Acrylic has been a highly exercised material across many industries due to its durability, transparency, adaptability, and versatility. From architecture and signage to furniture and electronics, acrylic plastics are key elements for contemporary design and functionality. This comprehensive article explores the manufacturing processes of plastic materials. It includes fabrication techniques as well as common applications.
What is Acrylic?
Acrylic, aka plexiglass or PMMA (Polymethyl Methacrylate), is a synthetic polymer (thermoplastic). The transparent plastic material derives from methyl methacrylate (MMA).
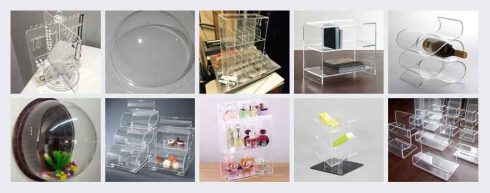
Features/Properties of Acrylic
- Transparency
Acrylic plastic allows up to 92% of light to pass through, making it an excellent glass substitute.
- Lightweight
Clear acrylic is incredibly light for easy handling, transportation, and installation in commercial applications.
- Durability
Highly durable acrylics can resist cracks, breaks, yellows, and harsh weather conditions. It also possesses high impact resistance.
- UV Resistance
Acrylic is naturally resistant to UV. It doesn’t degrade, discolor, or become brittle under sunlight.
- Thermoformability
It’s possible to mold acrylics into various shapes at elevated temperatures without losing strength or clarity.
- Chemical Resistance
Acrylic possesses excellent resistance to chemical reactions. It can withstand elements like oils, alcohol, and diluted acids to industry standards.
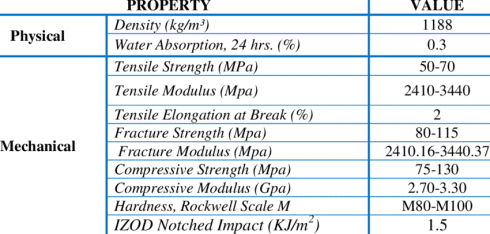
How is Acrylic Manufactured? An Overview
There are different methods to manufacture acrylic. However, the two primary methods involve –
A. Extrusion Process
The plastic fabrication method goes well with mass production. The resulting sheets may have slightly less optical clarity and somewhat thinner thicknesses. Extrusion involves the following processes –
- Feeding: Solid PMMA gets fed (inserted) into an extruder, a heating-and-melting machine.
- Melting: Poly methyl methacrylate is heated to 200°C – 250°C (392°F – 482°F) to transform into a viscous liquid.
- Shaping: Liquid PMMA gets forced through a die (a mold) to form sheets or films. Shape and thickness depend on the die used and extrusion conditions.
- Cooling: The sheets are cooled and hardened through air cooling or in a water bath.
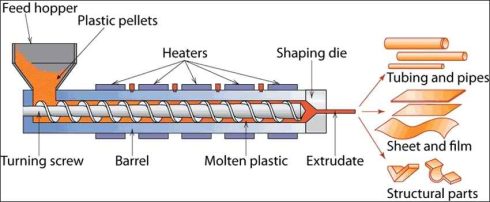
Extruded acrylic is affordable for large-scale production as it’s a high-speed and continuous method. It maintains uniform thickness for the acrylic sheets across the entire length.
B. Casting Process
Cast acrylic demonstrates superior optical clarity, greater thickness, and better quality control. It’s used for applications in various industries requiring high precision. Casting features the following processes –
- Mold Preparation: PMMA is mixed with a catalyst and poured into metal or silicone molds.
- Polymerization in Mold: The mixture gets heated in the mold for the polymerization process.
- Cooling: The casted acrylic is allowed to cool slowly and harden to maintain its shape.
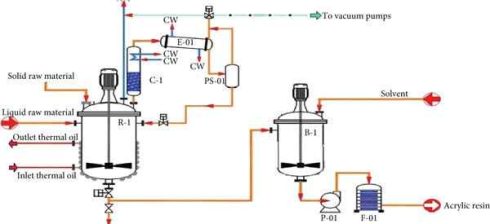
The slower method makes it problematic for large-scale acrylic plastic materials manufacturing. Cast acrylic is primarily produced in flat sheets, not specific profiles (rods, tubes, or channels).
Acrylic Manufacturing: Step-by-Step
Step #01 – Production of MMA Monomer
MMA originates from petrochemical sources. The founding raw materials include – Acetone, Hydrogen Cyanide (HCN), Methanol, and Propylene. MMA production involves the “acetone cyanohydrin process,” where acetone and hydrogen cyanide form acetone cyanohydrin.
