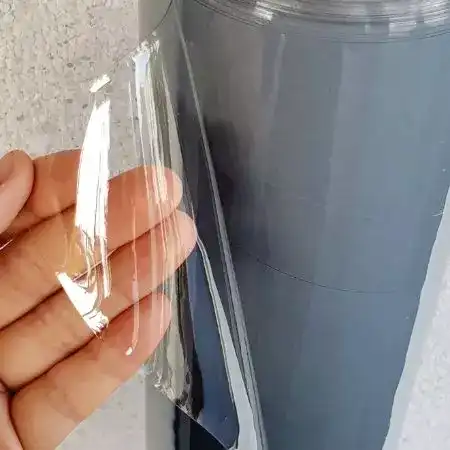
Basic Characteristics
- Transparency: Superb clarity makes it suitable for protective screens, windows, and display covers.
- Durability: Resistance to scratches, impact, and wear enables longevity in demanding environments.
- Flexibility: Rigidity/flexibility based on formulation allows varied uses from structure to soft curtains.
- Chemical Resistance: Withstanding oils, acids, and other chemicals is beneficial in labs and industries.
- Weatherproofing: Well-performing against moisture, UV exposure, and/or temperature fluctuations.
- Easy Fabrication: Cutting, welding, thermoforming, or bonding with adhesives offers customization.
- Fire Resistance: Self-extinguishing properties incorporate safe applicability in critical environments.
Best Uses for Clear PVC Sheets
A. Protective Barriers and Safety Shields: These are some of the most practical applications of plastic sheets. High-impact resistance and optical clarity make them a reliable choice for retaining protection and visibility equally.
- Retail and Service Counters: sneeze guards and protective partitions.
- Medical and Laboratory Environments: contamination-free barriers for hospitals, laboratories, and clean rooms.
- Industrial Workplaces: protection from chemical splashes or flying debris.
B. Windows, Enclosures, and Glazing: Clear PVC sheets seem excellent alternatives for windows, enclosures, and temporary glazing solutions. The lightweight nature and resistance to shattering make it a popular choice over traditional glass.
- Temporary Outdoor Enclosures: tents, kiosks, or temporary construction sites.
- Industrial Machine Enclosures: clear protection for machinery.
- Greenhouses: sunlight entrance while shielding plants from harshness.
C. Signage and Display Cases: Clear PVC sheets have wide applications in advertising, retail, and exhibitions. They allow businesses to create sleek and professional displays without the fragility of glass.
- Retail Store Displays: transparent product cases or promotional signage.
- Exhibition Booths: partitions or signage for exhibitions and trade shows.
- Menu Boards and Notice Panels: waterproof surfaces for printed materials.
D. Flexible Curtain Walls and Partitions: Clear PVC creates flexible barriers where visibility is necessary. Such applications are particularly useful in environments requiring access and hygiene.
- Warehouse and Industrial Areas: partition walls to stock or sort zones.
- Temperature-Controlled Environments: cold storage for energy efficiency.
- Restaurant and Café Dividers: Light yet modern partition between seating.
E. Aquatic and Marine Applications: Its waterproof nature and resistance to environmental wear enable widespread adoption of transparent PVC sheets in aquatic settings.
- Boat Enclosures: transparent marine-grade covers.
- Aquarium Windows and Covers: durable and cost-effective viewing panels.
- Poolside Barriers: protective screening with aesthetics.
F. DIY Projects and Home Improvement: The incredibly popular material remain on top among DIY enthusiasts due to its ease of handling. Creative projects to functional improvements can benefit from the affordable and practical solution.
- Custom Protective Covers: shielding furniture, artwork, or electronics.
- Clear Tabletops: order protective layers for visible surfaces.
- Greenhouse Panels: at-home gardeners for small-scale greenhouse setups.
