Acrylic and Perspex are popular materials that are often confused due to their similar appearance and applications. Both have extensive uses across industries like construction, design, and DIY. But they possess unique properties that set the two apart. This article digs deep into the differences and similarities between acrylic and Perspex, helping you make the right choice.
What is an Acrylic Sheet?
Polymethyl methacrylate (PMMA) is the chemical name for acrylic. The transparent thermoplastic also goes by acrylic glass or ice rinks. The term “acrylic” is an umbrella term with various brand names and acrylic sheet types.
Make no mistake: all acrylic sheets share the same core chemical composition. But they may differ in production methods and common applications. Acrylic is commonly used as a lightweight and shatter-resistant alternative to traditional glass.
History and Development
German chemists Otto Röhm and Walter Bauer first synthesized PMMA in 1933. Its commercial production began in 1936 under the brand name ‘Plexiglas.’ However, acrylics gained prominence during World War II.
The plastic was extensively employed in aircraft canopies, submarine periscopes, and gun turrets. It’s because the material is lightweight and impact-resistant. Over the decades, acrylic has evolved into a versatile material.
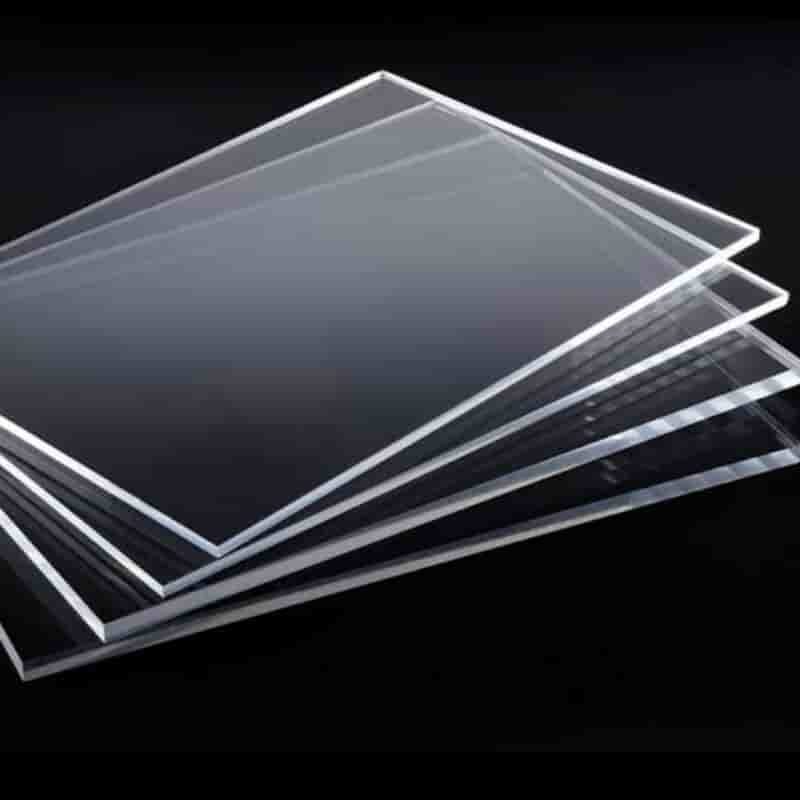
Physical Properties of Acrylic
- Transparency: Acrylic features exceptional optical clarity by transmitting up to 92% of visible light. It makes acrylic sheets one of the most transparent plastics available.
- Impact Resistance: Unlike traditional glass, acrylic is more resistant to impact. It offers immense longevity without sacrificing aesthetics.
- Lightweight: Acrylic measures half the weight (half the density) of standard glass. Therefore, acrylic is easy to transport, handle, and install.
- UV Resistance: It’s highly resistant to ultraviolet light, ensuring it doesn’t yellow or degrade. Even constant or prolonged exposure to sunlight can’t alter the properties.
Types of Acrylic Sheets: Cast vs Extruded
Acrylic is manufactured using two primary methods – cell casting and extrusion. And the outcomes are also different, resulting in various types with unique properties.
- Cast Acrylic: Manufacturers create acrylic sheets by pouring liquid acrylic into molds to harden. Cast acrylic offers superior transparency and greater resistance to scratching.
It usually possesses slight variations in thickness but features further durability and resilience. This type is preferred for high-quality displays, aquariums, and intricate designs.
- Extruded Acrylic: Manufacturers craft extruded acrylic by continuously pushing liquid acrylic through rollers to form sheets. Such acrylic sheets possess superior uniformity in thickness.
They’re easy to fabricate and shape but seem slightly less durable than cast acrylic. Extruded ones are ideal for mass-production applications (signage and point-of-sale displays).
