Glass sheets have been a fundamental material in many sectors for decades. From home renovations to architectural designs, automotive applications to industrial use, glass offers functionality and elegance. Among available sizes, 4×8 glass sheets stand out as a practical option.
The standard dimension (4 feet by 8 feet) with a well-balanced coverage is suitable for any project. Its adequate surface remains manageable for easy handling, transportation, and installation. This article holds valuable insights for a better understanding of 4×8 glass sheets.
What Are Glass Sheets?
Glass sheets are flat (transparent or translucent) materials made from silica sand, soda ash, and limestone. They incorporate impressive structural integrity, optical clarity, and customizing properties. Integrating mechanical strength, UV resistance, and thermal insulation is possible.
Its origin dates back to ancient Mesopotamia and Egypt. Early craftsmen created decorative items with naturally occurring glass. The first recorded glass sheets emerged in the Roman Empire. Artisans formed glass panels for windows. Stained glass became prominent in European cathedrals by the Middle Ages.
The float glass process, pioneered by Pilkington in the 1950s, revolutionized modern sheet production. It enabled the manufacturing of smooth and flawless glass surfaces. The process remains the gold standard in producing glass sheets for different industries today.
How Glass Sheets Are Manufactured?
Glass sheets are primarily made from three key ingredients. Silica (SiO₂) is the primary component to introduce transparency and rigidity. Soda Ash (Na₂CO₃) lowers the melting point of silica for efficient production. Limestone (CaCO₃) adds durability and prevents solubility in water.
These three raw materials are mixed and heated at extremely high temperatures. The temperature usually remains around 1,700°C (3,092°F) to form molten glass. Once melted, the glass is shaped using various processes to deliver distinct advantages to the intended applications.
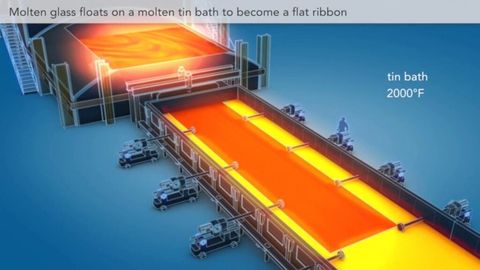
Common Manufacturing Processes for Glass Sheets
01. Float Glass Process: Molten glass is poured onto a bed of molten tin. The glass spreads evenly to create a smooth surface. The glass sheet is cut into precise dimensions after cooling.
02. Rolled Glass Process: Molten glass is passed through rollers to create textured or patterned surfaces. This method is mainly employed for frosted or decorative glass sheets.
03. Tempering Process: Regular glass is heated and rapidly cooled to increase strength. Tempered glass is four to five times stronger than standard glass.
04. Laminated Glass Production: Two or more glass sheets are fused with an interlayer [polyvinyl butyral (PVB)]. It improves strength while preventing shattering upon impact.
05. Annealing Process: Glass is slowly cooled to relieve internal stresses, preventing cracks and breakage. It’s a crucial step before glass sheets undergo further treatments.
Popular Glass Sheet Alternatives
Traditional glass sheets have immense applications in windows, doors, architectural designs, etc. Several alternative materials enhance durability, flexibility, impact resistance, and customization. Such substitutes can outperform glass in unique properties.
A. Acrylic Glass Sheets (Plexiglass)
It also goes by plexiglass, Lucite, and Perspex. The transparent thermoplastic sheets serve as a great alternative to glass. Lightweight acrylics provide superior resistance to impact and UV.
A high-end shop can prefer acrylic for light transmittance, longevity, and break resistance. It has extensive applications for fish tanks, sneeze guards, window panels, and safety shields.
B. Polycarbonate Sheets
The lighter plastic is literally unbreakable, with an enormous 250x more impact resistance than glass. The transparent plastics are often used for high-security and industrial applications.
The material is used in banks, police shields, and security enclosures due to its high strength. Modern greenhouses use polycarbonate sheets for light transmission and weather durability.