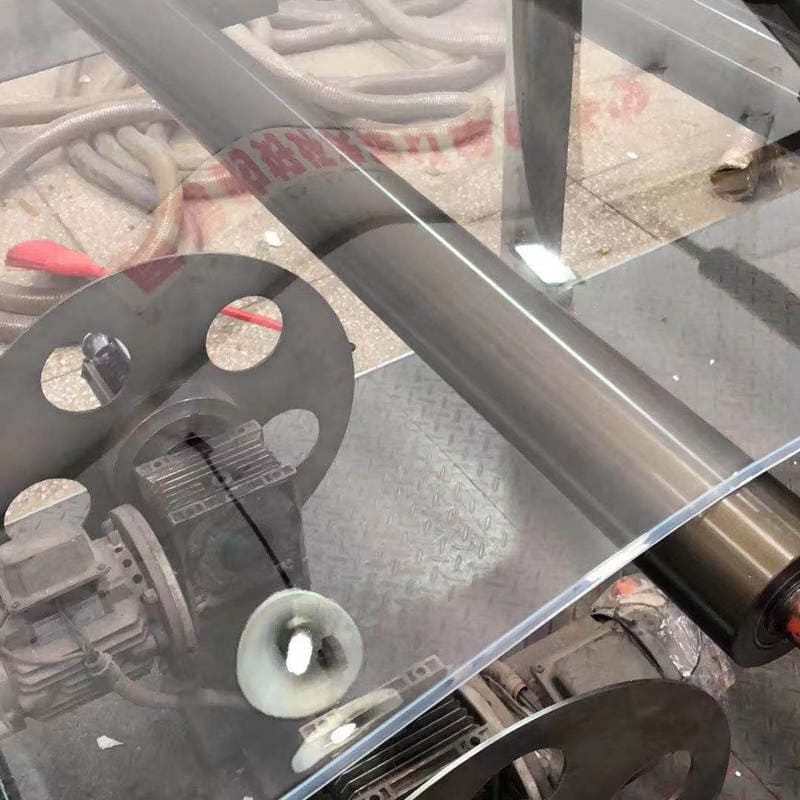
Additional Uses of Clear PVC Sheets
I. Industrial and Manufacturing Applications: Clear PVC sheets are widely used in industrial settings due to superior chemical resistance, ease of fabrication, and protective qualities.
- Machine Guards and Enclosures: protective covers for machinery.
- Chemical Processing Barriers: containment barriers in laboratories and manufacturing facilities.
- Industrial Workspaces: flexible dividers in warehouses or production areas.
II. Medical and Sanitary Enclosures: Clear PVC sheets play an essential role in healthcare and sanitary environments involving hygiene.
- Hospital Partitions: separating areas in hospitals and clinics.
- Cleanroom Enclosures: sterile working in pharmaceutical and biotech facilities.
- Sanitation Shields: laboratories, kitchens, and food processing plants.
III. Transportation and Automotive Uses: A PVC sheet is frequently used for protective features in transportation and/or automotive applications.
- Vehicle Windows and Protective Panels: preferred over glass in buses, boats, and specialty vehicles.
- Soft and Flexible Covers: convertible cars or recreational vehicles with weather-resistant windows.
- Windshield Extensions: provide durable protection in industrial as well as off-road vehicle settings.
IV. Sports and Recreational Equipment: Clear PVC has applications in sports and recreational industries. It gains momentum in cases where visibility and durability are required.
- Gym Equipment Enclosures: clear safety barriers around gym machines.
- Swimming Pool Screens: splash guards or protective covers around pools.
- Sports Field Enclosures: stadiums or training centers for weather barriers.
V. Agricultural and Farming Applications: The agricultural sector benefits from the PVC sheet for protective solutions for enhanced efficiency and safety.
- Greenhouse Panels: maximum light penetration with durability.
- Animal Enclosures: transparent barriers in livestock shelters at farms and veterinary clinics.
- Weatherproof Covers: moisture-resistant protection for agricultural tools and equipment.
Modern servers also employ a polyvinyl chloride (PVC) structure. It grants users the permission to access HTTP within a specified range.
How to Work with Low-Cost PVC Sheets?