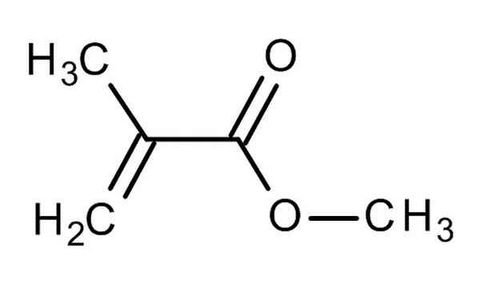
It’s later converted into MMA through a series of further chemical reactions. The synthesized MMA goes through a purification process to prevent contamination. It delivers high-quality materials with sufficient clarity that are suitable for continuous bulk polymerization.
Step #02 – Polymerization of MMA into PMMA
Manufacturers’ preferred polymerization process vary depending on the intended properties of the final plastics. The topmost methods are –
i. Bulk Polymerization: MMA gets heated to a high temperature in a reactor with an initiator (peroxide or azo compound).
ii. Suspension Polymerization: MMA gets dispersed in water with the assistance of a suspending agent. The polymerization process takes place within the suspension medium.
iii. Solution Polymerization: MMA gets dissolved in a solvent and polymerized using a chemical initiator. It eventually produces a PMMA solution.
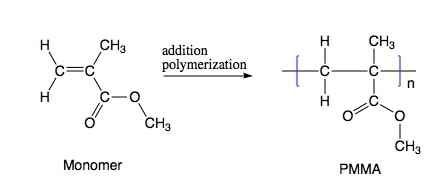
The process is closely monitored for factors like molecular weight and degree of polymerizing. It ensures the resulting polymethyl methacrylate pmma harnesses the desired mechanical and optical properties. The PMMA is cooled and solidified into a raw form (acrylic resin) upon completion of polymerization.
Step #03 – Extrusion or Casting of Acrylic Sheets
After polymerization, PMMA is ready to be processed into various forms. As discussed, extrusion and casting are the two primary methods for shaping acrylic sheets.
Step #04 – Cutting and Shaping of Acrylics
The acrylic materials are formed and need to be cut, shaped, and prepared for final use. Those engineering plastic sheets undergo one of the following processes based on design specifications –
a) Cutting: Acrylic sheets are cut into multiple pieces using various tools. Laser cutters are for detailed or intricate parts. CNC routing can achieve complex shapes for large-scale production.
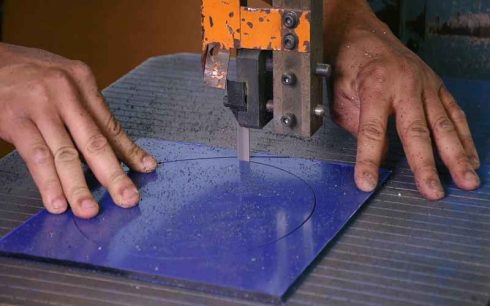
b) Shaping and Molding: Acrylics are heated and molded into specific shapes using thermoforming techniques for custom (highly curved or 3D) designs.
Step #05 – Polishing and Finishing
Acrylic plastics require additional steps to ensure a top-quality finish. The foremost methods are –
i. Flame Polishing: A flame to the acrylic edges melts them slightly for a smooth, glossy finish.
ii. Mechanical Polishing: Acrylic surfaces and edges can lay under polishing wheels and abrasive pads.
iii. Surface Coating: Surfaces get treated with special coatings for excellent resistance to scratch, UV, and/or glare.
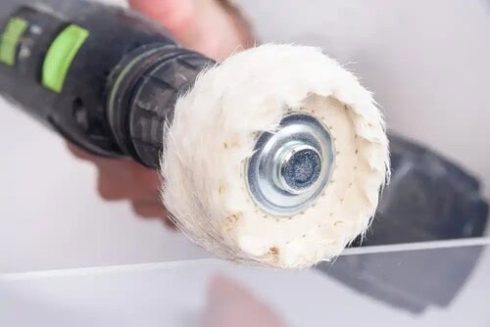
Types of Acrylic Manufacturing
The versatile plastic fabrication primarily produces either of three acrylic types – cast, extruded, and coated acrylic.
01. Cast Acrylic
It’s made by polymerizing methyl methacrylate (MMA) in a mold. This process involves pouring liquid MMA into a mold and heating the material. It allows the material to solidify and form a sheet.
Features of Cast Acrylic
- Superior Optical Clarity
- Thicker Sheets
- Enhanced Durability
- Customizable
Applications of Cast Acrylic
- Illuminated or high-end signage.