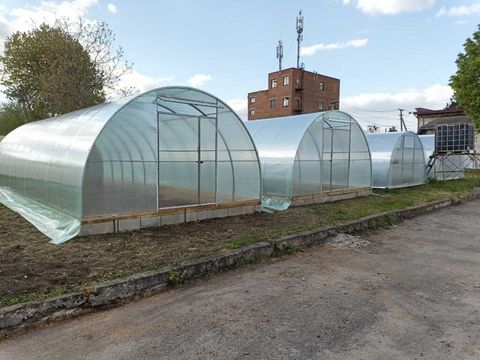
C. Tempered Acrylic Sheets
They go through heat and chemical treatments for additional toughness compared to standard acrylic. Tempered sheets don’t shatter upon impact but instead crack like tempered glass.
Due to weather resistance, bus shelters, airport screens, and advertising panels rely on tempered acrylic. It also has uses for entryway barriers, cashier shields, and museum display cases.
D. PETG Sheets
PETG (Polyethylene Terephthalate Glycol) is incredibly durable and flexible. These sheets are chemical-resistant, making them great for easy shaping and thermoforming.
Equipment enclosures in hospital settings and laboratories harness their sterilization capacity. Many factories and workshops use PETG sheets to shield from flying debris.
E. Laminated Glass Alternatives (Multi-Layer Plastics)
Such substitutes include multi-layer polycarbonate or acrylic. They offer soundproofing, shatter resistance, and UV protection. It makes them excellent for structural glazing and automotive uses.
Soundproof windows and doors in hotels, recording studios, and luxury homes have them. It’s even used in fighter jets and armored vehicles to incorporate high-security and durability.
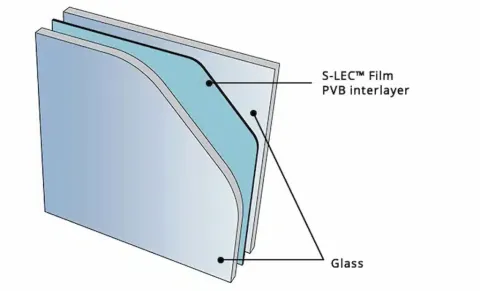
What Are Acrylic Glass Sheets?
You may think – plexiglass and glass seem like alternatives to each other. The transparent thermoplastic is lightweight, impact-resistant, and shatterproof to suit distinctive uses. Acrylic, scientifically known as polymethyl methacrylate (PMMA), was invented in the early 20th century.
The origin of PMMA traces back to 1928 when chemists at Röhm and Haas in Germany experimented with polymerization. By 1933, the company patented it under the name Plexiglas. Around the same time, similar materials were developed under brand names like Lucite (DuPont) and Perspex (Imperial Chemical Industries).
During World War II, acrylic sheets were widely used in aircraft canopies, submarine periscopes, and military vehicles. Over the decades, technological advancements refined the manufacturing processes. They integrated superior versatility for widespread commercial applications.
Common Manufacturing Processes for Acrylic Glass Sheets
I. Cell-Cast Acrylic Process: Pouring liquid acrylic into glass molds, allowing a slow cure at controlled temperatures. Cell cast holds higher clarity and better resistance for precision and durability.
II. Extruded Acrylic Process: Molten acrylic is continuously forced through rollers to form sheets of desired thickness. Extruded acrylic offers cost-effective solutions that are easy to cut and manipulate.
III. Injection Molding: It injects the PMMA into a mold to create complex shapes. While this isn’t used for standard sheeting, it allows manufacturers to produce special acrylic components like optical lenses.
IV. Thermoforming and Bending: Acrylics can be softened with heat and molded into curved shapes due to their thermoformability. It’s used for domed skylights, curved retail displays, and custom enclosures.
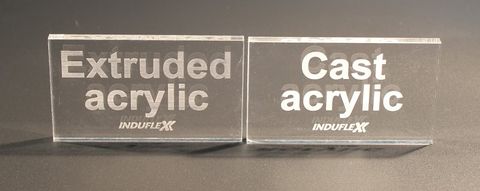
Why 4×8-Sized Sheets Are So Popular?
The 4×8 feet (48 inches by 96 inches) sheet has become the industry standard for glass and plexiglass (glass-like materials). For construction, interior design, signage, or industrial applications, the 4×8 format remains a go-to option for professionals and DIYers.