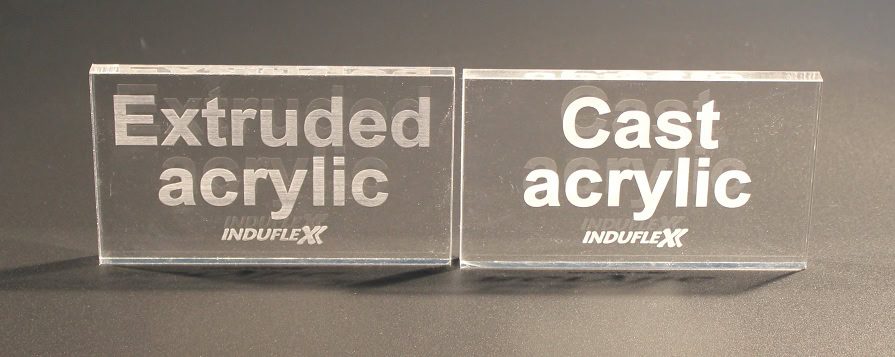
Acrylic holds a unique combination of crucial properties like endurance and adaptability. That’s why it has become a material of choice for everyday items as well as specialized uses. Cast or extruded plastic remains a valuable asset for many projects.
Advantages of Acrylic
- Cost-Effective: Acrylic is a highly economical material. Its affordability seems ideal for budget-conscious tasks, even with durability or visual appeal. Acrylic sheets come in many thicknesses and finishes to offer cost-effective solutions.
- Versatile Applications: Its adaptability lends acrylic to countless sectors. It has been widely adopted in signs, displays, and automobiles due to its customizability. Manufacturers can accommodate different shapes, sizes, and colors relatively easily.
- Ease of Fabrication: Acrylic is remarkably easy to work with, making it a favorite among manufacturers, designers, and DIY enthusiasts. Unlike traditional glass, acrylic sheets can be precisely trimmed and drilled without shattering risks.
- Impact Resistance: Acrylic can resist impact, making it a safer choice for strength-related uses. This property allows acrylic to withstand accidental impact. The additional longevity also increases the lifespan for long-term reliability.
- UV Stability: Acrylic offers excellent resistance to UV rays, preventing yellowing and degradation. It’s a suitable feature to address long-term exposure to the sun. Acrylic’s built-in UV stability retains its overall structural integrity.
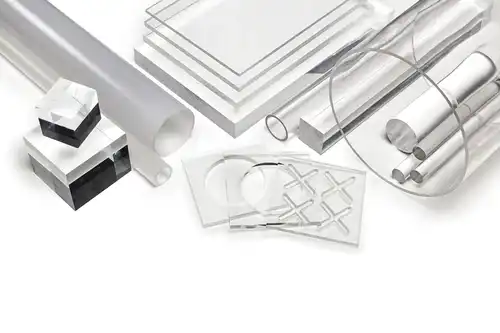
What is a Perspex Sheet?
Perspex, Lucite, or plexiglass is a high-quality (premium) acrylic version. Almost everyone often uses the term interchangeably with acrylic. Perspex stands out for its premium manufacturing process, which is related to superior consistency and optimal performance.
Still, it’s polymethyl methacrylate (PMMA) like standard acrylic. But it comes with strict quality controls and further enhancements for high-end applications. The premium version is also known for exceptional clarity and versatility and remains a highly preferable choice.
History and Evolution of Perspex
Plexiglass has a rich history traces back to the early development of PMMA in the 1930s. It was first commercialized in 1934 by Röhm & Haas under the name ‘Plexiglas.’ The Perspex brand was later introduced, becoming synonymous with premium-quality acrylic.
Just like acrylic, Lucite also gained prominence as a material for aircraft canopies during World War II. The lightweight material’s strong properties and superb transparency led to widespread adoption. It has now evolved to cater to diverse applications.
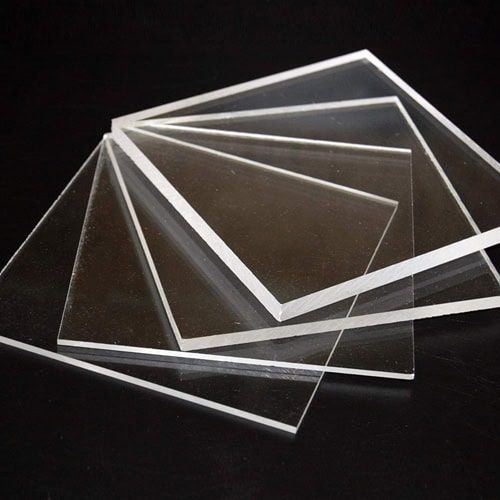
Physical Properties of Perspex
- Transparency: Plexiglass marks the pinnacle (top point) among acrylic materials. It delivers crystal-clear transparency, making it ideal for high visual appeal.