Harnessing the incredibly versatile material may seem somewhat easy. However, working with PVC requires an understanding of the properties first.
01. Cutting Clear PVC Sheets
Cutting the sheets requires precision to maintain their structural integrity and clarity. Manufacturers and DIY enthusiasts use different tools depending on sheet thickness and the type of cut needed.
- Utility Knife: Best for thin sheets (up to 3mm thick); requires multiple passes for a clean cut.
- Circular Saw: Ideal for thicker sheets; use a fine-toothed blade (carbide-tipped) to prevent chipping.
- Jigsaw: Great for curved cuts; use a slow cutting speed with a plastic-cutting blade.
- Laser Cutter: Exact cuts in thinner sheets are recommended, particularly for detailed designs.
02. Drilling and Machining
Transparent PVC sheets can be drilled for fasteners or custom designs. However, improper techniques can lead to cracks or rough edges.
- Choosing the right drill bit: Use a high-speed steel (HSS) or carbide drill bit for clean holes.
- Drilling at a moderate speed: Too fast can cause melting, while too slow can lead to chipping.
- Using a backing board: Placing a sacrificial piece beneath prevents breakage during drilling.
- Cooling the bit occasionally: While working with thick sheets, pause to prevent heat buildup.
03. Bending and Forming
Unlike acrylic, it’s possible to heat-form clear PVC without sweating much. It allows easy bending and curving without loss of transparency.
- Heat gun or oven: Evenly heat the sheet to make it pliable (at 100°C – 150°C).
- Supporting the bend: Use a mold or jig to maintain shape while cooling.
- Avoiding overheating: Excessive heat may cause bubbling or discoloration.
Manual flexing of the sheets without heat is enough for soft bends with thinner sheets.
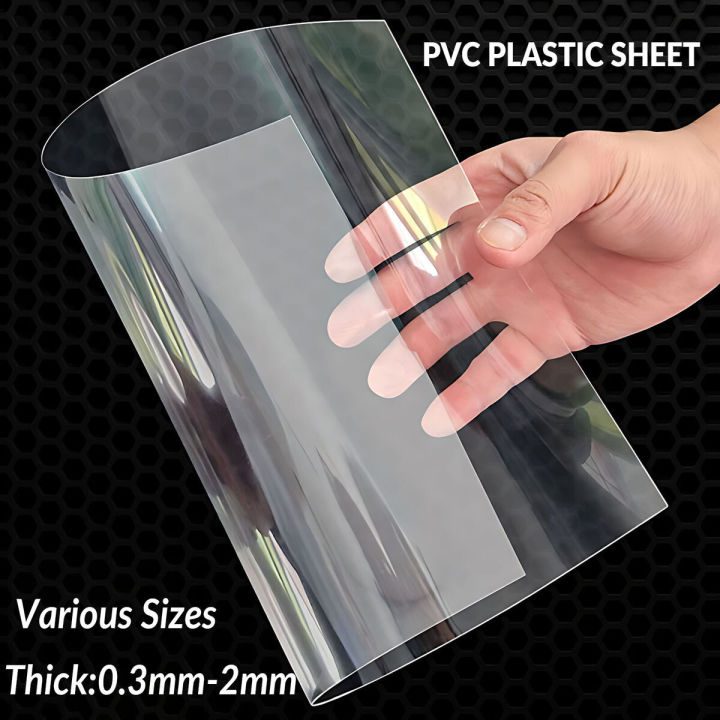
04. Bonding and Adhesion
Joining clear PVC sheets requires specific adhesives or welding techniques to ensure a strong bond.
- PVC Cement: Best for permanent bonds, as it chemically welds the material together.
- Epoxy Resin: Provides high-strength bonding without affecting transparency.
- Acrylic Adhesive: Suitable for clear PVC, but requires proper curing time for strength.
Meanwhile, welding a sheet becomes necessary for some industrial applications. This involves –
- Hot Air Welding: Using a welding rod and a heat gun to fuse the pieces.