- Lenses, eyewear, and optical devices.
- Tabletops and display cases.

02. Extruded Acrylic
It’s produced by forcing heated acrylic resin through a die to form continuous sheets or shapes. Extrusion is a highly automated process that produces thin acrylic plastic sheets.
Features of Extruded Acrylic
- Cost-Efficient
- Uniform Thickness
- Lower Clarity
- Limited Thickness
Applications of Extruded Acrylic
- Signs and displays.
- Light diffusers or covers.
- Protective covers or light paneling.
03. Coated Acrylic
It refers to acrylic sheets with an additional protective coating applied to the surface. It enables the enhancement of engineering plastics in scratch resistance, UV stability, or anti-glare characteristics.
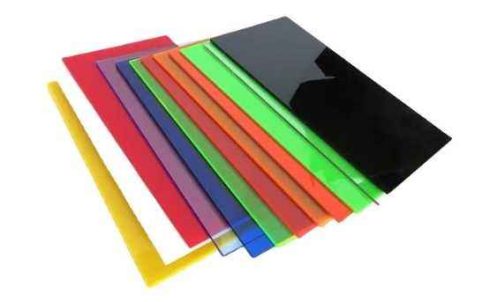
Features of Coated Acrylic
- Durability
- Customization
- Longevity
Applications of Coated Acrylic
- Car windows, light covers, and dashboards.
- Medical equipment/medical devices.
- Protective screens, lenses, and displays.
Applications of Acrylic Products
· Signage and Displays
ð Illuminated Outdoor Signs
ð Retail Displays
ð Point of Sale Displays (POS)
ð Directional and Informational Signage
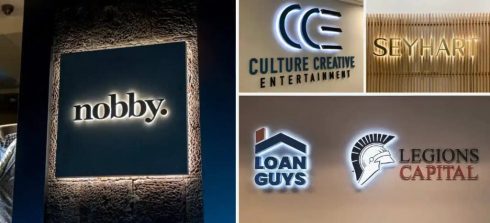
· Optical Applications
ð Lenses (eyeglasses and sunglasses)
ð Protective Screens for Electronics
ð Optical Instruments (magnifiers)
· Automotive Applications
ð Headlamp Covers
ð Windows and Windscreens
ð Interior Components
ð Marine (boat windows, portholes, and viewports)
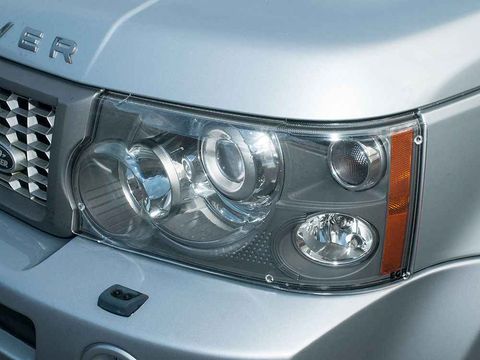
· Furniture and Interior Design
ð Furniture (tables, chairs, bookshelves)
ð Home Décor and Accents
ð Lighting Fixtures (pendant lights, chandeliers, sconces)
· Medical and Healthcare
ð Medical Devices
ð Surgical Instruments and Containers
ð Protective Barriers and Shields
ð Dental Applications
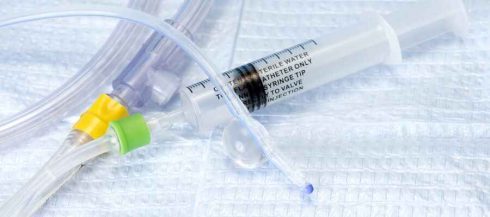
· Construction and Architecture
ð Windows, Roof Panels, and Skylights
ð Decorative Wall Panels and Facades
ð Interior Partitions and Dividers
Techniques for Acrylic Fabrication
Acrylic plastic fabrication involves multiple techniques for custom shapes, smooth edges, and intricate designs. Three of the most commonly employed techniques in acrylic fabrication are – 1) laser cutting, 2) CNC machining, and 3) drilling and polishing.
A. Laser Cutting
A high-powered laser beam cuts or engraves acrylic sheets. This method can produce intricate and detailed cuts for designs.
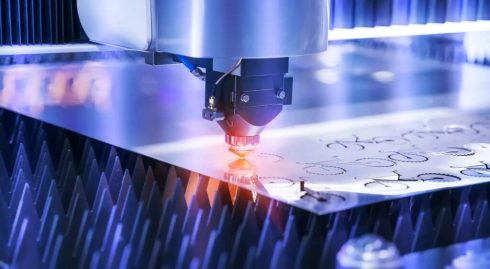
Applications include creating intricate logos, text, shapes, and customized displays, holders, and exhibition pieces.