- Scratch Resistance: Some Perspex formulations include advanced scratch-resistant coatings. Greater resilience ensures longevity in environments prone to wear and tear.
- Durability: Like acrylic, plexiglass is highly impact-resistant. Certain formulations enhance its durability, ensuring optimal performance even under demanding conditions.
Manufacturing Quality
Being a premium acrylic brand, plexiglass production maintains stringent quality control standards. The meticulous production process delivers uniform thickness, consistent color, and superior clarity.
Such qualities call for a precise laser cut for engraving and fine edges with tight tolerances. The flawless surface of Perspex sheets is particularly valued in luxury design or engineering applications.
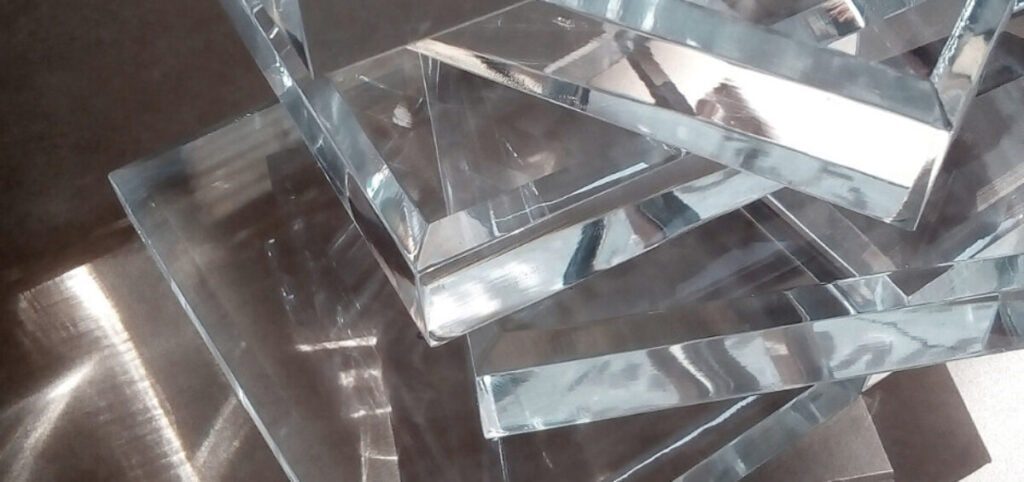
Today, plexiglass continues to push the boundaries of what acrylic can achieve. It acts as a trusted and high-performing material across traditional and modern fields. With creative designs or structural uses, Perspex has set a benchmark for quality in acrylic materials.
Advantages of Perspex
- Superior Quality: Its transparency ensures maximum visibility with minimal distortions. That’s why it’s a preferred choice for projects requiring precise transparency. Its color consistency from the uniform sheeting is crucial for seamless aesthetics.
- Enhanced Scratch Resistance: Many Perspex products are well-coated for protection against scratches. Its features make plexiglass ideal for high-traffic environments where surfaces are frequently touched or exposed to abrasive solvents.
- Durability: Perspex offers remarkable durability, surpassing standard acrylic in several aspects. It resists yellowing and degradation under prolonged exposure to sunlight. Additionally, the robust formulation can withstand wear and tear in any environment.
- Brand Reputation: Perspex carries significant trust and credibility. The reliable material from limited brands incorporates added confidence to customers. It’s quite beneficial in professional tasks where trustworthiness is a top priority.
- Aesthetic Appeal: Plexiglass is highly regarded for its premium finish and aesthetic appeal. Its flawless surfaces and vibrant color options allow for making visually striking installations and displays. Perspex offers unique finishes for limitless creative possibilities.