01. Standardization Across Industries
Standardized dimensions ensure easy compatibility between materials, tools, and installations. The 4×8 size aligns with standard building materials like plywood, drywall, and insulation panels.
Window manufacturers and glazing companies design products based on the 4×8 sheet format. It easily matches commercial or residential buildings’ standard wall openings and framing sizes.
02. Efficient Material Use with Minimal Waste
Cutting the materials into non-standard sizes often leads to high material wastage. The 4×8 format optimizes material efficiency, reducing offcuts, and ensuring cost-effective production.
Manufacturers can maximize the yield during fabrication with reduced scraps and costs. Acrylic signage from pre-cut 4×8 sheets enables effective material utilization for large advertising panels.
03. Easy Handling and Transportation
The format is large enough to cover significant surfaces. Still, the size allows for comfy handling, storage, and transportation. They easily fit into standard trucks, freight containers, and warehouse facilities.

Companies can stack 4×8 sheets flat on pallets almost anywhere to maximize logistics. Homeowners and hobbyists prefer them for custom cutting, without industrial equipment, which is one of the other advantages.
04. Versatility Across Applications
A 4×8 sheet is large enough for big projects yet small enough to be cut into smaller pieces for detailing. Such flexibility suits applications like windows, doors, protective shields, signage, and arts.
Designers use 4×8 sheets for seamless integration of glass walls, partitions, and curtain walls. Clear acrylic sheets provide large viewing panels for aquariums without clarity-affecting joints.
05. Compatibility with Cutting and Fabrication
Fabrication machines (CNC routers, laser cutters, and saws) are calibrated for 4×8 sheets. They make precise cuts for efficient shaping to enable cost savings, easy automation, and fast production cycles.
Large-scale billboards and storefront signs start as 4×8 acrylic sheets before getting cut into designs. Protective covers for machinery are cut from standard 4×8 sheets for seamless item manufacturing.
Types of Glass Sheets Available in 4×8 Dimensions
Glass sheets in 4×8 dimensions (4 feet by 8 feet) balance coverage, handling, installation, and efficiency. They come in various types to suit specific uses based on strength, clarity, insulation, and safety.
a. Float Glass: It’s the fundamental form of standard glass. The transparent, lightweight, and cost-effective choice lays the ground for many other types.
b. Tempered Glass: The heat-treated type increases strength (4x/5x stronger). It shatters into small, blunt pieces instead of sharp shards.
c. Laminated Glass: It consists of two or more layers of glass bonded with an interlayer like polyvinyl butyral (PVB). Such a structure prevents the glass from shattering upon impact.
d. Insulated Glass (Double-Glazed Glass): Two or more panes are separated by air or gas-filled spaces. It improves thermal insulation and reduces energy expenses.
e. Low-E Glass: Low-emissivity glass with the microscopic metallic coating reflects heat. It helps reduce UV exposure and improve energy efficiency.
f. Tinted Glass: It’s infused with color during production to reduce glare and heat absorption. Enhanced privacy comes from colors like bronze, gray, and green.
g. Wired Glass: A metal mesh is embedded within to prevent shattering and enhance fire resistance. Wired glass is commonly employed in fire-rated doors and industrial settings.
h. Frosted and Patterned Glass: They undergo acid etching or sandblasting to create opaque surfaces. It allows light to pass through while obscuring visibility.