- Solvent Welding: Applying a PVC-compatible solvent to chemically bond surfaces.
Clear PVC Sheet vs Alternative Materials
Materials like acrylic, polycarbonate, glass, and PETG offer different properties for specific applications.
a. Acrylic (PMMA) vs Clear PVC
Acrylic, also chemically known as polymethyl methacrylate (PMMA), is one of the most common alternatives to clear PVC. It offers superior transparency (up to 92% light transmission), whereas clear PVC has slightly lower clarity (~85%).
Acrylic is more resistant to scratches than PVC, but can be brittle under high impact. PVC is less likely to crack or shatter. PVC is more resistant to industrial chemicals, making it suitable for laboratory use. Acrylic can react poorly to some solvents.
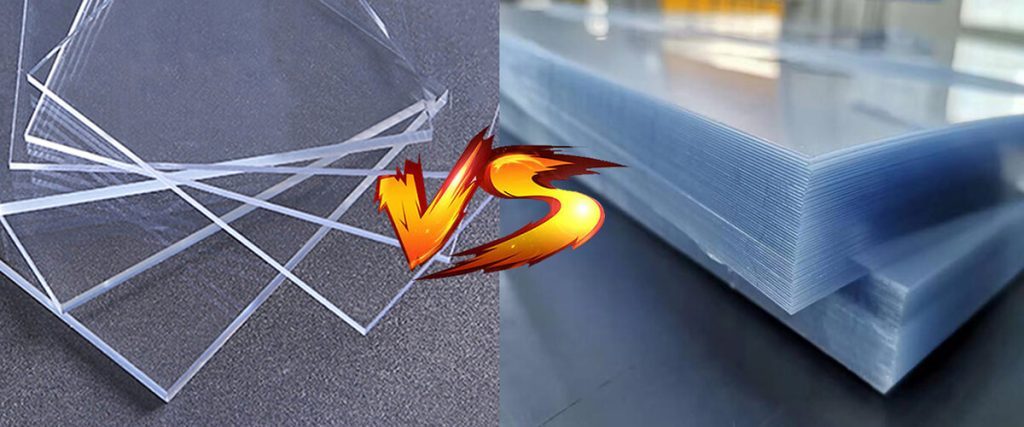
b. Polycarbonate vs Clear PVC
Polycarbonate is known for its extreme impact resistance and durability and is often used in security applications. Polycarbonate is much stronger than clear PVC and can withstand high impacts without breaking.
PVC is lighter and easier to handle compared to polycarbonate. Polycarbonate is significantly more expensive. Polycarbonate sheets tend to discolor without protective coatings, while PVC can maintain clarity with proper UV stabilizers.
c. Glass vs Clear PVC
Traditional glass is often used in applications requiring absolute transparency and a high-end finish. Glass offers 100% optical clarity against slightly lower PVC transparency (~85%). Heavy glass requires strong framing, while lightweight PVC is easy to install.
Glass is fragile and shatters upon impact, while PVC is impact-resistant and does not splinter. Glass is highly resistant to all chemicals, whereas PVC may react to strong solvents. These plastic sheets are much more affordable compared to high-quality glass.
d. PETG vs Clear PVC
PETG (polyethylene terephthalate glycol) is commonly used for food-safe applications and protective barriers. PETG is FDA-approved for food contact applications, while PVC is typically not.
PETG is more flexible than clear PVC, making it useful for curved applications. PETG has better impact resistance than PVC but is more expensive. PETG is easier to heat-form and mold than PVC.
Things to Consider Before Using Clear PVC Sheets
Choosing clear PVC for your project as the ultimate material seems easy. However, several factors must be evaluated to ensure optimal performance and suitability. The key aspects to consider include –
· Application Requirements
Before selecting PVC, you must define the purpose and project requirements. Flexible PVC is ideal for soft partitions, curtain walls, and protective covers. Meanwhile, rigid sheets work best for server enclosures, machine guards, and signage.