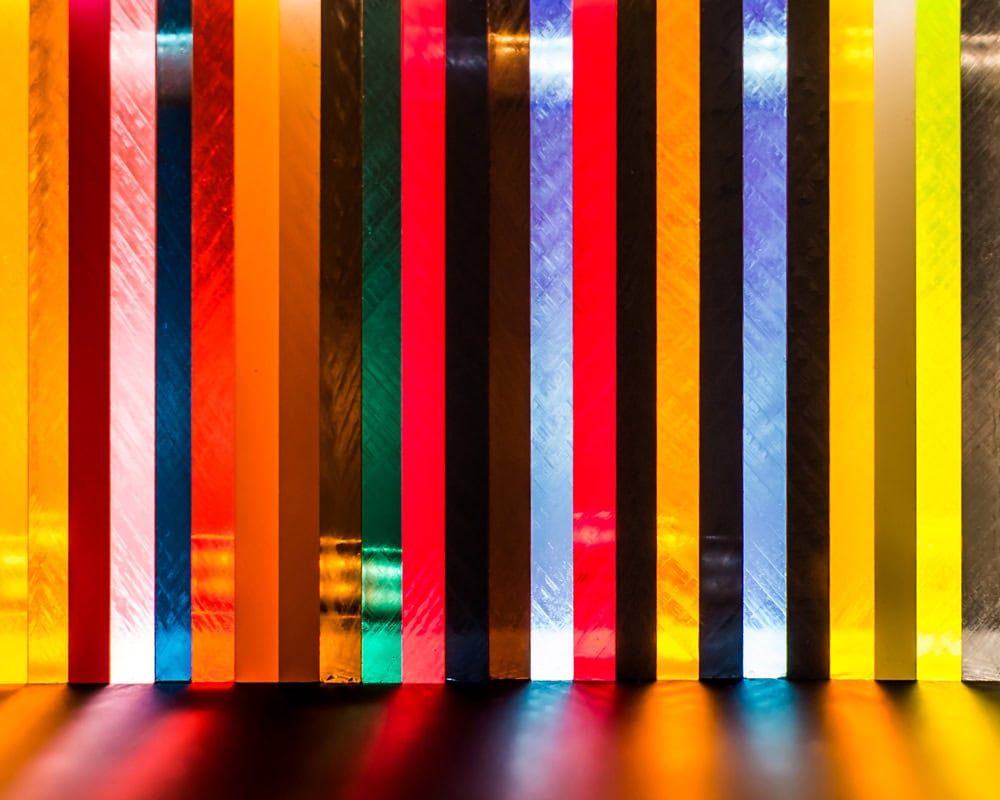
Key Difference: Are Acrylic and Perspex the Same Material?
Featuring the same chemical compound, the two share considerable similarities in physical properties. However, there are some subtle differences between Perspex and acrylic, which are simplified below.
a. Material Composition
- Acrylic: It’s the overarching term for a transparent thermoplastic material from polymethyl methacrylate (PMMA). Acrylic’s versatility, strength, and aesthetics make it an industry favorite across construction, art, and design applications.
It’s also available in many standard as well as specialized types to meet diverse project needs. Aside from transparency, its impact resistance, lightweight nature, and UV stability puts acrylic in a great position as a strong glass alternative.
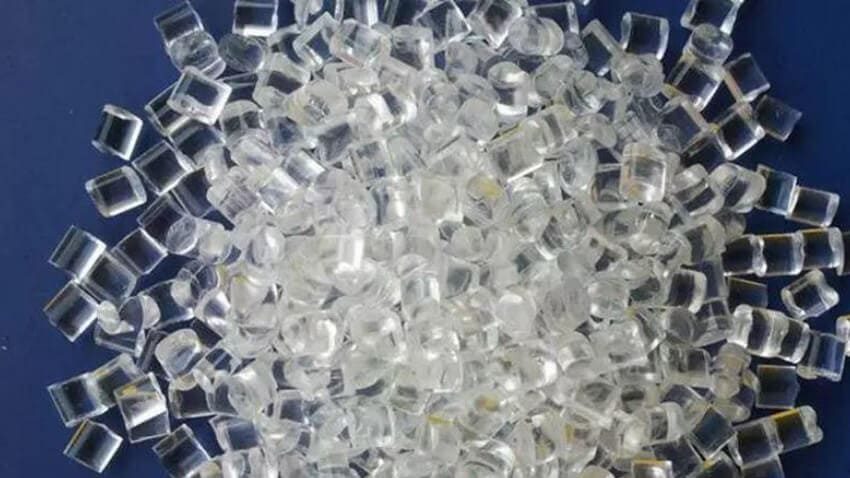
- Perspex: Acrylic refers to the generic term or the whole product category. But Lucite represents a high-quality branded version of acrylic. Plexiglass is a recognized trade name synonymous with premium acrylic sheets.
Although chemically identical to PMMA, Perspex distinguishes itself through rigorous manufacturing with strict quality controls. Such enhancements ensure greater consistency, superior clarity, and added performance features.
b. Clarity and Optical Properties
- Acrylic: Outstanding transparency by transmitting up to 92% of visible light makes acrylic a direct glass substitute. Such transparency makes it a go-to material for applications requiring clear visibility. Acrylic is highly effective in maintaining optical quality over time.