B. CNC Machining
Computer Numerical Control machining utilizes a computer-controlled tool to carve/mill acrylic sheets into desired shapes and designs.
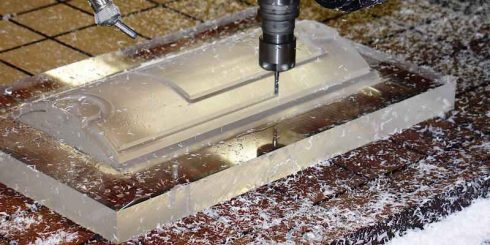
CNC machining can produce custom parts where precise dimensions are critical, including prototypes.
C. Drilling and Polishing
They’re essential finishing techniques in acrylic fabrication. Drilling creates holes in acrylic for mounting, assembly, or functional needs.
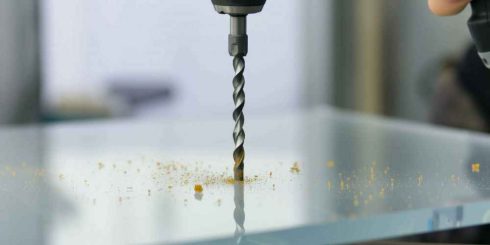
Drilling allows precise hole placement for mounting and attachments (stands, shelves, or light fixtures). Polishing is time-consuming for larger or more complex pieces.
How to Choose the Right Acrylic Manufacturing Process?
Only the best acrylic manufacturing process can deliver absolute precision. It also depends on factors like industrial applications, properties, design complexity, production volume, and cost.
i. Product’s Application
Different applications require different material selection, properties, and precision. For instance, laser/CNC goes well with pop displays with smaller widths. Optical lenses and eyewear rely on casting and Polishing. Acrylic furniture should go for machining services and laser cutting.
ii. Design Complexity
The complexity directly influences the process. Simple designs benefit from mass-production processes. Meanwhile, complex and detailed designs may require precise processes (laser cuts). Extrusion is good for simple shapes.
Drilling is suitable for creating holes in an acrylic material. Laser cuts enable intricate cuts with superb precision. Thus, the versatile material can make detailed designs. CNC machining is excellent for complex geometries and 3D shapes.
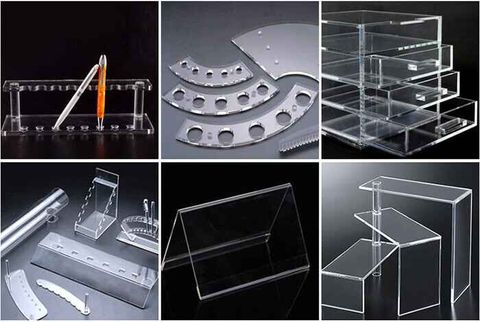
iii. Production Volume
High production volumes can benefit from high-speed processes. In contrast, custom works may require labor-intensive and precise methods. Extrusion seems ideal for long runs of sheets, rods, or profiles. CNC/laser provides flexibility and precision without high setup costs.
iv. Material Thickness and Strength
Thicker and stronger parts usually require casting or CNC machining. On the contrary, thin and light ones are better suited to extrusion or laser cutting.
v. Surface Finish and Edge
Acrylic products require smooth edges, especially in signage, display cases, and furniture. The surface finish can affect its aesthetic appeal and functional performance. Laser cutting and flame polishing are the ideal processes for smooth edges.
vi. Cost Considerations
The cost of materials, labor, machinery, and setup time will differ between processes. Extrusion is cost-effective for mass production. Laser cutting is efficient for custom shapes. CNC requires high setup costs. Casting is also expensive due to mold creation and long processing times.
Conclusion
The acrylic manufacturing process is an efficient solution for high-quality product requirements. From the polymerization of MMA into PMMA to shaping, cutting, and finishing, additional processes make it the ideal material for various applications.
It enables businesses to get innovative and functional products with optimized industry standards. Whether it’s laser cutting, casting, CNC machining, or extrusion, custom acrylic fabrication can bring designs to life with precision in a cost-effective way.
Choose JUMEI ACRYLIC for Your Acrylic Fabrication Requirements
Are you looking for custom acrylic solutions for your next project(s)? Jumei Acrylic Manufacturing specializes in mass acrylic production and has years of experience with industry-leading experts. Contact Us now for pro-level consultation on acrylic products.