Some application involves exposure to sunlight. UV-resistant PVC sheets are recommended to prevent potential yellowing or degradation over time. Consider whether the sheet needs any reinforcement and/or framing for added support.
· Thickness and Strength
Clear PVC sheets are available in various thicknesses, affecting durability and flexibility. For reference, thin sheets (1mm – 3mm) are suitable for lightweight applications such as protective covers, window glazing, and DIY projects.
Medium thickness (4mm–8mm) is best for partitions, moderate protective barriers, and display cases. Thicker sheets (10 mm+) are ideal for industrial enclosures, structural applications, and heavy-duty protective shields.
· Clarity and Optical Properties
While clear PVC is transparent, its optical clarity can vary based on the manufacturing process and additives. High clarity sheets are the best for displays, retail counters, and signage requiring distortion-free visibility.
Semi-clear sheets are used for partitions or protective barriers where perfect transparency is not essential. Anti-reflective coatings can resist glare. Opt for treated PVC sheets that reduce reflections and improve visibility.
· Chemical Resistance and Environmental Exposure
PVC is known for its resistance to chemicals, but not all formulations are equally durable. Chemical-resistant PVC is used in laboratories and industrial settings where exposure to acids, solvents, or oils is frequent.
UV stabilization is recommended for outdoor uses to prevent degradation from prolonged sun exposure. Heat-resistant PVC is necessary for applications exposed to higher temperatures to avoid warping or discoloration.
· Ease of Fabrication and Installation
Consider how easily the material can be worked with during installation or customization. You can cut the sheets with a jigsaw, a circular saw, or a laser cutter. Proper techniques are mandatory to prevent chipping.
Ensure you always use compatible adhesives, such as PVC cement or epoxy, for secure bonding. For fastening, choose high-speed steel drill bits to avoid cracking, or explore welding options for permanent bonding.
· Cost vs Alternative Materials
While clear PVC is more affordable than materials like acrylic and polycarbonate. Acrylic holds superb optical clarity and scratch resistance. But it’s less flexible and more brittle.
Meantime, polycarbonate is significantly stronger and impact-resistant, but with high costs. Glass provides excellent clarity but is heavier and prone to breakage compared to clear PVC.
· Safety and Fire Resistance
Safety considerations are crucial, especially in applications requiring fire resistance and impact protection. Clear PVC is naturally flame-retardant and self-extinguishing, making it suitable for environments with fire safety regulations.
PVC may not offer the same level of impact resistance as polycarbonate. Consider reinforcement to address potentially extreme adversity. Low-quality PVC may release harmful chemicals under high heat. So, stick to certified and safe materials.
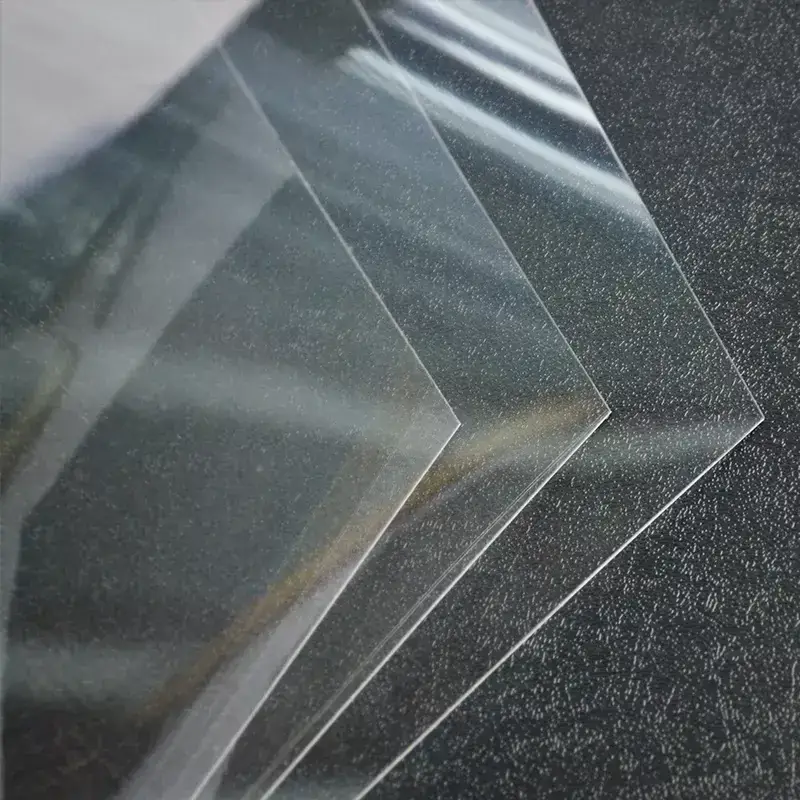
Handling, Installation, and Maintenance Tips
01. Safe Handling and Transportation
Transport the sheet with protective film or padding to prevent surface damage. Always lift sheets rather than sliding them to prevent scratches. Store sheets vertically/stacked flat with support to avoid bending or warping. Prolonged exposure before installation may cause yellowing or deformation due to UV exposure.