It incorporates high UV resistance to prevent yellowing or discoloration even after prolonged exposure to sunlight. However, the optical finish of acrylic can vary depending on the manufacturing process (cast vs. extruded), with cast acrylic often having the upper hand.
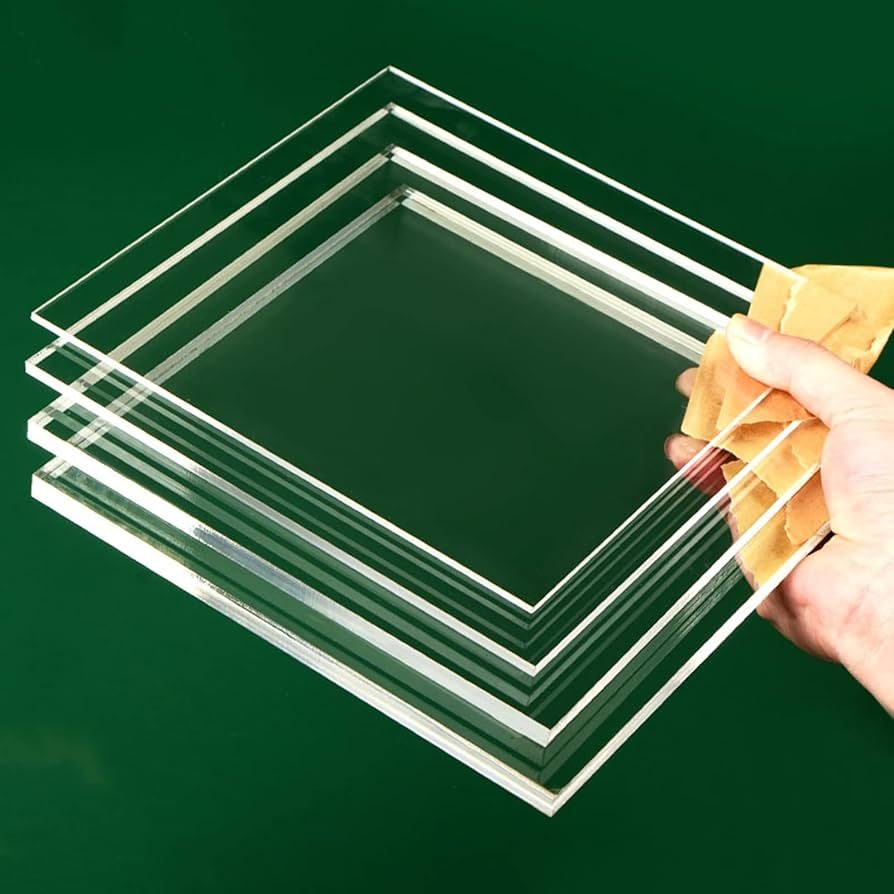
- Perspex: The manufacturing process of Perspex enables optimized transparency with fewer imperfections than standard acrylic sheets. Perspex is also ideal for high-precision applications like museum displays, art installations, and architectural features.
It’s the choice where flawless visual quality seems obligatory. In addition to optical excellence, Perspex may have advanced coatings to reduce glare or enhance light transmission. Such mechanisms also distinguish Perspex from generic acrylic materials.
c. Scratch Resistance
- Acrylic: Despite great persistence, scratch resistance isn’t one of acrylic’s strong attributes. Standard acrylic sheets, even impact-resistant ones, can develop surface scratches. It can derive from rough handling or exposure to abrasive materials.
This particular limitation makes regular acrylic less suitable for some applications. Frequent contact with chemicals or abrasives can damage the protective sheets without coating. Fortunately, it’s possible to polish out acrylic scratches using specialized products.
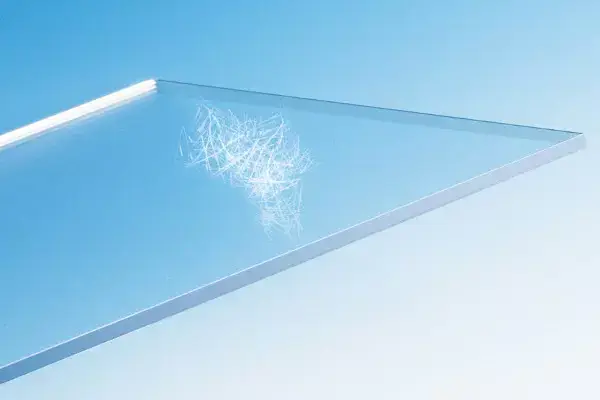
- Perspex: as a premium-grade acrylic, Perspex offers significant scratch resistance advancements. Some products are designed with enhanced formulations or surface coatings. Such treatments provide superior resistance to scratches than standard acrylic.