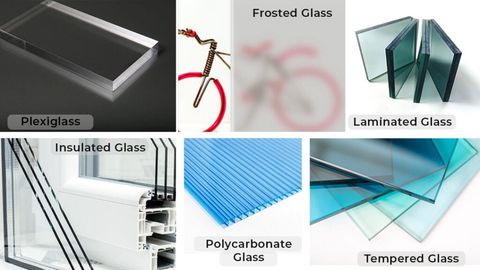
Acrylic Plexiglass vs Glass Sheet: Compare Plexiglass Against Glass
Feature | Glass Sheets | Acrylic Plexiglass |
---|---|---|
Material Composition | Silica-based amorphous solid | Thermoplastic (Polymethyl Methacrylate - PMMA) |
Transparency or Clarity | High optical clarity with slight color tint in thicker sizes | Excellent clarity, often clearer than glass in thicker sections |
Impact Resistance | Fragile, breaks into sharp shards upon impact | 10x/20x resistant than glass, doesn't shatter |
Weight | Heavy (about twice the weight of acrylic) | Lightweight (about half the weight of glass) |
UV Resistance | Standard glass allows UV to pass through unless treated | Naturally UV-resistant, ideal for prolonged outdoor use |
Scratch Resistance | Hard surface, highly resistant to scratches | Softer surface, somewhat poor scratch resistant (may need polish) |
Breakability | Excessively brittle, shatters into sharp pieces | Flexes under stress, cracks rather than shattering splinters |
Weather Resistance | Capable of withstanding extreme conditions with protective treatments | Excellent outdoor durability by resisting yellowing, weathering, or fading |
Ease of Fabrication | Harder to cut and shape, requires specialized tools | Easy to cut, drill, bend, and thermoform with basic tools |
Thermal Insulation | Low insulation (requires double-glazing for better performance) | Provides superior insulation compared to single-pane glass |
Chemical Resistance | Resistant to most chemicals | Can react to certain solvents, causing surface damage |
Fire Resistance | Non-combustible, withstands high temperatures | Flammable, but can be treated with fire-retardant coatings |
Cost | More expensive due to processing and treatments | More affordable for large-scale applications |
Common Applications | Windows, doors, furniture, mirrors, displays, skyscrapers | Signage, protective shields, aquariums, aircraft canopies |
Factors to Consider When Choosing the Best 4×8 Sheet
Making the better choice (from glass, acrylic, polycarbonate, or other) depends on multiple factors. Such critical measures ultimately decide the best sheet for your needs.
· Application Purpose
The foremost factor concerns your intended application. Do you want to install windows, wall partitions, protective barriers, signage, or decorative panels? You may have to consider alternatives to glass, like acrylic, for sensitive display cases.
· Strength and Impact Resistance
Some projects involve high-traffic areas, industrial environments, or potential impact risks. You’ll need a material good enough to endure force or pressure without breaking. Tempered glass is preferred for office partitions and commercial doors.
· Transparency/Optical Clarity
The level of transparency required varies across applications. Glass provides high optical clarity, but acrylic can sometimes offer better visibility in thicker sections. Jewelry stores and luxury brands often use low-iron glass for display cases.
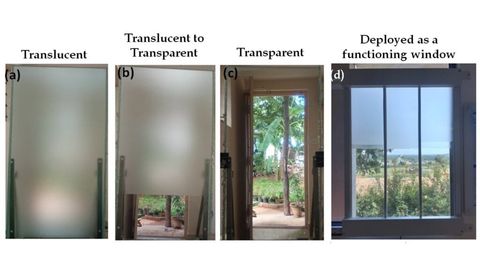
· Weather and UV Resistance
Outdoor applications require weather-resistant materials to withstand sun exposure, temperature fluctuations, and humidity. Many skyscrapers and high-rise office buildings use low-emissivity (Low-E) coated glass to improve energy efficiency.
· Weight and Ease of Handling
Consider lightweight alternatives like transparent plastics instead of heavy glass to ease handling. Traditional glass walls and partitions are notably heavier. But they offer a premium look, making glass ideal for upscale office environments.
· Safety and Shatter Resistant
Shattered glass results in shards with sharp edges that cause injury risks. Safety applications may get materials that neither shatter nor break. Most modern shower doors use tempered glass, whereas car windshields use laminated glass.
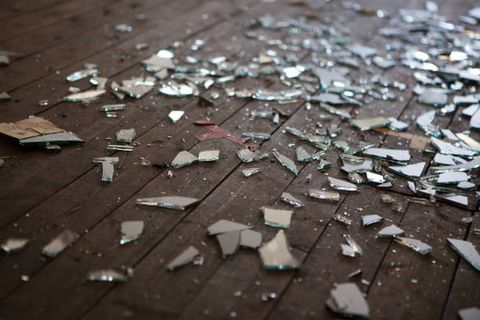
· Thermal Insulation and Energy Efficiency
Some projects involve temperature regulation (windows or partitions). Consider insulated materials for better heat retention or reduction. Many energy-efficient homes use double-glazed glass to maintain the indoor temperature without heating.