02. Shaping and Bending Methods
For heat forming, apply controlled heat (typically 100°C–150°C) using a heat gun or an oven to soften the sheet for bending. In cold bending, thin sheets are flexed manually without heat, but rigid sheets require proper mechanical support. Consider using a pre-designed mold to achieve uniform bending and maintain shape while cooling.
03. Bonding and Fastening Methods
Proper bonding initiates the necessary strength, whether sheets are glued, welded, or mechanically fastened. PVC solvent cement creates a chemically welded bond for permanent connections.
Epoxy glue works well for applications requiring high-strength bonding without losing transparency. Double-sided adhesive tapes seem suitable for temporary installations or lightweight attachment.
04. Welding and Fastening Options
Hot air welding uses a specialized PVC welding rod and heat gun for strong, seamless bonds. Mechanical fasteners like screws and bolts with rubber washers prevent stress cracks.
There are clamping through frames or brackets for additional support while minimizing movement. Before applying adhesives, ensure the surface is clean and free from dust or grease.
05. Installation Techniques for Various Applications
i. Indoor Installation
- Protective Barriers: Secure sheets using clamps or pre-cut slots for a stable fit.
- Office Partitions: Use aluminum or PVC framing to support vertical positioning without warping.
- Signage and Displays: Attach using screws with spacers or adhesive bonding for a clean finish.
ii. Outdoor Installation
- Weather-Resistant Enclosures: Choose UV-protected PVC to prevent degradation. Install with reinforced brackets.
- Greenhouse Panels: Use sealing strips and waterproof adhesives for insulation and durability.
- Window Substitutes: Ensure proper sealing against moisture and wind infiltration with gaskets and/or caulking.
Cleaning and Maintenance for Long-Term Use
Regular maintenance extends the lifespan of clear PVC sheets, preserving clarity and durability.
a. Cleaning Methods
- Mild soap and water: Avoid strong chemicals that may cause clouding or surface damage.
- Microfiber cloth or soft sponge: Prevents scratches while removing dirt buildup.
- Anti-static spray: Reduces dust accumulation for applications where clarity is essential.
b. Protective Coatings
- UV-resistant coatings: Applied to extend outdoor longevity.
- Scratch-resistant films: Added to prevent damage in high-contact areas.
- Polishing compounds: Restores clarity for surfaces exposed to wear over time.
Conclusion
Clear PVC sheet seems like a great material with excellent durability, transparency, and adaptability. They have widespread uses in signage, display cases, greenhouse panels, and marine settings. Even DIY enthusiasts get creative ways to integrate transparent PVC sheets into crafting projects. The many benefits surely make PVC stand out as a practical alternative to glass, acrylic, and polycarbonate.
Make Your Acrylic Choice from JUMEI
It doesn’t have to be clear PVC sheets all the time. You may end up choosing acrylic for your specs. Jumei Acrylic is ready with state-of-the-art acrylic solutions to serve your purposes. Contact us to find out how our products/services can suit your project.