Perspex is valuable in high-traffic uses (retail displays, furniture, or automotive parts). Maintaining a flawless appearance is essential for such applications. The additional scratch resistance of Perspex minimizes maintenance for longer-lasting surfaces.
d. Price and Cost Efficiency
- Acrylic: Acrylic is more cost-effective than many, including Perspex and polycarbonate. That’s why it’s a popular choice for works with budget constraints. Acrylic can be manufactured in several methods (cast and extruded), allowing distinctive prices to suit different needs.
Extruded acrylic seems particularly economical compared to cast acrylic. This is because continuous production can effectively reduce total manufacturing costs. Large-scale projects with appearance and durability requirements can benefit from standard acrylic to a great extent.
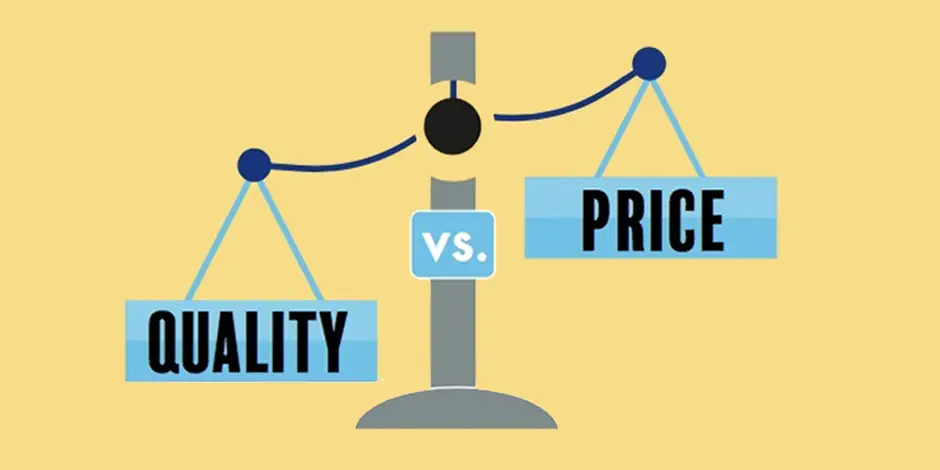
- Perspex: The high-quality branded acrylic version comes with higher pricing by default. The increased cost reflects stricter quality controls, superior consistency, and additional features. Higher scratch resistance or better optical clarity are two common characteristics.
Although Perspex comes with higher upfront costs, the material seems a worthy investment in tasks requiring flawless execution and longevity. The enhanced performance and longer lifespan can result in long-term savings, as it reduces repair or replacement needs.
e. Availability and Range
- Acrylic: Acrylic is broadly available in markets worldwide, thanks to its widespread manufacturing. The same goes for its near-universal use across various industries. Lots of manufacturers produce acrylic, resulting in diverse options and price ranges for different applications.
Acrylic sheets come in vast sizes, colors, thicknesses, and finishes. Such extensive ranges make the plastic an accessible and adaptable choice for creative and customized projects. Purchased acrylic can accommodate DIY enhancements even in smaller quantities.
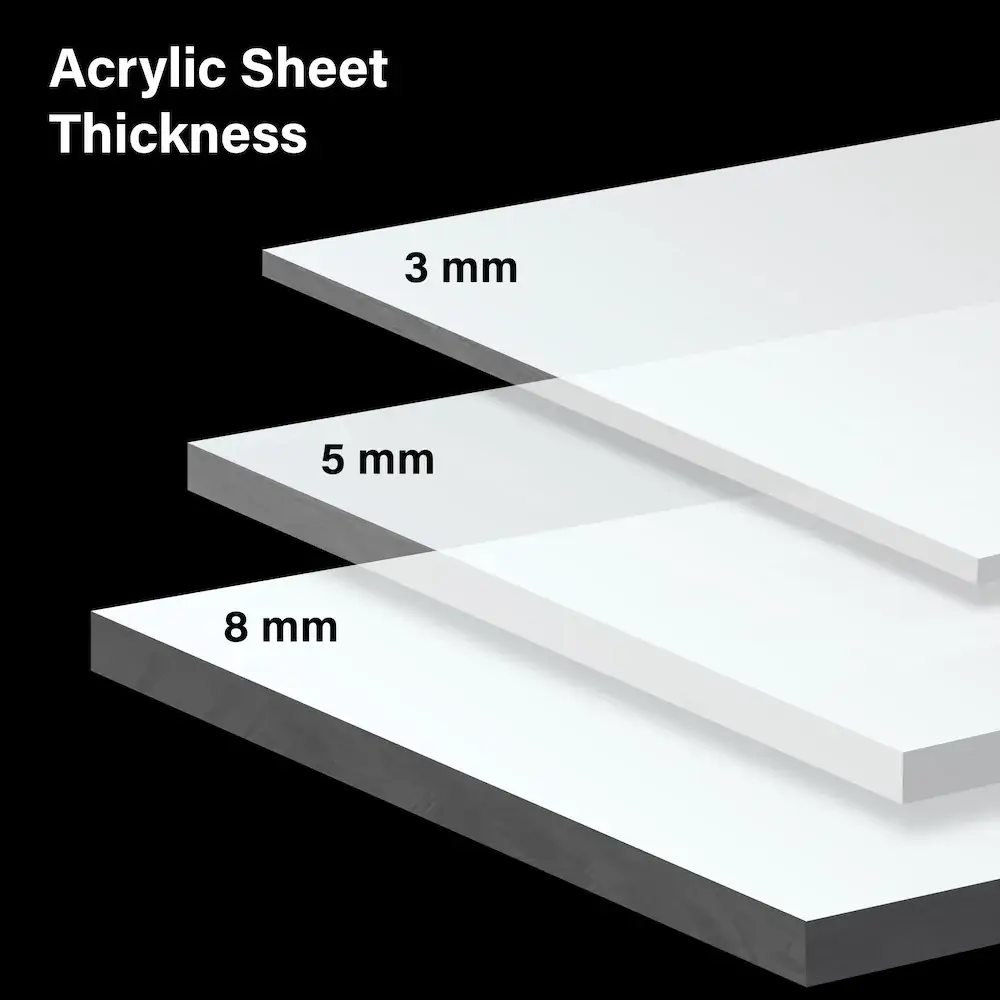
- Perspex: As a branded and quality acrylic product, Perspex is available through authorized suppliers. Its distribution network isn’t as expansive as generic acrylic. Still, Perspex is widely recognized in regions where premium materials are in demand (architecture and art).
Perspex sheets also offer a diverse range of options, including unique finishes. Luxury metallic, fluorescent, and high-impact formulations are available. But its availability may vary depending on location, often incorporating higher costs and limited access.