· Scratch Resistance and Maintenance
Some substitutes, like acrylic, are more prone to scratches than glass. Even a reckless wash can cause scratches on acrylic surfaces. That’s why restaurants prefer glass tabletops since glass is harder and less likely to scratch, regarding aesthetics.
· Cost and Budget Considerations
Overall expense (initial investment and maintenance costs) is crucial in material selection. Glass features a high initial investment against minimal maintenance. High-end offices or luxury hotels prefer glass due to its premium aesthetic.
How to Measure and Cut 4×8 Glass Sheets?
Precision is critical when working with 4×8 glass sheets. The correct measurement and cutting ensure safety, efficiency, and fit.
Step #01: Essential Tools and Safety Gear
Essential tools are – measuring tape/ruler, glass cutter, straight edge or T-Square, clamps, glass breaker pliers, sandpaper, or diamond file.
Important safety equipment – protective gloves to handle sharp glass edges, safety goggles to shield the eyes from splinters or flying debris.
Step #02: Accurate Measurement and Marking
- Define the Cut Dimensions: Determine the size for your project using blueprints or measuring guides. Ensure uniform dimensions for symmetrical results when cutting multiple sheets.
- Mark the Cutting Line: Use a non-permanent marker or wax pencil to mark the cut line for visibility. Align a straight edge or T-square along the marked line for an exact cutting guide.
Step #03: Scoring the Glass for Cutting
- Position the Glass on a Stable Work Surface: Lay the 4×8 sheet on a sturdy, flat workbench to avoid shifting or wobbling. Keep the sheet appropriately supported to prevent unnecessary stress.
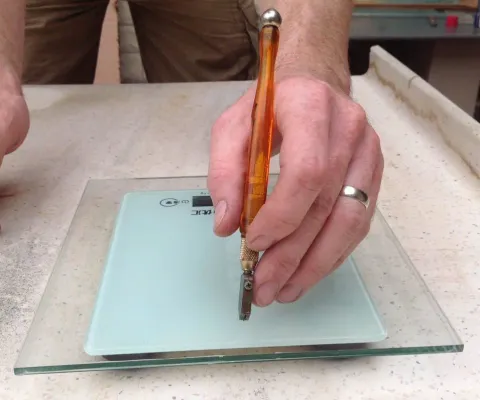
- Use a Glass Cutter to Score Along the Marked Line: Hold the glass cutter at a 45-degree angle for clean, deep scoring. Apply consistent pressure along the marked line for a continuous cut.
Step #04: Breaking and Separating the Glass
- Controlled Breaking Along the Score Line: Place the scored glass along a sharp edge or table corner. Apply quick but controlled pressure to snap the glass cleanly along the score.
- Breaker Pliers for Smaller Cuts: For narrow or intricate cuts, use glass breaker pliers to avoid unwanted fractures. Apply gradual pressure from one end to the other for a clean separation.
Step #05: Smoothing the Edges with Final Adjustments
Use sandpaper or a diamond file to remove sharp edges and smooth the cut surfaces. Apply polishing compound for clarity and refinement in aesthetic projects. Check whether the final dimensions match your project’s requirements before installation.
Conclusion
Selecting 4×8 glass sheets feels like a game-changing decision regarding functionality and aesthetics. Even with the standard sizes, there are numerous types to serve distinct purposes. Standard glass may have sleek sophistication, but coated, tinted, or soundproof glass provides superior performance. Understand strength, durability, weight, fabrication, and usability for a practical and preferable solution.
Get High-Quality Acrylic for Aesthetic Appeal from JUMEI
There are many reasons to consider lightweight materials like acrylic for glass-like uses. Only the top acrylic products can meet the satisfaction firsthand. Jumei Acrylic specializes in acrylic items for different settings. Contact us to know how and why you should get acrylic for the next project.