Acrylic vs Perspex: A Summarized Comparison
You may not feel interested in reading all the texts to understand them quickly. Check out the tabulated comparison to grab the key difference.
Feature | Acrylic | Perspex |
---|---|---|
Definition | A generic term for all forms of polymethyl methacrylate (PMMA) | A premium acrylic version, trademarked by Imperial Chemical Industries in 1934 |
Material Composition | Made from PMMA, with varying formulations depending on the manufacturer | Made from PMMA, but holds higher quality and specialized features |
Manufacturing Process | Usually produced through extrusion or casting methods | Primarily produced via cell casting for clarity and strength |
Optical Clarity | Excellent transparency, with a light transmission of over 92% | Superior transparency due to specified process |
Durability | Highly durable, resistant to impact and weather conditions | Better durability and resistance compared to generic acrylic |
Processing Methods | Molding, laser cutting, polishing, and cutting with saws for sheets, tubes, rods | Similar bending and cutting methods, aimed at highly precise length or edge |
Cost | More affordable and widely available | Higher cost due to premium quality and specialized features |
Applications | Used in signage, furniture, skylights, lighting fixtures, picture frames, and more | Ideal for high-end applications like aquariums, medical devices, and architectural designs |
Environmental Impact | Recyclable and UV-resistant, but environmental considerations vary by manufacturer | Recyclable, with additional environmental and safety considerations due to premium manufacturing |
Which Material Should You Choose: Acrylic or Perspex?
Choosing between acrylic and Perspex depends mainly on your project specifications. Either material offers unique benefits, requiring you to emphasize some key factors.
- Budget: Acrylic is more cost-effective for large-scale or budget-conscious projects. It comes with impressive functionality at a lower price point.
Perspex, however, features a premium price tag from the start. High-end quality and your willingness to invest can make Perspex a justifiable option.
- Project Requirements: Clarity can become crucial in selecting the ultimate material. When optical precision gets top priority, Perspex offers unparalleled consistency.
It should be your go-to choice for applications involving flawless visibility. Meanwhile, acrylic offers excellent clarity, but minor variations may occur depending on the production method.
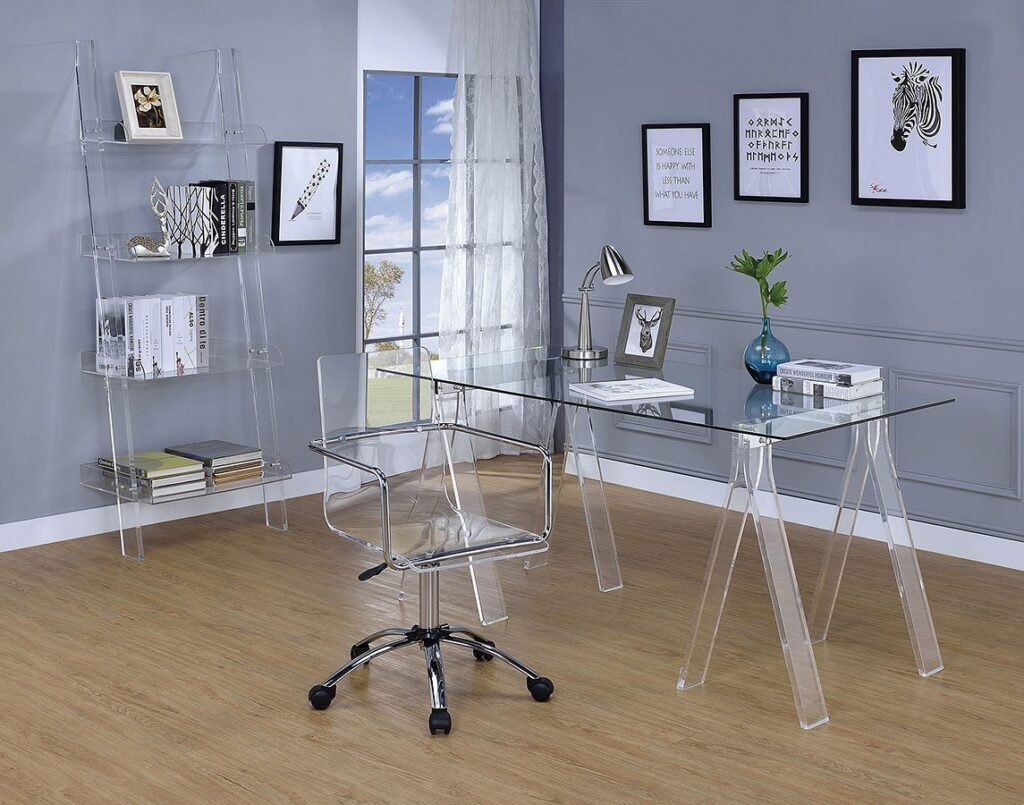
- Durability Needs: Some works remain exposed to heavy use or harsh conditions. And Perspex’s enhanced durability and scratch resistance make it the better choice.
It can withstand weathering and physical wear for years. Despite being durable and impact-resistant, it may not match Perspex’s scratch resistance or long-term resilience.
- Aesthetic Quality: Perspex receives more favors for luxury design and architectural and artistic tasks. It’s because of the premium finish and immaculate appearance required for high-end applications.
Perspex’s sophisticated appeal can benefit art displays, designer furniture, and luxury installations. Acrylic, while visually appealing, offers practicality and flexibility for more general uses.
Best Use Cases for Perspex
Perspex’s premium quality seems more matching for –
- Premium Retail Displays: High-end showcases where aesthetic excellence and durability are essential.
- Luxury Design: Designer furniture and architectural elements benefit from Perspex’s flawless finish and enhanced scratch resistance.
- High-Clarity Applications: Tasks involving optical precision like museum displays or cockpit windows.
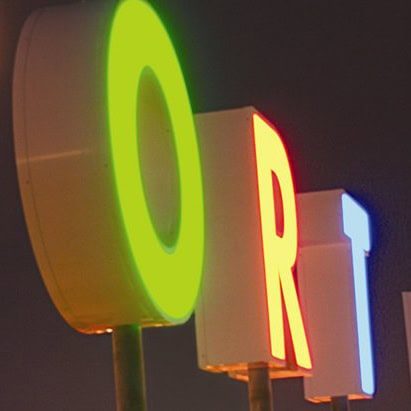
Conclusion
Acrylic and Perspex are chemically identical polymers. Likewise, they hold similarities in properties and advantages toward specific works. However, even the slight distinctions between the two made manufacturers and designers consider them differently.
Acrylic is affordable, versatile, and workable, whereas Perspex comes from a strict and sensitive process. The parent plastic suits cost-sensitive, large-scale, or general-purpose applications rather well. On that note, shop Perspex for high-end and luxurious projects.
Consult JUMEI ACRYLIC for Your Ultimate Solution
Many tasks can alternately utilize general acrylic and premium Perspex; you may need a clearer answer. That’s where Jumei Acrylic Manufacturing steps in with years of experience from industry-leading experts. Contact us to get valuable insights regarding your projects.